Press Brake
KRRASS, a prominent name in the field of sheet metal machinery manufacturing, stands as a frontrunner in the press brake industry in China. Our extensive range of press brakes includes an array of cutting-edge models such as NC press brakes, CNC press brake, hydraulic press brakes, hybrid press brakes, and electric press brakes, each offering unique advantages and capabilities.
Our commitment to excellence extends beyond product offerings. We are dedicated to providing our clients with innovative solutions that enhance productivity, promote efficiency, and deliver customized answers to meet their specific needs. Discover how our CNC Press Brake technology can transform your manufacturing operations, streamline your workflows, and drive your success to new heights.
Inquire Now
Exquisite Craftsmanship in Every Press Brake
As a leading press brake manufacturer, KRRASS® is proud to supply a diverse range of high-quality press brake machines to customers worldwide. Harness the strength and precision of our advanced bending machines, a testament to KRRASS®’s relentless pursuit of perfection. Our extensive cooperation with renowned global brands and the innovative ideas from our headquarters' R&D center ensure that our bending machines represent the pinnacle of sheet metal processing technology.
Our commitment extends beyond manufacturing. We have invested in a state-of-the-art intelligent CNC machine factory in Nanjing to ensure that each piece of equipment upholds our brand’s reputation for excellence.
Join Our Global Family
Be part of the KRRASS® legacy. With branches in more than ten countries, our global footprint is a testament to our trustworthiness and reliability. Contact us today to discover how our expertise can revolutionize your operations.
Press Brake List
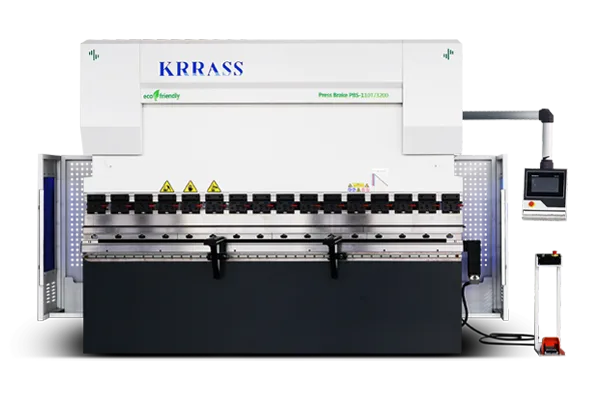
3-4 Axis Back Gauge Press Brake
MB8 Series Advanced Sheet Metal Press Brake (DA-53T Controller)
MB8 Series bending machines are designed with high technology to increase efficiency on precise part bending. With an easy-to-use control unit, stable body structure, perfect design, low operating cost, different tool usage options, and maximum safety standards, KRRASS bending machines are the best in their segment.
Bending performance is increased by using a high-quality European clamping system, ensuring ease of use. KRRASS is your solution partner with various tool options.
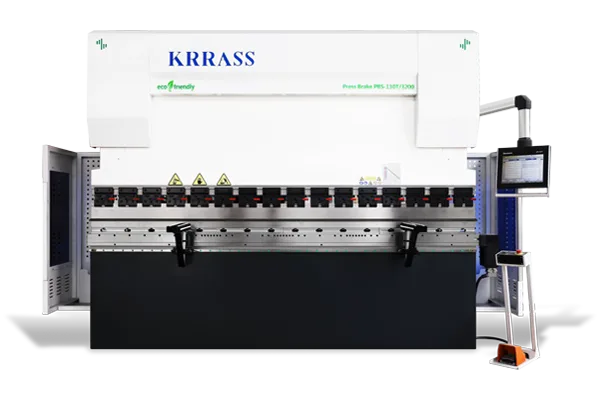
3-4 Axis Back Gauge Press Brake
MB8 Series Advanced CNC Press Brake Machine (DA-58Tx Controller)
MB8 Series bending machines continue to lead with high technology designed to enhance efficiency in precise part bending. The easy-to-use control unit, stable body structure, perfect design, and low operating costs make these machines outstanding. They offer different tool usage options and uphold maximum safety standards.
Bending performance is enhanced by the high-quality European clamping system, providing user-friendly operations. KRRASS serves as your reliable partner with diverse tool options.

6-8 Axis Back Gauge Press Brake
MB8 Series High Standard CNC Press Brake (DA-66T, DA-69T )
These advanced machines are crafted with high technology to maximize efficiency in precise part bending. With user-friendly control units, robust body structures, impeccable design, and cost-effective operation, they stand out in their category.
Enhanced bending performance through top-notch European clamping systems ensures ease of use. KRRASS is a trusted partner with a variety of tool options.
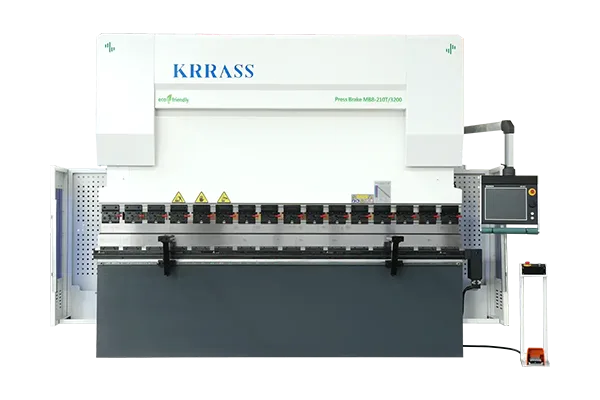
High Performances At All Level
PBS Series Main Motor Servo CNC Press Brake
Hybrid or inverter-driven bending machines offer numerous benefits: lower consumption, reduced oil and pump stress, decreased noise, and greater speed and flexibility.
KRRASS sheet metal bending machines enable you to bend better, faster, and with less energy consumption.
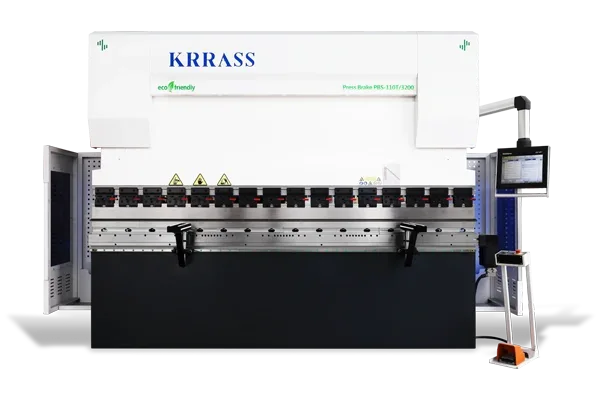
Green Hybrid Technology
PBE Series Hybrid CNC Press Brake
KRRASS® specializes in hybrid technology, allowing for energy savings between 55% and 78% compared to conventional bending machines.
Our hybrid press brake minimizes hydraulic oil and energy consumption without compromising bending performance.
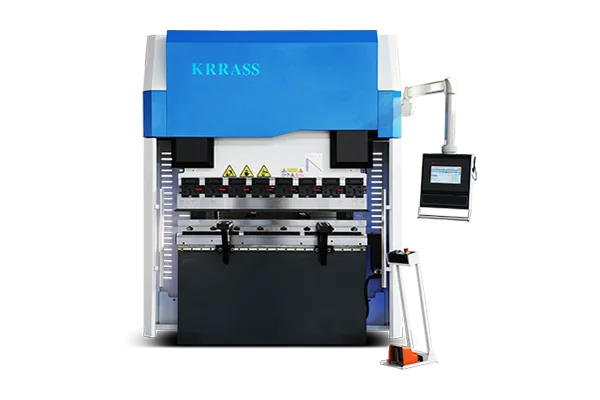
Green Hybrid Technology
ePP Electric Servo Press Brake
KRRASS® excels in hybrid technology development, offering energy savings between 55% and 78% compared to traditional machines.
Our hybrid press brakes reduce the need for hydraulic oil and energy consumption while maintaining excellent bending performance.
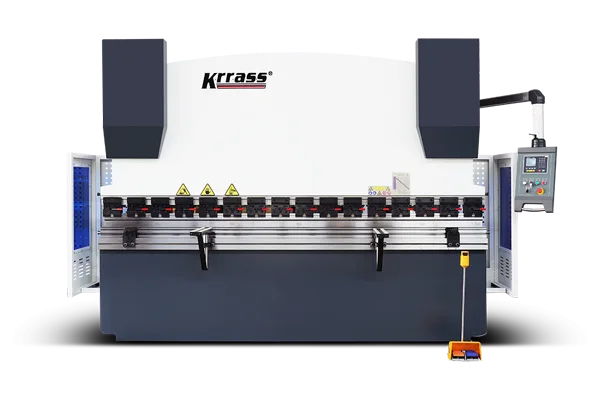
Simple NC Press Brake Machine For Sheet Bending
WC67K Series NC Press Brake (E21 Control)
The NC Press Brake Series is perfectly equipped for sensitive bending and energy-efficient solutions. With user-friendly control units, a rigid body frame, outstanding design, high efficiency, and multiple tool usage solutions, these machines uphold top-level CE safety standards and offer a competitive price range.
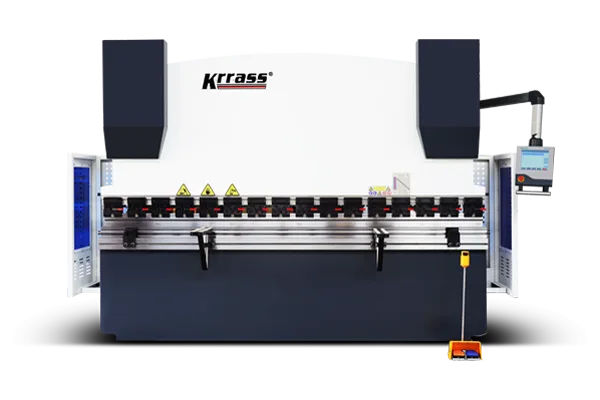
2-Axis Servo Bending Machine
WC67K Series NC Press Brake (E310P Control)
The NC Press Brake Series offers sensitive bending and energy-efficient solutions. The machines come with easy-to-use control units, a sturdy body frame, perfect design, and high efficiency. They provide multiple tool usage solutions and adhere to top-level CE safety standards, making them world leaders in their category.
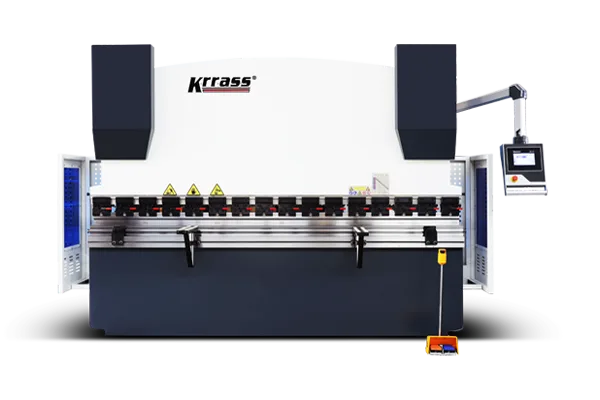
2-Axis Servo Bending Machine
WC67K Series NC Press Brake (DA41T Control)
NC Press Brake Series machines are designed for sensitive bending and energy-efficient solutions. Featuring easy-to-use control units, a robust body frame, impeccable design, high efficiency, and multiple tool usage solutions, they meet top-level CE safety standards and provide excellent value.
In addition to our extensive range of advanced press brake machines, we offer an array of models and configurations, each tailored to meet diverse industrial needs. From hydraulic to servo-electric models, our selection ensures that every operation finds its perfect fit. Whether you're seeking high tonnage capabilities for heavy-duty applications or precision engineering for intricate tasks, our catalog covers it all. Each machine is rigorously tested to deliver unparalleled reliability and performance, helping you achieve optimal results in your metalworking projects. Explore our comprehensive offerings to discover the perfect press brake solution tailored to your specific requirements.
Customer Case
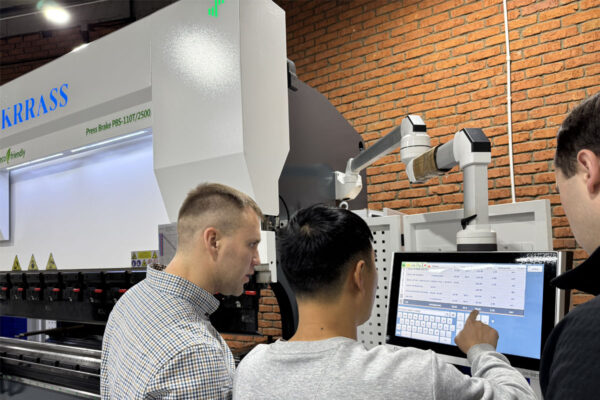
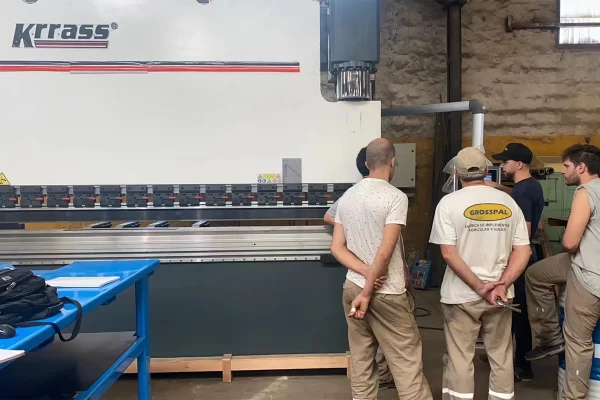
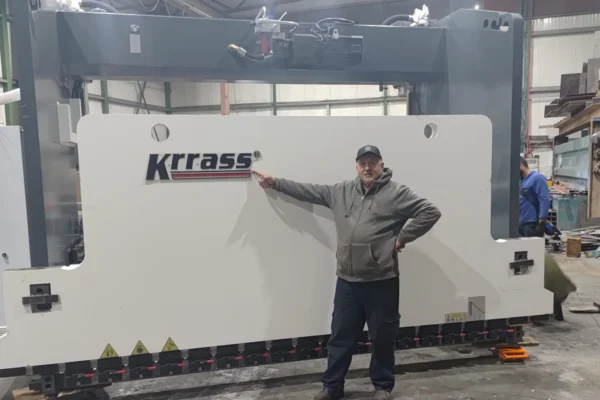
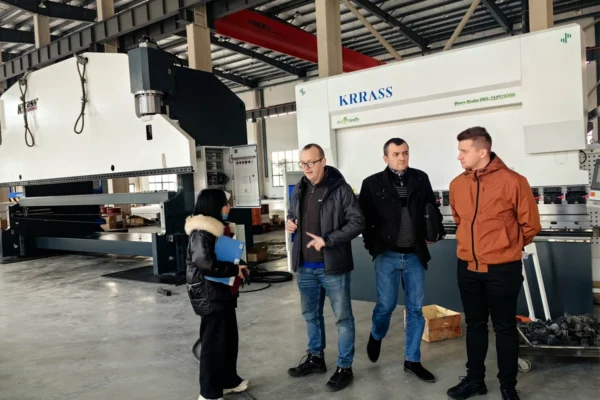
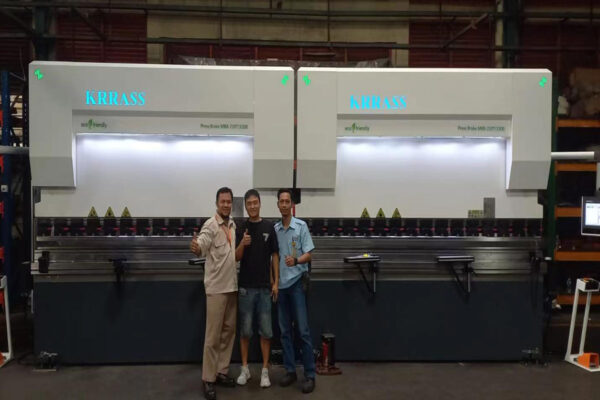
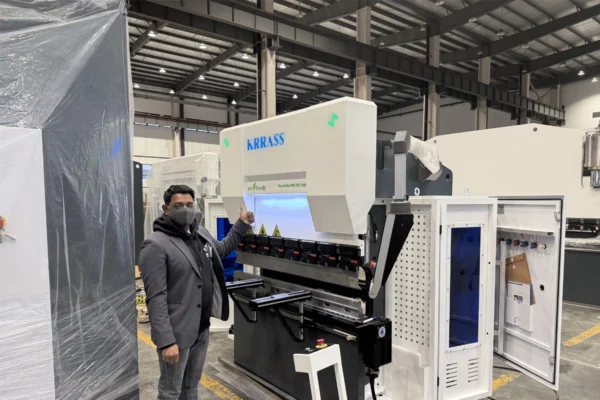
FAQ
What is Press Brake?
Press brake is to use the equipped mold (general or special mold) to bend the cold metal sheet into various geometric cross-sectional shapes. The press brak can quickly realize the actions of sliding down, jogging, continuous, pressure holding, return stroke and halfway stop, and bend multiple elbows of the same angle or different angles in one feeding.
The press brake generally adopts a special CNC system for the bending machine. The coordinate axis of the bending machine has been changed from a single axis is developed to 12 axes, and the numerical control system can automatically realize the sliding depth control, the left and proper tilt adjustment of the sliding block, the front and back adjustment of the back stopper, the left and right adjustment, the pressure tonnage adjustment and the slider approaching speed adjustment so and on.
What is NC Press Brake?
NC press brakes are two-axis programmable tools that use torsion bars for synchronization. NC, or Numerical Control, refers to the use of a numerical control system to manage the machine's movements. NC press brakes typically employ pre-written numerical programs to control bending operations. These programs contain a series of coordinates and motion instructions to determine the shape and bending angles of the workpiece. Operators must manually input these numerical programs, often using the machine's control panel or an external computer. NC press brakes are generally less expensive than CNC press brakes but require more operator skill. NC press brake controllers can be programmed for complex bending sequences, such as those offered by Delem 41, E21, and Cyblec. They remain an accurate and cost-effective option.
What is CNC Press Brake?
The CNC press brake does not need to take special measures during the return (up) trip. In the fast-forward phase of the descending stroke, on the basis of parallel synchronization, two one-way throttle valves are used to eliminate the deviation caused by factors such as manufacturing quality, leakage, etc., and to ensure the downward movement with a certain synchronization accuracy.
When it enters the work advancement stage but has not touched the workpiece, two correction plunger cylinders installed on the workbench are used for further synchronization correction. Imagine that one side first comes into contact with the correction plunger, and the larger correction force slows down or stops the movement of that side until the other side catches up and contacts the correction post hydraulic and pneumatic plugs at the same time. The correction force can be set by the overflow valve and read by the pressure gauge. Practice has shown that the synchronization effect is very obvious, this is because various asynchrony factors can be ignored compared with the correction force. In order to make full use of the capacity of the machine, the overflow valve 3 should be unloaded after a period of time.
What is hydraulic Press Brake?
The Hydraulic Press Brake includes a bracket, a workbench and a clamping plate. The workbench is placed on the bracket. The workbench is composed of a base and a pressure plate. The base is connected to the clamping plate through a hinge. The base is composed of a seat shell, a coil and a cover plate. The coil It is placed in the depression of the seat shell, and the top of the depression is covered with a cover plate.
When in use, the wire is energized to the coil, and after energization, an attractive force is generated on the pressure plate, so as to realize the clamping of the thin plate between the pressure plate and the base. Due to the use of electromagnetic force clamping, the pressure plate can be made into a variety of workpiece requirements, and it can also process workpieces with side walls. Hydraulic press brakes are the safest and more controllable than a mechanical brake. They generally allow for multiple speed settings. Hydraulic also allows for more precision bends, providing greater control when inching down and getting set for a job.
Hydraulic Press Brake Instructions
Step on the foot switch to start bending. Unlike the shearing machine, the bending machine can be released at any time, and the bending machine will stop when the foot is released, and continue to go down after stepping on it.
First, turn on the power, turn on the key switch on the control panel, and then press the oil pump to start, so that you can hear the sound of the oil pump turning. (The machine does not work at this time)
Stroke adjustment, the use of the bending machine must pay attention to the adjustment of the stroke, and it must be tested before bending. When the upper die of the bending machine goes down to the bottom, there must be a gap of plate thickness. Otherwise it will cause damage to the mold and machine. The stroke adjustment also has electric quick adjustment and manual fine adjustment.
For the selection of the bending notch, generally a notch with a width 8 times the thickness of the plate should be selected. If you bend a 4mm sheet, you need to choose a notch of about 32.
There are generally electric quick adjustments and manual fine adjustments for the adjustment of the back gauge, and the method is the same as that of the shearing machine.
How Does a Hydraulic Press Brake Work?
A hydraulic press brake uses the power of a hydraulic motor to apply force onto the metal, compressing it into the die forming the shape. It is the shape of the die that determines the shape acquired with the metal bending process.
The Bending Device of a Hydraulic Press Brake
The bending device of a hydraulic press brake is a stamping process where the sheet metal is stamped into the mold or dies for casting the metal to the required shape. Sheet metal is fed into the device, which gets aligned onto the die. Then as force is applied, the metal is cast as per the shape of the die.
The Die of a Hydraulic Press Brakes
The die is a crucial part of a hydraulic brake because the shape and strength of the die shape the metal. It is possible to cast almost any shape using the latest devices that come with standard and upgraded options for easy and customized shaping. For accuracy in the shaping process, hydraulic press brakes are also designed to be vibration-free.
Why Use a Hydraulic Press?
Hydraulic press brakes can carry out an automated bending process, and the choice of many manufacturers looking for cost-effective bending processes. The precision of the bending is also exact. Moreover, as hydraulic press brakes are available in user-friendly formats, the operator’s ease of use allows for fast metal bending operations.
What Are the Biggest Differences Between CNC Bending Machine and NC Bending Machine?
- Different Structural Principles
The design principles of the two models are different, resulting in varied structures for ensuring synchronization on both sides of the bending slider. The NC press brake uses a torsion shaft to link the left and right swing rods, forming a mechanical synchronization method. The parallelism of the slider isn't automatically checked or adjusted. Conversely, the CNC bending machine uses a magnetic (optical) scale on the slider and wall plate. The CNC system analyzes synchronization through feedback from the scale, adjusting via the proportional electro-hydraulic servo valve for precise synchronization. This setup forms a feedback closed-loop control system. - Accuracy
The parallelism of the slider determines the angle of the workpiece. NC press brakes lack real-time error feedback, so the machine cannot adjust automatically. They also have poor partial load capacity due to the torsion shaft synchronization mechanism. The CNC bending machine, however, uses a proportional electro-hydraulic valve group for slider synchronization and provides real-time error feedback. The system adjusts through the proportional valve after feedback from the magnetic (optical) scale to maintain slider synchronization. - Speed and Operation
The speed of the machine involves slider speed, backgauge speed, and bending steps. NC machines have slower cylinder ratios (6:1 or 8:1), while CNC models are faster (13:1 or 15:1). NC machines rely on experienced operators for trial bending, lacking a control system and V-axis compensation, which can lead to waste and higher operator costs. CNC models, with a professional numerical control system and V-axis compensation, offer simple operation, low experience requirements, and a simulation bending function, eliminating the need for stakeout. - Strength and Load Capacity
NC press brakes cannot handle unbalanced loads without risk of torsion shaft deformation. CNC models don't face this issue; their Y1 and Y2 axes run independently, allowing for eccentric folding. - Comparison of Various Models
When selecting a bending machine, comparing specifications is essential. Consider factors such as tonnage, bed length, stroke, and additional features like tooling options. For example, a 12-ton press with a 20-inch bed length may suit different needs than a 50-ton model with a 6-foot bed length. Understanding the condition and location of machines, influences decision-making. Pricing and request options for quotes or further information can also guide choices, ensuring the machine fits both technical and budgetary requirements.
KRRASS Tailored-made Press Brake
KRRASS® Each sheet metal press brake machine is designed to meet your production needs. Whether you are looking for a NC Press Brake or a CNC Press Brake, we can fulfill your every requirement.
Adds-on, tandem or tridem press brakes, automatic tool changers, and automated robotic bending machine cells are only some solutions we offer to help you achieve your goals.
Reviewed by 182 users
Інноваційні технології KRRASS
KRRASS є справді інноваційним у дизайні своїх гальмових пресів. Зручний інтерфейс у поєднанні з розширеними функціями автоматизації спрощує наш робочий процес і підвищує загальну продуктивність. Приємно бачити бренд, який постійно використовує передові технології у своїх пристроях.
KRRASS egiriji maşynlaryň ýokary çykdajyly öndürijiligi
KRRASS egirme maşynlarynyň baha öndürijiligi bilen deňeşdirip bolmaýar. Ösen aýratynlyklary göz öňünde tutup, hilini we ygtybarlylygyny göz öňünde tutup, maýa goýumlary dogry. Bu tygşytly çözgüt, öndürijilige zyýan bermeýär, önümçilik zerurlyklarymyz üçin ajaýyp uzak möhletli maýa goýumyna öwrülýär.
Kecekapan dan kelajuan mesin lentur yang memuaskan
Kecekapan mesin lentur KRRASS adalah luar biasa. Ia bukan sahaja boleh mengendalikan tugas lentur yang kompleks dengan mudah, tetapi kelajuannya juga mengagumkan. Peningkatan kecekapan membolehkan kami memenuhi tarikh akhir pengeluaran yang ketat dan memenuhi pesanan pelanggan tepat pada masanya.
Išskirtinis stabdžių presavimo tikslumas ir tikslumas
KRRASS lenkimo staklių tikslumas yra išskirtinis. Jis visada atlieka tikslius lenkimus su minimaliais nuokrypiais. Šis tikslumo lygis žymiai sumažina perdirbimą, taupo laiką ir medžiagų sąnaudas. Tai įrodo, kad kiekviena mašina yra kruopščiai suprojektuota.
Excelente marca e equipe de serviço
Estou muito impressionado com a marca KRRASS e sua excelente equipe de atendimento. Desde a consulta inicial até o suporte pós-compra, sua equipe demonstrou profissionalismo e capacidade de resposta. Seu compromisso com a satisfação do cliente realmente os diferencia no setor.