The choice of press brake tooling is an important one that has a direct effect on the effectiveness and caliber of your output. Making the incorrect tooling choice might result in increased expenses, poor precision, and operational delays. In this post, we'll examine how to choose wisely by understanding the main categories of press brake tooling and the ideal procedures to adhere to for the best outcomes.
Achieving correct bending results and preserving production efficiency depend on selecting the proper press brake tooling. This book helps you make well-informed judgments that save time and money by breaking down the fundamental types of press brake instruments and important guidelines to adhere to.
Table of Contents
Introduction
In the metalworking sector, press brake tooling is essential for precisely bending sheet metal into the required shapes and forms. The correct tooling choice can have a significant impact on the precision, caliber, and productivity of your production process, regardless of how complicated or simple the bends are. However, using the incorrect tooling choice can lead to a number of problems, such as greater material waste, longer production times, and lower-quality products. Bad tooling decisions can also result in higher maintenance, rework, and tool replacement expenses.
Perfecting your manufacturing process requires knowing the several kinds of press brake tools that are available, such as V-dies, punches, and clamping systems, and knowing how to choose the best ones for your requirements. The kind, thickness, bend radius, and machine compatibility of the tooling you select must all be in line. This article will examine the main determinants of tooling selection and offer advice on how to select the best tools for your press brake operations, guaranteeing both cost-effectiveness and long-term efficiency.
Types of Press Brake Tooling
Press brake tooling comes in a variety of forms, each with a distinct function depending on your manufacturing requirements. Let's examine the most prevalent kinds:
1. V-Dies (Die Sets)
One of the most important parts of press brake tooling is the V-die. By keeping the material while the punch applies force, these dies are employed to create the bends. The bend angle and radius are decided by the die's V-shaped profile. To manage a range of material types and thicknesses, V-dies are available in a variety of sizes and configurations.
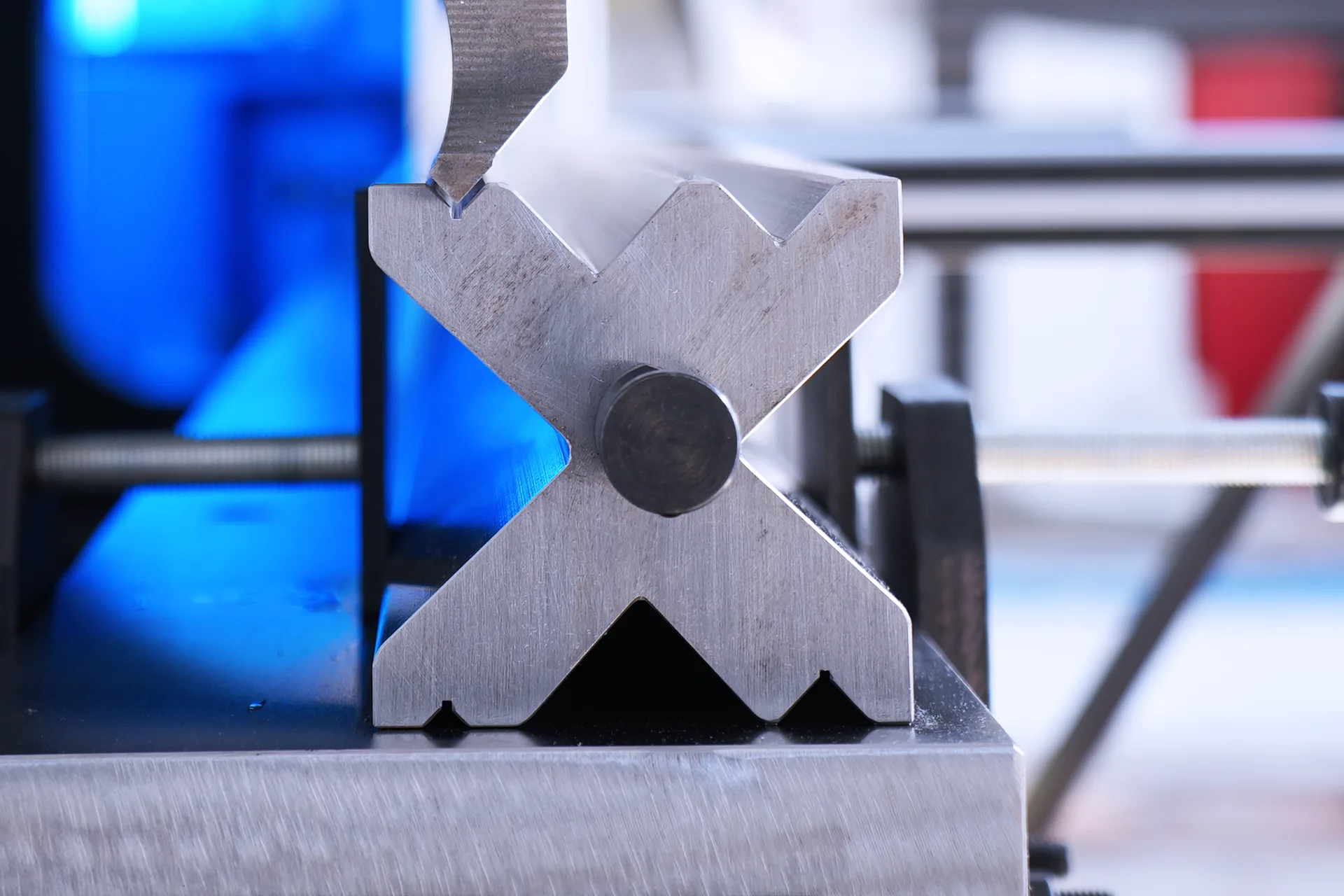
- Function: Helps to support and guide the material while it is being bent.
- Frequently Used: Used in nearly all metalworking processes, ranging from simple to intricate bends.
- Benefits: Easy to use, reasonably priced, and incredibly adaptable.
2. Punches
In contrast to dies, punches are used to exert force on the material while it is being bent. Depending on the kind of bend that is needed, punches come in a variety of sizes and forms. Hemming punches, single V-punches, and multi-V-punches are common punch types. To get the proper bend, punches are usually used in conjunction with V-dies.
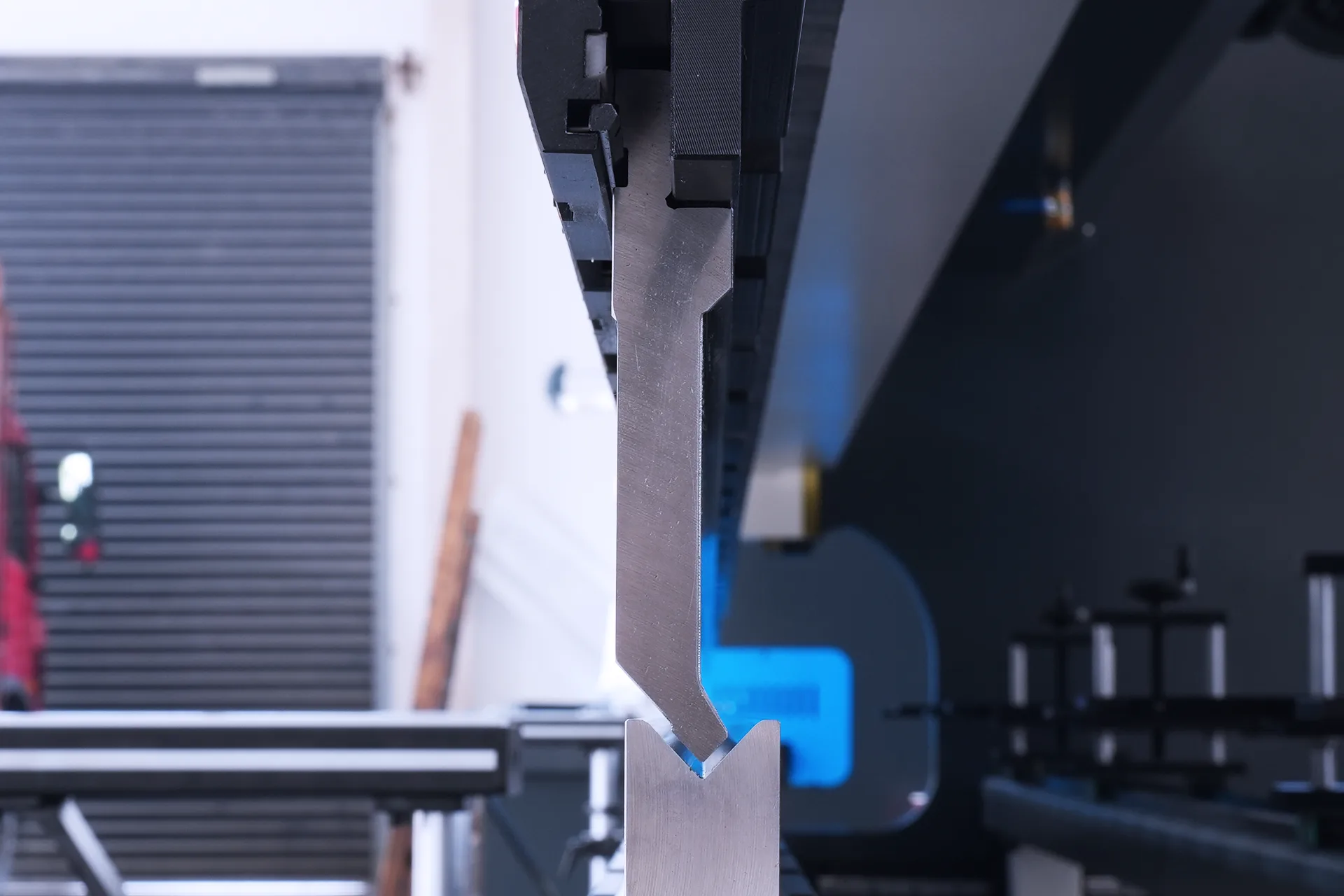
- Function: Produces a bend by applying force to the material.
- Frequently Used: For precisely and carefully bending sheet metal.
- Benefits: Comes in a range of sizes and forms to accommodate varied bending degrees and materials.
3. Specialty Tooling
Custom tooling made to satisfy, intricate, or unusual bending needs is known as specialty tooling. Tools made for certain materials (such as heavier metals or materials that are difficult to bend) or for specialized tasks like punching, notching, or creating complex shapes can fall under this category.
- Function: Made to do bending jobs that are beyond the capabilities of conventional tools.
- Frequently Used: For extremely specialized or difficult applications.
- Benefits: Offers customized solutions for certain manufacturing requirements, increasing accuracy and flexibility.
4. Gooseneck Tooling
Deep bends or pieces with narrow interior radii are bent using gooseneck tooling. These tools include a characteristic gooseneck shape, allowing the punch to reach portions of the material that are difficult to access with standard tooling.
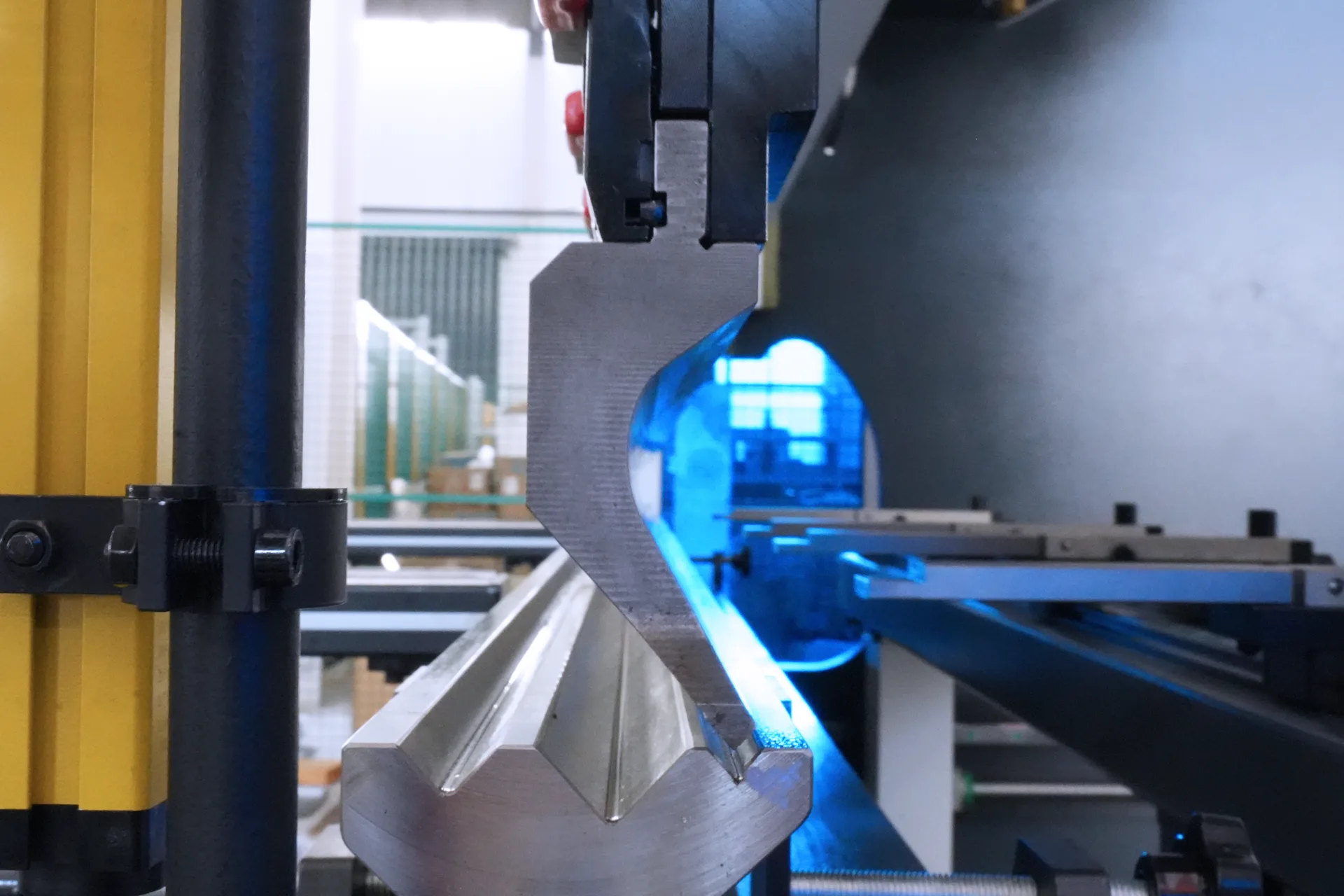
- Function: Provides access to difficult-to-reach places, enabling deep or tight bends.
- Frequently Used: For intricate, very precise tasks like creating deep bends.
- Benefits: Increases bending flexibility without sacrificing material integrity.
5. Folding Tooling
The purpose of folding tooling is to bend sheet metal without producing a large bend radius. These tools are employed in folding operations, which are often used to create boxes or enclosures, where the metal is bent so that the material folds over itself.
- Function: Enables a folding action without the formation of a conventional bend.
- Frequently Used: Often used in the construction of boxes or enclosures and pieces that don't have sharp edges.
- Benefits: Increases material efficiency by enabling complex folds and low-radius bends.
Factors to Consider When Choosing Press Brake Tooling
Choosing the proper press brake tooling needs a thorough comprehension of your manufacturing requirements. Consider the following elements:
1. Material Type and Thickness
When selecting press brake tooling, one of the most crucial considerations is the material you're working with. The qualities of various materials (such as brass, aluminum, stainless steel, and mild steel) influence how they bend. Since it dictates how much power is needed to bend the material, the thickness of the material is equally significant.
Material Type: Depending on their characteristics, certain materials may need specialist tools or are more likely to break. For instance, because stainless steel is harder than softer materials like aluminum, it could require a more durable punch and die system.
Material Thickness: Stronger tooling that can sustain more force is needed for thicker materials. For efficient handling of these materials, you might need larger or more robust dies and punches.
Consideration: To avoid early wear and guarantee precision, always make sure the tooling you choose is proper with the kind and thickness of material you want to work with.
2. Bend Angle and Radius
Material | Minimum Bend Radius |
---|---|
Aluminum | 6t |
Bronze | 4t |
Brass | 2t |
Magnesium | 13t |
Stainless Steel | 6t |
Carbon Steel | 4t |
Titanium | 3t |
Crucial elements that affect the accuracy of your produced pieces are the bend angle and radius. Different bend radii and angles are managed by diverse types of tooling. It is crucial to consider when choosing:
Bend Angle: Certain tools, like V-dies, are made to manage bend angles. The ultimate result of the bend will depend on the die's size and form.
Bend Radius: The bend's radius is just as significant. For instance, different tooling is needed for severe bends compared to mild or wide-radius bends. For tight bends, specialty tooling—like gooseneck tooling—is often used.
Consideration: To guarantee precise, clean bends free of material distortion, select tooling that satisfies the project's necessary bend standards.
3. Tooling Compatibility with Press Brake Machine
For seamless operation, make sure the tooling you select is proper for your press brake machine. Not every equipment is made to fit every machine, and press brakes come in a variety of sizes and styles.
Machine specs: Your press brake's dimensions and tonnage ability should match the equipment you want to employ. For instance, bigger dies may be needed for a large hydraulic press brake than for a smaller mechanical press.
Machine Control: Make sure your tooling is compatible with the machine's control system if you're using a CNC press brake. More correct tooling is often needed for CNC machines, and the machine's capabilities should be taken into consideration while selecting it.
Consideration: Make sure the tooling is made to fit your press brake model by always consulting the machine's specs. This will reduce problems like tool wear and misalignment.
4. Precision and Tolerances
Your choice of tooling will depend on how precise your bending process must be. While certain projects could allow for greater flexibility, others would require strict standards. For example, CNC press brakes are renowned for their extreme accuracy, and the tooling used must take this requirement into account.
Tolerances: High-precision tooling that can sustain steady performance over time is necessary to meet tight tolerances. Better-fitting dies and punches that guarantee less variation are common components of precision tooling.
Material handling: Because thin materials are more likely to be damaged during bending, high-precision tooling is especially crucial.
Consideration: Use CNC press brake tooling and custom dies to keep tight tolerances and lower the chance of mistakes if your project requires an elevated level of precision.
5. Tooling Durability and Maintenance
One crucial factor to consider while choosing press brake tooling is durability. A longer lifespan and fewer replacements are possible with high-quality tooling since it can lessen wear and strain. To guarantee the long-term efficacy of tools, routine maintenance is also crucial.
Durability: Long-term performance and longevity are enhanced by tooling composed of premium materials like tungsten carbide or high-strength steel.
Maintenance Requirements: Tools must be simple to clean and keep. The tooling's lifespan may be increased and the expenses related to frequent replacements can be decreased with proper maintenance.
Consideration: To perfect tool longevity and performance, select long-lasting tooling materials and make sure your team has proper maintenance procedures in place.
6. Production Volume and Speed
Your choice of tooling should also be influenced by the operation's needed speed and production volume. Tooling that is more robust and made for speedier setups and cycle times can be something you want to think about for high-volume operations.
High-Volume Production: Press brakes that are hydraulic or mechanical and with high-speed tooling could be more proper for production settings that move quickly. Additionally, productivity can be increased using quick-change dies and punches.
Low-Volume or bespoke Bending: Although more expensive, more adaptable tooling (like CNC equipment) may be needed for low-volume or bespoke operations to accommodate a variety of bending angles and forms.
Consideration: To prevent bottlenecks and downtime, match tooling to the volume and speed needs of your production.
7. Cost Efficiency
While high-quality tooling can offer long-term savings through reduced wear and fewer replacements, it is essential to balance quality with cost. Consider the following:
Initial Cost: Although higher-quality instruments may cost more up front, they often last longer and require fewer replacements over time.
Long-Term Cost: Consider the whole cost of ownership, which includes upkeep, repairs, and lost productivity.
Consideration: To make an educated choice that strikes a balance between operational requirements and financial limitations, evaluate the tooling's first and ongoing expenses.
8. Supplier Reliability and Support
For operations to run smoothly, selecting a trustworthy supplier that can offer top-notch tools and support is crucial. A trustworthy vendor ought to provide:
Technical Support: Downtime may be greatly decreased by having access to professional guidance and help with tool setup, maintenance, and troubleshooting.
Quality Assurance: Verify that the tooling supplied by the supplier satisfies industry standards and is supported by guarantees or warranties.
After-Sales support: You can keep the efficiency of your production by collaborating with suppliers who provide prompt replacements for damaged tools and attentive after-sales support.
Consideration: Collaborate with vendors who are well-known for offering top-notch customer service and high-quality tools.
Rules to Follow for Effective Press Brake Tooling Selection
Use these important guidelines to make sure that the tools you choose will result in accuracy and efficiency:
Quality Control: Always give top priority to top-notch equipment that satisfies industrial requirements. Tools that are well-made endure longer and yield greater outcomes.
Tooling Maintenance: It's important to keep your tools properly. Your tools can last longer and remain in best operating condition with routine cleaning, lubrication, and inspection.
Supplier Reliability: Select a dependable provider who has a history of on-time, high-quality tool delivery. Preventing manufacturing delays requires effective communication and post-purchase support.
Cost Efficiency: The whole cost of ownership must be considered, even when quality is crucial. Longer-lasting, high-quality instruments could be more affordable than their less expensive counterparts.
How to Maintain Your Press Brake Tooling
The longevity of your press brake tooling depends on routine maintenance. Here are some pointers:
1. Regular Cleaning
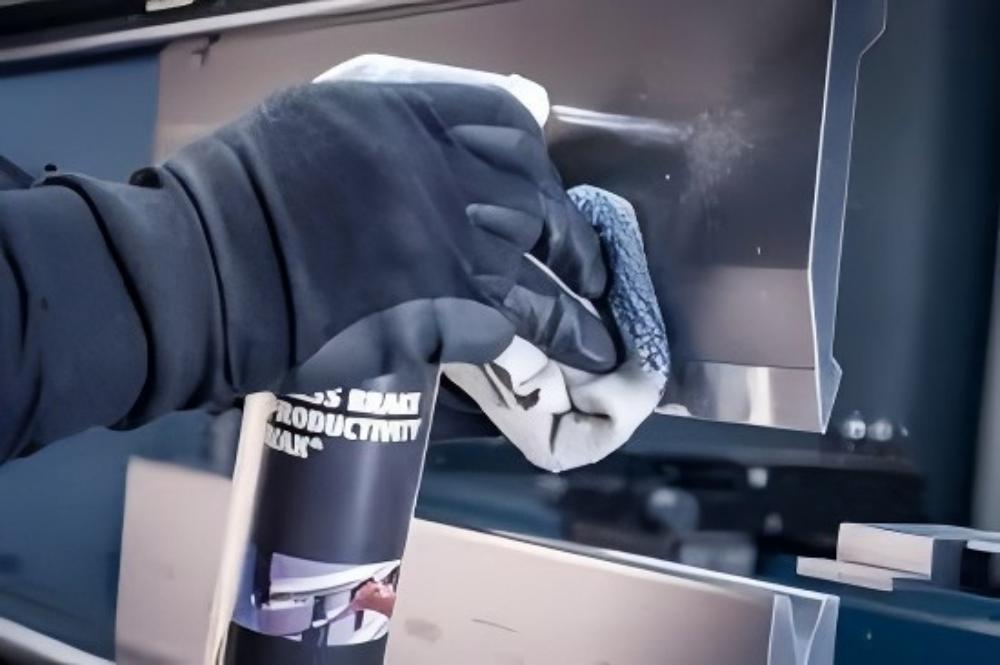
The first and most crucial step in preserving the functionality of your tools is to keep it clean. Debris, dust, and dirt can harm the tooling, result in uneven wear, and compromise the precision of the bends. To avoid accumulation, cleaning should be done after every manufacturing run.
Action: Clean the dies, punches, and clamping mechanisms using a gentle cloth or brush. Avoid abrasive materials that could scratch or harm the instruments' surface.
Why It Is Important: Frequent cleaning stops metal shavings and other impurities from building up, which can erode tooling and lessen its performance.
2. Lubrication
Wear and tear are reduced when the tools and the material being bent have less friction thanks to proper lubrication. By making sure that the dies and punches slide smoothly, it also enhances bending accuracy and keeps operations running smoothly.
Action: As part of your regular maintenance program, lightly lubricate the die, punch, and clamping system surfaces. Make use of lubricants made especially for press brake applications.
Why It Is Important: Lubrication prolongs the life of your tools by lowering friction and avoiding excessive heat accumulation, which can lead to tool failure or deformation.
3. Inspect for Wear and Damage
To find wear or damage early on, you must regularly examine your press brake tooling. Tooling may eventually show wear indicators like chipped edges, fissures, or distorted regions, particularly after extended usage in high-volume manufacturing.
Action: Frequently inspect the tooling for obvious wear indicators like fractures, nicks, or uneven surfaces. Because they are most likely to wear, pay close attention to the dies' edges and the punch faces.
Why It Is Important: Early wear detection and repair helps shield the tooling from considerable damage and guarantees constant production quality. Inaccurate bends and worse product quality might result from worn tooling.
4. Ensure Proper Storage
When not in use, tooling must be stored properly to avoid corrosion, damage, or distortion. When tools are stored incorrectly, they may distort or corrode, especially if they are exposed to moisture or extremely high or low temperatures.
Action: By keeping tools in a dry, temperature-controlled space. To keep equipment from being chipped, damaged, or exposed to dangerous conditions, use cabinets, tool racks, or protective coverings. Additionally, to prevent bending or warping, place heavier tools on shelves that can sustain its weight.
Why It Is Important: In addition to preventing avoidable corrosion or damage, proper storage guarantees that your tools will still be in good condition when you need them.
5. Check Tool Alignment
Accurate and precise bends depend on the tools being properly aligned. A finished product with misaligned dies or punches may have irregular bends, mistaken angles, or even tool damage.
Action: Verify that the press brake machine's tooling is aligned before beginning a fresh manufacturing run. To prevent any misalignment during bending, make sure the dies are appropriately installed in the machine and that the punch and die are lined up.
Why It Is Important: The quality and accuracy of the bends are enhanced by proper alignment, which guarantees that the tooling distributes force uniformly throughout the material.
6. Monitor Tooling Performance
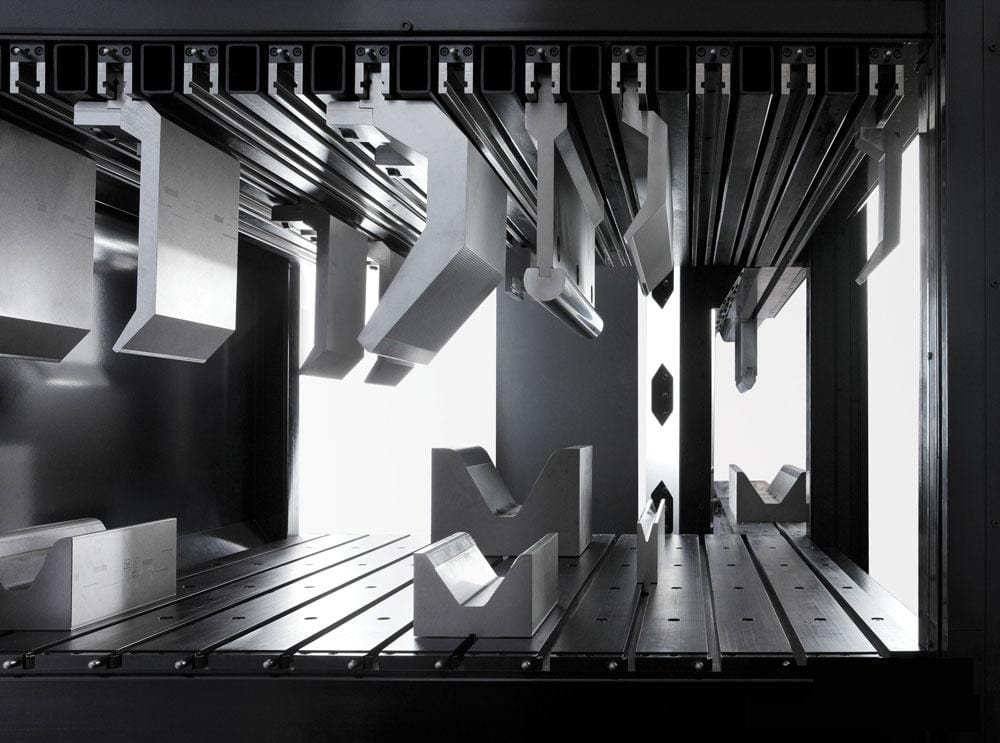
Long-term usage may cause a minor decline in tooling performance. You may find problems early and take remedial action before they worsen by keeping an eye on how well your tooling is doing throughout production.
Action: Throughout operation, keep an eye out for any indications of strange noise, vibration, or trouble bending the press brake. These can be early indicators that the equipment needs to be replaced or kept.
Why It Is Important: Early identification of performance problems guarantees that the tooling keeps running effectively, reducing downtime, and helps avoid production delays.
Conclusion
Selecting the proper press brake tooling is essential to getting correct, superior outcomes. You may improve your manufacturing process by being aware of the many types of tooling, considering essential elements like machine compatibility and material type, and adhering to best practices for maintenance. Consult a dependable provider for knowledgeable guidance if you're unclear which tooling solutions are ideal for your requirements.