Are you in the market for a high-quality panel bender for sale but unsure where to start? Look no further! In this ultimate guide to affordable bending solutions, we’ll walk you through everything you need to know about finding the best panel bender for sale. Whether you’re a seasoned professional or just beginning your journey into the world of metal fabrication, this comprehensive guide will provide you with valuable insights, expert tips, and detailed comparisons to help you make an informed decision. Get ready to discover top deals, essential features, and the latest trends in panel bending technology.

Introduction
Brief Overview
Panel benders are essential machines in the field of metal fabrication, designed to automate the process of bending and shaping metal sheets with precision and efficiency. These machines are crucial for producing consistent and high-quality bends in a variety of materials, including steel, aluminum, and copper. Whether you're manufacturing components for the automotive industry, constructing metal furniture, or creating custom metal parts, a panel bender can significantly enhance your production capabilities. By reducing manual labor and minimizing errors, panel benders not only improve productivity but also ensure a higher standard of workmanship.
Purpose of the Guide
Navigating the market for panel benders can be daunting, given the myriad of options available. This guide is designed to simplify the process for you. Our aim is to provide comprehensive information and practical advice to help you identify and purchase a panel bender that meets your specific needs without breaking the bank. From understanding the various types and benefits of panel benders to comparing top brands and finding the best deals, this guide covers all the essential aspects to equip you with the knowledge needed to make a well-informed decision. Whether you're a seasoned professional or a newcomer to metal fabrication, this guide will be your go-to resource for securing an affordable and high-quality panel bender.
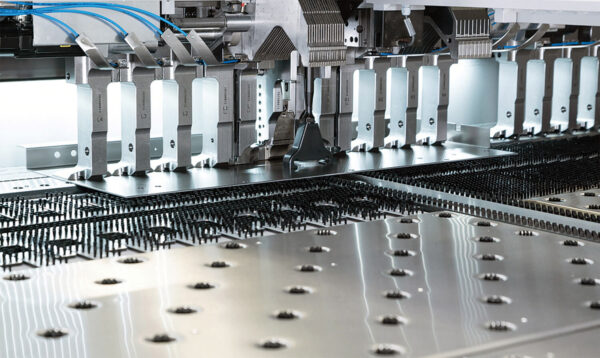
Understanding Panel Benders
A panel bender is a specialized machine used in metal fabrication to bend and shape metal sheets into desired angles and forms. Unlike traditional press brakes, panel benders utilize a combination of automated movements and sophisticated control systems to achieve precise and repeatable bends. The machine typically clamps the metal sheet in place while a bending blade moves up and down or side to side, applying force to create the bend. Panel benders are known for their ability to handle complex bending tasks with high accuracy and consistency, making them ideal for various industrial applications.
Key Components and How They Work
Clamping System
The clamping system is an essential component of a panel bender, designed to secure the metal sheet firmly in place during the bending process. This system usually consists of upper and lower clamps that apply uniform pressure along the sheet’s edges. The stability provided by the clamping system ensures that the metal sheet does not shift or move, allowing for precise and consistent bends.
Modern clamping systems may be hydraulically or pneumatically operated, offering adjustable clamping force to accommodate different material thicknesses and types. Advanced models might also feature quick-release mechanisms for faster sheet changes, enhancing overall productivity.
Bending Blade
The bending blade is the primary tool within a panel bender that applies force to bend the metal sheet. It operates by moving in a controlled manner, either up and down or side to side, depending on the design of the machine. The blade’s movement is precisely calibrated to create the desired angle and shape of the bend.
High-quality panel benders use hardened steel blades to ensure durability and maintain sharpness over prolonged use. Some machines are equipped with interchangeable blades or multi-axis bending capabilities, allowing for a wide range of bending operations, from simple right angles to complex curves and folds.
Backgauge System
The backgauge system is responsible for positioning the metal sheet accurately before the bending process begins. It consists of a series of adjustable stops and guides that can be moved to specific locations according to the bending program. The backgauge ensures that the bends are made at the correct locations on the sheet, which is crucial for producing parts with precise dimensions.
In automated panel benders, the backgauge system is often integrated with the machine’s control system, allowing for automatic adjustments based on the programmed bend sequence. This integration minimizes setup time and reduces the risk of human error, leading to higher efficiency and repeatability.
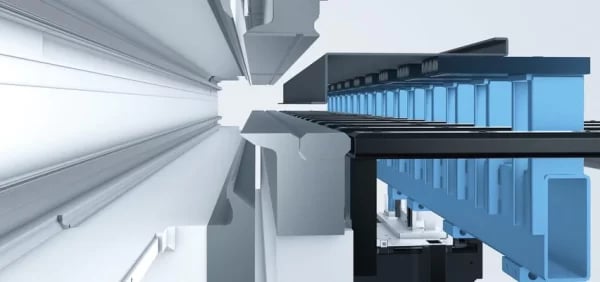
Control System
The control system is the brain of the panel bender, typically consisting of a computer and specialized software that manage the machine’s operations. Operators use the control system to input specifications such as bend angles, material type, and thickness. The system then calculates the optimal bending sequence and adjusts the machine’s components accordingly.
Advanced control systems offer user-friendly interfaces, often with touchscreen displays, and may include features like programmable logic controllers (PLCs) and CNC (Computer Numerical Control) capabilities. These systems can store multiple bending programs, allowing for quick setup changes and consistent production of repeat orders. Additionally, some control systems offer remote monitoring and diagnostics, enabling operators to troubleshoot and maintain the machine more efficiently.
Safety Mechanisms
Safety is a critical aspect of any industrial machinery, and panel benders are no exception. Modern panel benders are equipped with various safety mechanisms to protect operators from potential hazards during operation. These include physical barriers, such as safety gates and guards, that prevent access to the bending area while the machine is in operation. Sensors and light curtains are often used to detect the presence of hands or objects in dangerous zones, automatically stopping the machine to prevent injuries. Emergency stop buttons are strategically placed for quick access, allowing operators to halt the machine immediately in case of an emergency.
Additionally, advanced panel benders may include safety interlocks that ensure the machine cannot operate unless all safety conditions are met. Regular maintenance and safety checks are essential to ensure that these mechanisms function correctly and provide continuous protection.
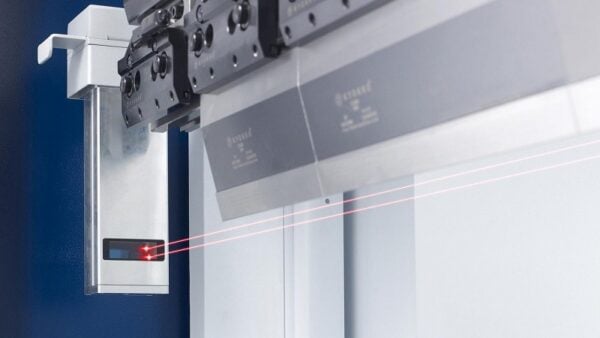
Types of Panel Bender For Sale On the Market
1. Manual Panel Bender
The manual panel bender is the simplest type, relying on manual force for bending. It is ideal for smaller jobs, offering ease of use and minimal maintenance requirements.
2. Hydraulic Panel Bender
Utilizing hydraulic pressure, this type is designed for bending thick metal sheets. Operated via a foot pedal controlling the hydraulic cylinder, it is suitable for heavy-duty bending tasks.
3. Electric Panel Bender
Electric panel benders are suited for bending small to medium-sized metal sheets. They operate using an electric motor to power the hydraulic cylinder, providing efficiency and moderate capacity.
4. CNC Panel Bender
The CNC panel bender, controlled by computer numerical programming, offers precision and accuracy in bending metal sheets. It excels in high-volume production scenarios due to its automated capabilities.
Other Panel Bending Machines
Aside from the main types, other machines include:
- Roll Benders: Used for creating curves and circles in metal sheets.
- Press Brakes: Ideal for creating angular bends in metal sheets.
- Box and Pan Brakes: Suitable for forming corners and bends in metal boxes or pans.
How to Judge If You Need a Panel Bender
Deciding whether you need a panel bender involves evaluating your specific needs, production requirements, and the advantages a panel bender can offer. Here are key factors to consider, along with detailed explanations to help you make an informed decision:
1. Production Volume and Efficiency
High Production Volume: If your operation involves high production volumes with repetitive bending tasks, a panel bender can significantly enhance efficiency and throughput. The automation and precision offered by panel benders reduce cycle times and increase overall productivity. For example, a fully automatic panel bender can process several parts per minute, far outpacing manual bending operations.
Manual vs. Automated Production: Compare the time and labor involved in manual bending processes with the potential speed and efficiency gains from using a panel bender. Automated panel benders can perform complex bends quickly and accurately, freeing up operators for other tasks. If your current process requires a lot of manual adjustments and handling, switching to a panel bender can streamline your workflow and reduce labor costs.
2. Complexity of Bending Tasks
Complex Bending Requirements: If your products require complex bends, tight tolerances, or intricate shapes that are difficult to achieve manually, a panel bender can provide the precision and consistency needed. For instance, producing parts with multiple angles and radii can be efficiently handled by a panel bender without the need for extensive manual setup.
Variety of Bends: Consider the range of bends you need. Panel benders are versatile and capable of performing multiple bends on a single piece without repositioning, which is beneficial for complex and varied bending operations. This versatility can be especially valuable in industries such as automotive, aerospace, and custom metal fabrication where varied bending tasks are common.
3. Quality and Consistency
High-Quality Standards: If your products must meet stringent quality standards and require high precision, a panel bender ensures consistent and accurate results. Automated control systems minimize human error and produce uniform bends, which is crucial for maintaining quality in high-volume production.
Reduced Rework and Scrap: Evaluate your current rates of rework and material waste. A panel bender’s precision can reduce errors and scrap, leading to cost savings and higher product quality. For example, the repeatability of a panel bender can minimize the occurrence of defective parts, ensuring that each piece meets the required specifications.
4. Material and Thickness Variety
Diverse Material Handling: If you work with a wide variety of materials and thicknesses, a panel bender’s adjustable settings and versatile capabilities can accommodate different material properties and ensure optimal bending performance. This adaptability is crucial for operations that handle everything from thin aluminum sheets to thick steel plates.
Specific Material Needs: Some materials may require specific bending techniques or pressures that are difficult to achieve manually. Panel benders can be programmed to handle these specific requirements, ensuring consistent results across different materials. For instance, bending high-strength steels or delicate materials can be precisely controlled with a panel bender.
5. Cost Considerations
Initial Investment vs. Long-Term Savings: Assess the initial cost of acquiring a panel bender against the long-term savings from increased efficiency, reduced labor costs, and lower material waste. While the upfront cost may be significant, the return on investment (ROI) can be substantial over time. Calculate the potential savings in labor, material, and increased production capacity to justify the investment.
Maintenance and Operation Costs: Consider the ongoing maintenance and operation costs of a panel bender. Modern machines are designed for durability and ease of maintenance, potentially lowering long-term operational expenses. Additionally, automated diagnostics and maintenance alerts can help prevent costly downtime.
6. Space and Integration
Available Space: Ensure you have sufficient space to accommodate a panel bender in your facility. Consider the machine’s footprint and any additional space required for material handling and operator access. If space is limited, look for compact or modular designs that can fit into your existing layout.
Integration with Existing Processes: Evaluate how a panel bender will integrate with your current production processes. Consider any necessary changes to workflow, training for operators, and compatibility with existing equipment. A smooth integration can enhance overall efficiency and minimize disruption during the transition.
7. Future Growth and Scalability
Planned Expansion: If you anticipate growth in your production volume or complexity, investing in a panel bender now can prepare your business for future demands. Scalable solutions allow you to expand capabilities as your needs evolve. For example, modular panel benders can be upgraded with additional features or capacity as your production requirements increase.
Competitive Advantage: Having a panel bender can give you a competitive edge by enabling faster production, higher quality, and the ability to take on more complex projects. In a competitive market, the ability to deliver high-quality products quickly can set you apart from competitors.
Understanding Cost of Panel Bender for Sale
1. Price Range Based on Quality and Features
Panel benders vary widely in cost, primarily influenced by their quality, specifications, and brand. While basic models can start as low as $1,500, more advanced options with specific features range from $25,000 to over $100,000. The price increases with capabilities such as CNC control, multi-axis bending, and higher bending force.
2. Functionality and Material Handling
The functionality of panel benders is tailored to handle different thicknesses and widths of materials. Smaller machines are suitable for thinner sheets, while larger, specialized models can handle thicker and wider sheets. Prices correspondingly adjust based on the machine's capacity to handle varying material dimensions.
3. Additional Considerations
Total Cost of Ownership: Beyond the initial purchase, factor in costs like warranties, installation, and training. Cheaper machines may lead to higher long-term expenses if maintenance or part replacements become frequent.
After-Sales Support: Evaluate the manufacturer’s reputation for after-sales service. Quality support can significantly impact the machine's reliability and longevity in your operations.
4. Making an Informed Decision
Before purchasing, conduct thorough research to align the machine’s capabilities with your business needs and budget. Seek insights from industry professionals and manufacturers to understand specific requirements and ensure the chosen panel bender meets operational demands effectively.
Top Manufactures' Panel Bender for Sale
Lorem ipsum dolor sit amet, consectetur adipiscing elit. Ut elit tellus, luctus nec ullamcorper mattis, pulvinar dapibus leo.
Salvagnini
- Founded: 1963
- Company Description: Salvagnini, originating from Italy, revolutionized sheet metal processing with its automated solutions. The company is known for integrating advanced technology into its machinery, optimizing efficiency and precision.
- Popular Model: Salvagnini P4
- Advantages: The Salvagnini P4 is celebrated for its adaptive bending technology, which allows for rapid changeovers and high flexibility in production. It excels in handling complex parts with minimal setup time, making it ideal for diverse manufacturing environments.
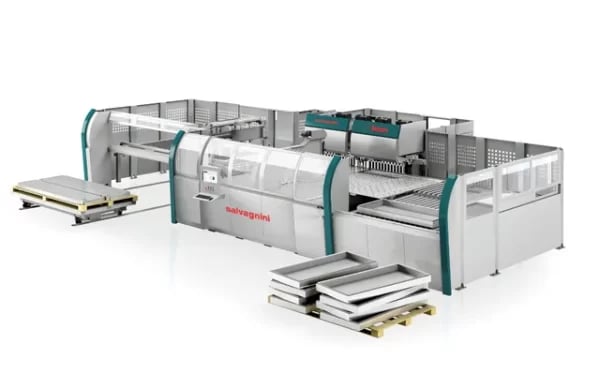
TRUMPF
- Founded: 1923
- Company Description: TRUMPF, a global leader based in Germany, specializes in machine tools, laser technology, and electronics for industrial applications. The company emphasizes innovation and sustainability in its manufacturing solutions.
- Popular Model: TRUMPF TruBend Series (e.g., TruBend 7036)
- Advantages: TRUMPF TruBend series offers exceptional bending precision and speed, supported by advanced control systems. They are renowned for their ergonomic design and intuitive user interface, enhancing operator efficiency and reducing setup times.
Amada
- Founded: 1946
- Company Description: Amada, a Japanese manufacturer, leads the industry in precision sheet metal processing equipment. With a focus on reliability and technological advancement, Amada’s solutions cater to a wide range of industrial needs.
- Popular Model: Amada HFE Series (e.g., HFE M2)
- Advantages: The Amada HFE series is known for its high-speed and high-precision bending capabilities. Equipped with state-of-the-art servo-electric technology, these machines offer energy efficiency and reduced environmental impact while maintaining superior accuracy in bending operations.
Bystronic
- Founded: 1964
- Company Description: Bystronic, headquartered in Switzerland, is dedicated to providing cutting-edge solutions for sheet metal processing. The company focuses on delivering productivity, flexibility, and sustainability through its innovative technologies.
- Popular Model: Bystronic Xpert series (e.g., Xpert 40)
- Advantages: Bystronic Xpert series excels in combining high bending speeds with precise bending angles. These machines feature automatic tool changing systems and adaptive bending sequences, optimizing production efficiency and minimizing setup times.
LVD
- Founded: 1952
- Company Description: LVD, originally from Belgium, is a leading manufacturer of sheet metalworking machinery. The company’s commitment to quality and customer satisfaction is reflected in its comprehensive range of innovative solutions.
- Popular Model: LVD PPEB Series (e.g., PPEB 4)
- Advantages: LVD PPEB series offers robust construction and versatility, capable of handling a wide range of bending applications. They are known for their reliable performance and ease of operation, making them a preferred choice for various industrial sectors.
Durma
- Founded: 1956
- Company Description: Durma, based in Turkey, is renowned for its extensive portfolio of industrial machinery, including cutting-edge solutions for sheet metal processing. The company emphasizes durability, performance, and innovation.
- Popular Model: Durma AD-R Series (e.g., AD-R 37220)
- Advantages: The Durma AD-R series stands out for its heavy-duty construction and advanced control systems. These machines offer high bending accuracy and efficiency, suitable for demanding production environments requiring consistent performance and durability.
Haco
- Founded: 1965
- Company Description: Haco, headquartered in Belgium, specializes in manufacturing machinery for sheet metalworking and steel fabricating industries. The company is known for its commitment to quality craftsmanship and customer satisfaction.
- Popular Model: Haco Euromaster S Series (e.g., Euromaster S 30150)
- Advantages: Haco Euromaster S series provides precise bending solutions with versatile tooling options. These machines are designed for maximum productivity and operational flexibility, catering to a wide range of sheet metal bending requirements.
Paner Bender for Sale from Krrass Machinery
As a premier manufacturer based in China, KRRASS consistently delivers top-quality panel bender machines to global manufacturers. A panel bender machine plays a crucial role in manufacturing and fabrication by bending and shaping sheet metal and flat materials into diverse configurations. These machines find widespread application across industries including HVAC (Heating, Ventilation, and Air Conditioning), automotive, aerospace, and general metalworking. KRRASS is recognized for its commitment to innovation and reliability, providing advanced solutions that meet the demanding needs of modern industrial production.
We equip the machine with a suction cup design that enables sheet metal fabrication with a maximum bending size of 2000mm x 2000mm. Its remarkable bending speed of only 0.2 seconds per bend significantly enhances productivity and helps reduce labor expenses.
KRRASS Servo electrical fully-automatic panel bender machine
The CNC automatic panel bender machine, designed for processing thin plates, features a structured setup including a tool holder, worktable, clamping feeding device, and CNC operating table. The worktable consists of a base integrated with a clamping piece feeding structure.
Key Features:
- Rotary Part Manipulator: Independently secures and rotates blanks to precise positions as needed.
- Dual-axis Manipulator: Positions sheet metal and allows for negative bends, enhancing versatility.
- ACB Laser for Precision: Ensures accurate angles and flawless parts right from the initial production stage.
- TecZone Fold Programming: Offers the industry's quickest offline programming, simplifying setup and operations.
- Integrated Tool Change (ToolMaster Bend): Automates setup of upper blank holder tools for efficient operations.
- Advanced Gripper Systems: Assists in secure component handling throughout the production process.
- Automatic Loading and Unloading: Enhances productivity with simultaneous loading and unloading during production.
- On-Demand Servo Drive: Operates swiftly, silently, and with energy efficiency, contributing to sustainable manufacturing practices.
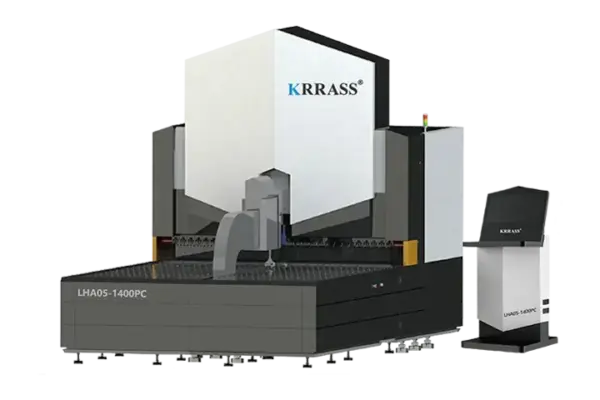