In the vast panorama of industrial manufacturing, nitrogen in laser cutting emerges as a remarkable thermal process, akin to a precise and nimble artisan, carving out a niche with its extensive applications. Laser cutting machines, with the assistance of nitrogen gas, can swiftly engrave and cut metal sheets, even those bearing the most intricate and elaborate shapes, bestowing upon them a finish of the highest quality, much like an expert craftsman adding the final changes to a delicate piece of art.
Within this comprehensive wiki article, we shall embark on a journey to explore the laser cutting process, its diverse techniques, and the crucial assist gases, namely nitrogen, oxygen, and compressed air. This exploration is designed to unravel the mysteries of how this process functions and to shed light on the manifold benefits it offers, guiding you through the labyrinth of laser cutting knowledge.
What Constitutes Laser Cutting?
Laser cutting is a sophisticated process that employs a high-power laser, meticulously directed by computer numerical control (CNC) through the conduit of optics, to slice through materials. This technique has permeated a multitude of industries, such as the automotive sector, which resembles a bustling metropolis of mechanical innovation; the aerospace domain, a realm where dreams of reaching the heavens are fabricated; the electronics field, a digital wonderland of micro-components; and the medical arena, a life-saving bastion of precision instruments. It is used to cut a wide array of materials, including metals that are as sturdy as ancient fortresses, plastics as pliable as soft clay, ceramics with their brittle yet resilient nature, wood that holds the warmth of nature, fabrics as delicate as gossamer, and paper as thin as a whisper.
During laser cutting, a focused laser beam, like a searing ray of concentrated sunlight, is utilized to melt material within a localized area. With the invaluable assistance of a co-axial gas jet, which acts as a vigilant guardian, a kerf is created. The laser beam, impervious to the gas like a fearless knight in shining armor, can effectively burn, melt, or vaporize materials. Meanwhile, any debris that emerges is promptly blown away by the gas jet, ensuring that the finished edge is as smooth and flawless as a polished mirror, a testament to the high quality of the cut.
Laser cutting also dons multiple hats, being applicable for welding and etching. The three principal techniques in laser cutting are the CO2 laser, which is like a steady and dependable workhorse; the neodymium (Nd) laser, a vibrant and energetic performer; and the neodymium yttrium-aluminum-garnet (Nd:YAG) laser, a refined and precise virtuoso. The choice of laser type can significantly influence the performance, much like the selection of a musical instrument can alter the melody. The advantages of laser cutting are as numerous as the stars in the sky, encompassing precision that rivals the accuracy of a Swiss watchmaker, reduced contamination that keeps the workspace as pristine as a freshly cleaned room, and easier work holding that simplifies the process like a well-oiled machine. Fiber lasers stand out with their superior precision cutting capabilities. They possess the remarkable ability to deliver a consistent beam quality over long distances, like a lighthouse casting a steady beam across the vast ocean, enabling uniform cutting across various materials and thicknesses. This consistency is the cornerstone of superior edge quality, minimizing the need for secondary processing like a well-planned journey that requires few detours.
How Does a Laser Cutting Machine Operate?
A laser cutting machine functions by orchestrating a high-powered laser beam, guiding it through the optical pathways and onto the material slated for cutting. The laser beam, focused through a lens like a magnifying glass concentrating sunlight, is projected onto the material. The rapid temperature rise, akin to a sudden burst of heat in a desert, causes the material to melt or vaporize within a localized area. Subsequently, a co-axial gas jet, acting as a dutiful sweeper, removes the molten material and carves out a kerf. This gas jet also serves as a cooling balm, preventing the material from warping or distorting, much like a cool breeze soothing a heated object. The laser cutting machine is under the meticulous control of a computer numerical control (CNC) system, which ensures the precision and accuracy of the cutting process, like a conductor leading an orchestra to produce a harmonious symphony.
What Are the Assist Gases in Laser Cutting?
Assist gases play a pivotal role in laser cutting, enhancing the quality and efficiency of the process like a catalyst in a chemical reaction. They assist in blowing away the molten material, preventing it from re-solidifying on the material's surface like a vigilant sentinel warding off unwanted intruders. Additionally, they help cool the material, safeguarding it from warping or distorting, much like a protective shield. The most utilized assist gases in laser cutting are nitrogen, oxygen, and compressed air, each with its unique characteristics and applications.
1. The Utilization of Nitrogen in Laser Cutting
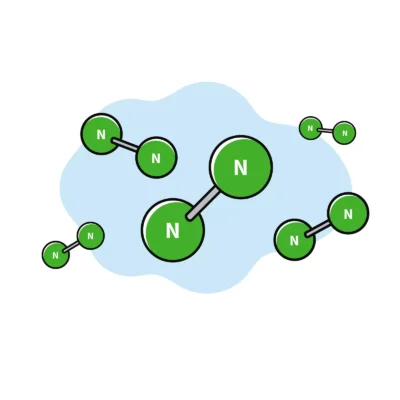
Nitrogen reigns supreme as the most widely employed assist gas in laser cutting, owing to its inert nature, which is as stable and unresponsive as a stoic mountain. It is the go-to choice when a high-quality cut is essential, ensuring the laser performs at its peak, much like a well-tuned instrument producing a flawless melody. Nitrogen expels oxygen from the air, thwarting any reaction between the hot metal and oxygen, thus yielding a perfect, shiny cut. It leaves the color of the material unblemished, like a gentle touch that preserves the original hue (although this is contingent upon the purity of the nitrogen used). Nitrogen gas, in its inert state, acts as a guardian angel, preventing the cut edge from oxidizing by creating an oxygen-free environment for the laser to operate in. Moreover, nitrogen is a boon for cost reduction, akin to finding a hidden treasure chest; it boosts cutting speed, heightens productivity, offers better control, achieves the highest efficiency, provides on-demand availability, and presents a convenient plug-and-play solution, making it an all-round champion in the laser cutting arena.
2. The Application of Oxygen in Laser Cutting
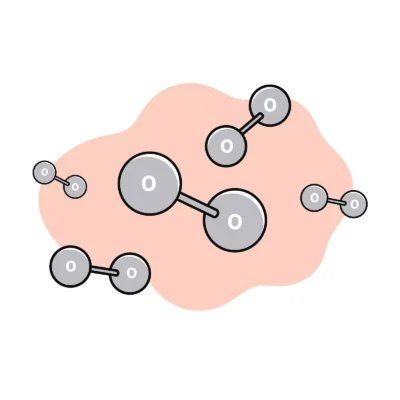
Oxygen is summoned in laser cutting to tame materials that prove recalcitrant to other cutting methods, like a fearless warrior facing a formidable foe. It is a highly reactive gas, and when it enters the fray, it triggers an exothermic reaction, multiplying the power of the laser beam like a magnifying force. This allows for the cutting of thicker materials, breaking through barriers like a battering ram. Oxygen engages in a chemical dance with the material being cut, helping to melt and vaporize it. Depending on the material, it can also accelerate the cutting speed and trim the cost of the process, like a skilled navigator finding the quickest route. However, oxygen has a downside. It can cause oxidation, leading to the formation of a carbon layer on the cut edge, which is like a dark shadow marring the otherwise pristine finish. This can result in adhesion problems for any coating or paint applied to the oxidized surface, much like a rough patch on a smooth surface. Due to its high reactivity, achieving very thin slices with oxygen is as elusive as catching a fleeting shadow.
3. The Employment of Compressed Air in Laser Cutting
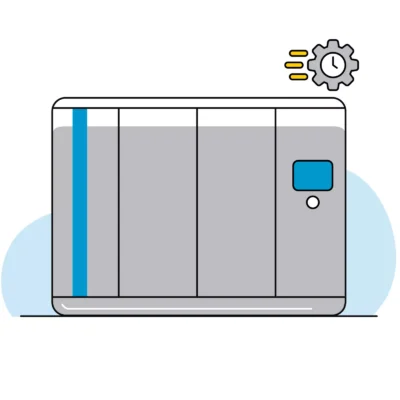
Compressed air can also take on the role of an assist gas in laser cutting and offers a faster and more cost-effective alternative, like a budget-friendly shortcut. However, it falls short when it comes to obtaining parts with immaculate cuts, as air contains 21% oxygen in its composition, which is like a tiny flaw in an otherwise useful tool. Normally, these parts require deburring before the next process, adding an extra layer of labor, much like an additional hurdle in a race. But for parts that will be painted or welded later, where the color of the forefront is of little consequence, these cuts are acceptable, like a passable compromise.
What Are the Typical Assist Gas Purities?
The purity of the assist gas hinges on the customer's discerning requirements for the final product, much like a tailor customizing a garment to fit perfectly. However, we must bear in mind the following:
- If we resort to atmospheric air, its purity remains unalterable, with 78% nitrogen and approximately 21% oxygen, a fixed recipe in nature's cookbook.
- When using oxygen, the purity soars above 99.5%, like a refined and purified elixir.
- In the case of nitrogen, its purity is contingent upon numerous factors such as the material to be cut, whether the material will undergo further treatment, and the significance of the cutting edge's color, among others. It is a delicate balance, much like adjusting the ingredients in a complex recipe.
It is worth noting that by tempering the purity of nitrogen, we can significantly slash costs, like trimming the excess fat from a budget.
Can an Assist Gas like Nitrogen be Generated On-Site?
Indeed, it is not only possible but also highly advantageous to generate your own assist gas, such as nitrogen, within the plant's confines. By integrating a high-pressure gas generation system into the facility, companies can ensure an unceasing supply of gas, available around the clock, 24/7, like a never-ending stream of energy. This approach not only trims operational expenses like a sharp pair of scissors cutting through unnecessary costs but also affords complete dominion over gas consumption, like a captain steering a ship. Furthermore, by eliminating the need for truck transportation, companies can curtail CO2 emissions, making a significant contribution to environmental sustainability, like planting a forest of green hope.
Nitrogen Generators for Laser Cutting
Nitrogen generators are the unsung heroes in optimizing laser cutting operations, offering a plethora of practical benefits. There are two types: membrane and PSA (Pressure Swing Adsorption) nitrogen generators, which possess the remarkable ability to achieve exceedingly elevated levels of purity, like alchemists transforming base substances into pure gold.
Businesses that utilize nitrogen in laser cutting can achieve substantial cost savings by generating their own nitrogen supply, liberating themselves from the shackles of external purchases, like a bird breaking free from a cage. This in-house production also confers greater control over nitrogen purity, guaranteeing a consistent quality without being at the mercy of external suppliers, like a self-sufficient farmer relying on his own bountiful harvest.
Moreover, by producing nitrogen on-site, companies play their part in environmental sustainability by reducing transportation emissions and minimizing reliance on traditional nitrogen production methods, like a conscientious citizen taking steps to protect the planet. Overall, the use of nitrogen generators is a sagacious choice for companies aiming to augment efficiency and shoulder environmental responsibility in laser cutting processes, like a wise leader guiding their team towards success.
High-Pressure Compressors and Boosters for Laser Cutting
Laser cutting machines frequently rely on compressed air or gases to fulfill diverse functions, including powering the laser itself, much like a heart pumping blood to keep the body alive. High-pressure compressors and boosters supply the essential compressed air or assist gases like nitrogen in laser cutting for the process. They function as dependable powerhouses, ensuring a consistent and reliable power source for the laser, which in turn contributes to stable and precise cutting, like a firm foundation supporting a towering structure. High-pressure compressors are used to compress gases such as nitrogen or oxygen for assisted laser cutting. The pressurization of assist gases, especially nitrogen, augments the laser cutting process, facilitating the delivery of high-pressure gases to the cutting head for optimal performance, like a well-designed pipeline ensuring the smooth flow of water to a thirsty field.
Laser cutting systems often incorporate high-pressure compressors or boosters as integral components of an integrated solution, streamlining and optimizing the setup for laser cutting applications, like a seamless jigsaw puzzle coming together. Integrating high-pressure compressors with laser cutting systems presents a comprehensive solution for your industrial needs, like a Swiss Army knife offering a multitude of useful tools in one compact package.
Reviewed by 1 user
The article on nitrogen’s role in laser cutting provides a comprehensive overview of how this inert gas enhances the cutting process,krrass does the best