In today's diverse and advanced manufacturing landscape, laser cutting technology has become essential across various industries due to its unique advantages and wide-ranging applications. Whether it's for producing complex structures in the aerospace industry, creating intricate designs in advertising and decoration, precision parts in automotive manufacturing, or even micro components in electronics, laser cutting machines deliver exceptional accuracy, high speed, and flexible design capabilities. A common question that arises in the context of laser cutting is: can a laser cutter cut metal? The answer is a resounding yes. This ability is one of the primary reasons why laser cutters have become indispensable in many industries.
Laser cutting technology can handle a wide variety of metals, such as stainless steel, carbon steel, aluminum, and copper. Thanks to its non-contact process, it minimizes mechanical stress on the workpiece while maintaining high cutting precision, which enhances both product quality and longevity. Additionally, laser cutting stands out in metal processing for its rapid speed, minimal heat-affected zones, and smooth, clean edges, making it an increasingly vital tool in metal fabrication. In the following sections, we will explore how laser cutters efficiently handle different types of metal, the benefits they offer, and the future trends shaping this technology in the world of metal manufacturing.
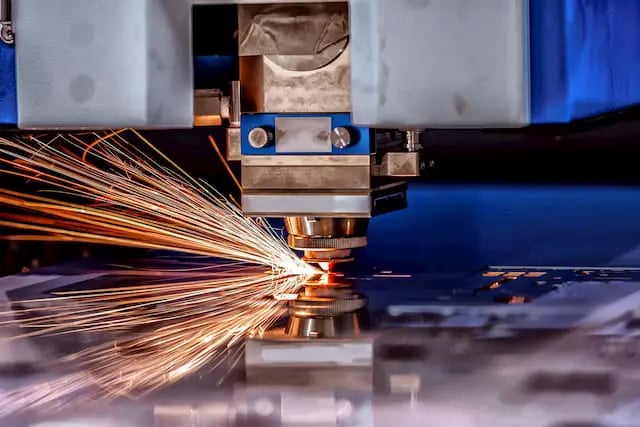
Introduction to Laser Cutting Technology
Definition and Brief History of Laser Cutting
Laser cutting is a precision technique that employs a high-energy laser beam to irradiate material, causing the target area to melt, vaporize, or ignite, resulting in a clean cut. This process offers unmatched accuracy and is widely recognized for its efficiency in various applications.
The origins of laser cutting can be traced back to the late 1960s, where it was primarily used in scientific research. As laser technology advanced and became more affordable, its use spread into industrial production. Today, laser cutting is extensively utilized across industries such as sheet metal fabrication, automotive manufacturing, aerospace, and precision engineering.
Types of Lasers Used for Metal Cutting
There are three main types of lasers commonly used in metal cutting:
- CO₂ Lasers: The most prevalent laser cutting technology on the market, CO₂ lasers use a gas mixture to generate either continuous or pulsed laser beams. Known for their high power, exceptional beam quality, and fast cutting speeds, CO₂ lasers are suitable for cutting a wide range of metals and non-metals.
- Fiber Lasers: Fiber lasers have rapidly gained popularity due to their compact design, high efficiency, and low maintenance. Utilizing fiber doped with rare earth elements as the gain medium, these lasers produce shorter wavelengths, making them ideal for cutting metals, especially highly reflective materials like stainless steel, carbon steel, and aluminum.
- YAG Solid-State Lasers: Known for their stability and durability, YAG solid lasers use a crystal as the laser medium, producing near-infrared wavelengths. While their power output is lower than CO₂ and fiber lasers, they are highly effective for cutting thin sheet metals and are preferred in high-precision and delicate applications.
Work Mechanics
To fully grasp laser cutting technology, it's essential to first understand its fundamental working principle. The heart of any laser cutting machine is the laser generator, which produces a concentrated monochromatic beam, known as the laser.
This laser beam has an extremely high power density and can be focused by an optical system into a tiny spot, with a diameter ranging from tens to hundreds of microns. This leads to a highly concentrated energy per unit area.
When the intense laser beam strikes a metal surface, two primary physical effects occur: absorption and reflection.
For lasers of specific wavelengths, metal materials will absorb part of the laser's energy, which is then quickly converted into thermal energy. This rapid energy conversion causes the temperature of the targeted metal area to rise sharply, reaching its melting or even boiling point within a short time.
Simultaneously, the unabsorbed portion of the laser energy is reflected or scattered.
Once the metal material reaches a molten or vaporized state, the laser cutting head moves at a pre-determined speed, guiding the laser beam along a designated path. This allows for precise cutting of the metal.
Due to the highly concentrated laser beam and rapid energy transfer, most of the heat generated is confined to a small area. This minimizes heat impact on the surrounding material, ensuring high precision and quality along the cutting edge.
When cutting thicker metal sheets, high-pressure gas (such as oxygen or nitrogen) is often used to assist the process.
These gases serve two functions: they blow away slag produced during cutting to maintain a clean cut and, in the case of oxygen, act as an accelerant, enhancing the oxidation reaction of the metal. This further improves cutting speed and efficiency.
Laser Cutters and Metals: Types, Considerations, and Thickness Limitations
Types of Metals Suitable for Laser Cutting
Laser cutting technology is capable of cutting a wide range of metal materials, including carbon steel, silicon steel, stainless steel, aluminum alloys, and titanium alloys. Each metal has different requirements when it comes to laser cutting. For instance, a CO₂ laser cutting machine can cut carbon steel up to 20 mm thick, stainless steel up to 10 mm, and aluminum alloys up to 8 mm. This highlights the importance of selecting the right laser cutting machine to ensure optimal results.
Factors Affecting Metal Cutting with Lasers
- Metal Thickness: The thickness of the metal sheet significantly influences cutting efficiency and quality. Thinner materials are easier to cut quickly, while thicker sheets require higher laser power and slower cutting speeds to maintain cut precision.
- Laser Power Requirements: Different metals and thicknesses require varying laser power levels. Higher power allows faster melting and assists with removing molten material through auxiliary gases. The right laser power not only improves efficiency but also directly impacts cutting costs and the final quality of the workpiece.
The Role of Laser Types in Metal Cutting
- CO₂ Lasers: CO₂ lasers are ideal for cutting a mix of non-metals and metals within a limited thickness range due to their long wavelength. They work well for cutting medium and thick plates of carbon steel and stainless steel.
- Fiber Lasers: As fiber laser technology has advanced, it has become increasingly optimized for metal cutting. Its shorter wavelength is better absorbed by metals, resulting in higher electro-optical conversion efficiency, lower operating costs, and more stable cutting performance, particularly for stainless steel, carbon steel, and aluminum alloys. With their compact design and low maintenance, fiber lasers have become the preferred choice for modern metal cutting applications.
Selecting the appropriate laser cutting machine requires consideration of metal type, thickness, production needs, and the economic benefits of each technology. It’s essential to balance current production requirements with long-term technological advancements.
Thickness Limitations: How Thick Can Laser Cutters Go?
- CO₂ Laser Cutting Machines:
For mild steel, industrial CO₂ lasers can handle plates ranging from 0.5 mm to 25 mm, with high-power machines capable of cutting up to 30 mm. When cutting stainless steel and aluminum, the thickness capability decreases due to differing laser energy absorption rates, typically ranging from 0.5 mm to 20 mm. - Fiber Laser Cutting Machines:
Fiber lasers excel at cutting thinner metal sheets, such as stainless steel, carbon steel, and aluminum alloys, with thicknesses from 0.5 mm to 40 mm. Some high-power fiber laser machines can cut metal sheets up to 80 mm or even 100 mm thick. However, the actual cutting thickness depends on several factors, including cutting speed, precision requirements, and cost considerations. For very thick materials, multi-pass or hybrid processes may be necessary.
In summary, when choosing a laser cutting machine, it’s crucial to consider metal types and thickness while evaluating production needs, cost-efficiency, and future technological trends.
Advantages of Using Laser Cutters for Metals
- High Precision and Accuracy
Laser cutters offer unparalleled precision, making them ideal for cutting complex shapes and intricate designs in metal. The focused laser beam allows for exact cuts, with tolerances often within microns, ensuring consistently high-quality results across various metal types. - Minimal Material Waste
Laser cutting is a non-contact process, meaning the laser beam does not physically touch the metal. This reduces the risk of material distortion or damage and minimizes waste. The precise nature of laser cutting also allows for more efficient use of raw materials. - Speed and Efficiency
Compared to traditional cutting methods, laser cutting is significantly faster, especially for thin metal sheets. The high energy density of the laser enables quick cuts with minimal time loss, increasing productivity in industrial settings. - Versatility
Laser cutters can handle a wide range of metals, including stainless steel, carbon steel, aluminum, copper, and titanium. This versatility makes laser cutting a valuable tool across industries such as automotive, aerospace, electronics, and construction. - Smooth Cutting Edges
The concentrated heat of the laser results in clean, smooth edges, reducing the need for post-processing work like deburring or polishing. This improves the efficiency of production lines and reduces costs associated with additional finishing steps. - Automation Capabilities
Modern laser cutting machines can be integrated with CNC systems for full automation, enabling precise control of the cutting process. This reduces human error, improves repeatability, and allows for large-scale production with minimal supervision. - Reduced Heat-Affected Zone (HAZ)
Due to the highly concentrated laser beam, the heat-affected zone around the cut is small, which helps maintain the structural integrity of the surrounding material. This is particularly important when working with heat-sensitive metals. - Lower Maintenance and Operating Costs
Fiber lasers, in particular, have a longer lifespan and require less maintenance compared to traditional cutting tools. Their higher energy efficiency also reduces operating costs, making them a cost-effective solution in the long run.
What to Consider When Cutting Metal with Lasers
Key Material Property Considerations for Laser Cutting
- Reflectivity Different metals have varying abilities to absorb laser energy. High-reflectivity metals like aluminum and copper pose challenges in laser cutting because they reflect a significant portion of the laser energy rather than absorbing it. This reflection can reduce the efficiency of the cutting process, as less energy is converted into heat, which is essential for melting or vaporizing the material. To address this issue, laser systems with higher power outputs or specialized optical setups are often employed. Additionally, the use of assist gases can help enhance the absorption rate, improving the cutting performance for these reflective materials.
- Thermal Conductivity The rate at which heat is conducted through the material also plays a critical role in laser cutting efficiency. Metals with high thermal conductivity, such as aluminum, tend to dissipate heat quickly, which can reduce the localized energy concentration at the cutting point. This often requires adjustments to laser parameters, such as increasing the power or slowing down the cutting speed, to ensure that enough heat is retained at the laser focus for effective cutting.Conversely, metals with lower thermal conductivity, such as stainless steel, retain heat more effectively in the cutting zone, making it easier to achieve efficient and high-quality cuts with less power or adjustment.
The Impact of Laser Power and Cutting Speed
- Laser Power The power of the laser directly influences the speed, depth, and quality of the cut. Higher laser power enables faster melting of the material and allows for smoother cuts, especially in thicker metals. However, excessive power can lead to over-melting or deformation of the material, resulting in suboptimal cuts. For this reason, selecting the appropriate laser power based on the type of material and its thickness is crucial to achieving the desired results.
- Cutting Speed Cutting speed is closely related to the laser power and plays an essential role in determining the overall quality of the cut. Optimizing the cutting speed can minimize heat input and reduce the size of the heat-affected zone (HAZ), leading to cleaner edges and better precision. However, if the cutting speed is too high, the laser may not fully penetrate the material, leading to incomplete or uneven cuts. A balance between power and speed must be established to ensure both productivity and cutting quality.
Understanding and adjusting for material properties such as reflectivity and thermal conductivity are critical to optimizing laser cutting performance. The interplay between laser power and cutting speed is also essential for achieving high-quality cuts while maintaining productivity. By carefully considering these factors, manufacturers can ensure efficient and precise laser cutting processes.
What Is the Best Laser for Cutting Metal
Both Fiber and Co2 lasers are regularly used for cutting metal, but like most choices, each one of these laser systems has its drawbacks and benefits.
A Fiber laser can cut a large variety of materials with brass and copper having some exceptions, as many Co2 lasers cannot process certain grades of these. But these lasers are much more expensive.
That being said, Co2 lasers use more energy than a Fiber laser, and often cost more to maintain. A Fiber laser is definitely the better choice for most materials, if the budget can allow.
Both are tailored for flat rolled products; with other shapes (angles, beams, tubes), a 6-axis laser cutter is required.
What Is the Maximum Thickness a Laser Can Cut?
It seems simple enough to ask for a single maximum limit on thickness for all laser cutters, but it’s more complicated than that. Many variables are at play in how a laser cuts through a piece of metal, so the maximum laser cutting thickness depends on the specific laser and material being used, among other things.
For the sake of naming a specific number, we can pair a high wattage laser — 6,000 watts — with a metal like stainless steel. In this case, the laser cutting maximum thickness would typically be about 2.75 inches.
But that thickness is contingent on those particular variables. The same laser paired with carbon steel could probably only handle up to 1 5/8 inches, while a 4,000-watt laser could only penetrate 1 inch of stainless steel.
The maximum thickness would go up immensely for non-metallic materials like wood and plastic, as they’re much less dense and strong than steel or aluminum.
Maximum Metal Thickness for Laser Cutting: Key Considerations
Laser cutting is a revolutionary technology that enables manufacturers and metalworkers to cut through various materials with exceptional precision. Utilizing a narrow, high-intensity heat stream, laser cutting has enhanced the design and production of machine parts. However, like all technologies, laser cutting has its limitations, particularly when it comes to cutting thick metals. These limitations are influenced by several factors, including the type of material being cut and the power of the laser.
What Metals Can Be Cut with Lasers?
Laser cutting is commonly used for a wide range of metals, including:
- Carbon Steel: Known for its high carbon content, carbon steel offers excellent strength and durability.
- Mild Steel: With a lower carbon content than carbon steel, mild steel is easier to cut and still provides reliable strength.
- Stainless Steel: Incorporating chromium, stainless steel is resistant to corrosion but can be harder to cut due to its strength.
- Other Steel Alloys: Varying combinations of elements can make steel alloys stronger and more durable.
- Aluminum: Lightweight and ductile, aluminum is easier to cut compared to steel.
While lasers can also cut non-metallic materials like wood and plastic, they are most often employed to work with metals, especially those listed above.
What is the Maximum Metal Thickness a Laser Can Cut?
Determining the maximum thickness a laser can cut is complex and depends on multiple factors, such as laser power, material type, and other variables. For instance, a 6,000-watt laser can typically cut stainless steel up to 2.75 inches thick. However, with the same laser, carbon steel can only be cut up to 1 5/8 inches thick, while a 4,000-watt laser might only handle 1 inch of stainless steel.
These figures can vary significantly based on the material being cut. For example, non-metallic materials like wood or plastic allow for much thicker cuts, as they are less dense and strong than metals like steel and aluminum.
Laser Cutting Power and Material Strength
To better understand the limits of laser cutting, it’s essential to consider both the laser's power and the material's strength:
- Laser Power: Higher-wattage lasers, such as 6,000-watt models, can cut through thicker or stronger metals. However, in many cases, lower-wattage lasers (3,500 or 4,000 watts) are sufficient for the task.
- Material Strength: Metals vary in strength based on their composition, affecting their cuttability. Carbon steel, with its high carbon content, is tougher and more difficult to cut than mild steel, which is softer but still strong. Stainless steel, with its added chromium, is also challenging to cut due to its resistance to rust and strength. Aluminum, being lighter and more ductile, is generally easier to cut with lasers.
Cutting Speed and Gas Usage
Laser cutting speed is influenced by both the laser's power and the material’s strength. Higher-powered lasers not only cut through thicker materials but can also process thinner ones at faster speeds. However, gas usage during the cutting process plays a role in ensuring smooth cuts and clean edges. For example, nitrogen is typically used with stainless steel, while oxygen is employed for carbon steel. The type of gas and the time required for its application can impact cutting speed and quality.
In summary, selecting the appropriate laser cutter depends on a careful balance of laser power, material type, thickness, and desired cutting speed. For many jobs, a high-power laser may not be necessary, but the choice should be made based on the specific requirements of the task at hand.
Conclusion
If you're searching for a reliable solution to have your metal parts cut with laser-accurate precision, KRRASS is your ideal partner. Our sheet metal fabrication process guarantees top-tier quality and dependability, all performed in-house — with no need for outsourcing. Starting with laser cutting, followed by bending, inserting, welding, grinding, and painting, we deliver the finished products you need with unmatched precision.
At KRRASS, we use advanced equipment to ensure the highest quality metal parts for your projects. Wondering can a laser cutter cut metal? With KRRASS, the answer is a resounding yes. Contact us today to get started!
Reviewed by 1 user
Escolher o laser Krrass é uma consideração para um bom serviço no futuro