In modern manufacturing, the adoption of servo electric press brakes represents a pivotal advancement in precision engineering and operational efficiency. These sophisticated machines have revolutionized the sheet metal bending process, offering manufacturers unparalleled control, speed, and flexibility. Understanding the advantages of servo electric press brakes not only highlights their impact on production capabilities but also underscores their role in driving innovation across various industries.
Introduction to Servo Electric Press Brakes
Servo electric press brakes represent a significant leap forward in the field of manufacturing technology, particularly in the realm of sheet metal bending and forming processes. Unlike their traditional hydraulic counterparts, which rely on hydraulic fluid and mechanical linkages for operation, servo electric press brakes utilize electric motors controlled by advanced servo systems to achieve precision bending.
Definition and Basic Functionality
At its core, a servo electric press brake operates through the precise synchronization of servo motors and ball screws. These components work together to accurately position the ram (or beam) of the press brake, allowing for controlled bending of sheet metal. The elimination of hydraulic systems in favor of electric servo technology brings several advantages, including enhanced speed, accuracy, and flexibility in bending operation
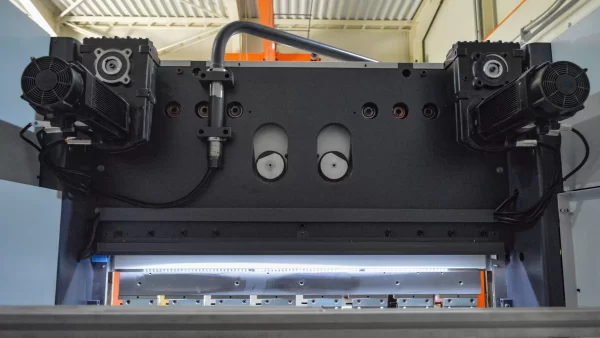
Evolution from Traditional Hydraulic Press Brakes
The evolution from hydraulic press brakes to servo electric press brakes marks a significant shift in manufacturing capabilities. Traditional hydraulic press brakes rely on hydraulic cylinders to apply force, which can lead to variations in bending angles due to factors such as oil viscosity and mechanical wear over time. In contrast, servo electric press brakes offer precise control over the ram position and bending force, resulting in consistent bend angles and repeatability.
This evolution has been driven by advancements in electric motor technology, control systems, and feedback mechanisms, which allow servo electric press brakes to achieve higher levels of accuracy and productivity compared to their hydraulic predecessors. Moreover, the electric-driven operation of servo press brakes contributes to reduced energy consumption and quieter operation, making them more environmentally friendly and cost-effective solutions for modern manufacturing facilities.
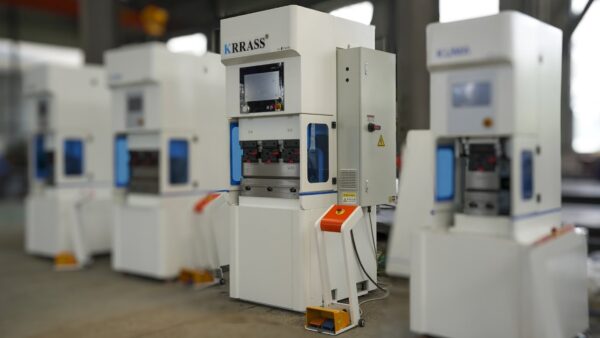
How Servo Electric Empower Your Bending Process
The bending process is indispensable in manufacturing and processing, fulfilling both geometric requirements of products and enhancing material structure to improve strength and rigidity, particularly beneficial for applications under heavy loads and stresses. Moreover, bending plays a pivotal role in part connection and assembly, augmenting product stability and durability. Economically, it offers efficiency in shape completion, thereby reducing production costs due to its swift processing capabilities.
Servo electric press brakes significantly contribute to the bending process by offering unparalleled precision and control. These machines utilize servo motors for precise motion and positioning, ensuring accurate bending angles and shapes. Compared to traditional hydraulic press brakes, servo electric models deliver faster cycle times and energy efficiency, translating into cost savings and enhanced productivity.
When selecting the right press brake, considerations such as precision requirements, production volume, material types, and operational efficiency are crucial. Servo electric press brakes excel in scenarios demanding high precision and versatility across various materials. Their advanced CNC control systems enable precise adjustments, making them ideal for industries requiring exacting standards like aerospace, electronics, and automotive manufacturing. Understanding these factors ensures optimal machine selection, aligning with specific production needs and market demands.
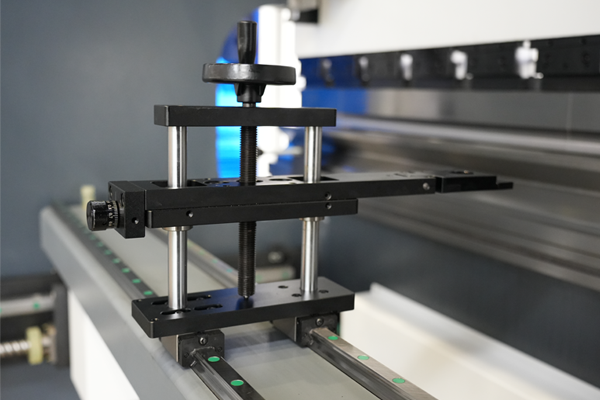
What are the Types of Servo Press Brakes?
Servo press brakes come in two primary types: electric-hybrid servo press brakes and full servo-electric press brakes. Let's delve into each type and highlight some major applications for both.
Electric-Hybrid Servo Press Brakes
A hybrid servo press brake integrates both hydraulic and electric servo systems to function. The hydraulic system provides the power needed for handling heavier loads, while the electric servo system ensures precise control and faster operation for lighter loads. These press brakes are:
- Ideal for manufacturing and fabricating heavy-duty metal components.
- Suitable for a wide array of applications, including automotive, aerospace, construction, and more.
- Used for bending, forming, and shaping sheet metal into various angles and configurations.
- Apt for medium- to high-volume production runs.
- Capable of handling thicker and heavier materials than fully servo-electric machines.
Full Servo-Electric Press Brakes
These machines operate solely on servo motors, completely eliminating the need for a hydraulic system. They offer high precision and superior energy efficiency, making them a popular choice in contemporary manufacturing settings. Full servo-electric press brakes are ideal for:
- High-precision applications and high-volume production.
- A broad range of applications, including electronics, medical devices, and precision components.
- Bending, forming, and shaping sheet metal into various angles and forms.
- Achieving superior accuracy and precision, making them suitable for complex geometries and intricate designs.
- Working with thinner materials with high precision and minimal distortion.
Both electric-hybrid and full servo-electric press brakes come equipped with advanced features that make them excellent investments for businesses looking to enhance their manufacturing processes. Depending on specific needs and applications, either type can be a suitable option for enterprises in the manufacturing and fabrication industry.
How Does a Servo Electric Press Brake Work?
Understanding the operational mechanics of a servo-electric press brake is crucial for maximizing its efficiency and longevity. Unlike traditional hydraulic models, which rely on hydraulic fluid for power, a servo-electric press brake utilizes electric motors to drive its movements with precision and control.
Components and Operation of Traditional Press Brake
Normal press brake machines typically consist of two primary components: the die and the punch. These components work together to bend sheet metal into desired shapes. Depending on the machine's design, either the punch or the die may be movable while the other remains fixed. This movable part applies force against the fixed part, shaping the metal placed between them.
Servo-Electric Mechanism
In a servo-electric press brake, such as Krrass's Electro Servo Press Brake, hydraulic pressure is replaced by electric power. Two servo motors power the movable parts, providing the force needed to press the die against the fixed punch. This electric-driven system offers several advantages over hydraulic systems, including faster response times, precise control over bending force, and reduced energy consumption.
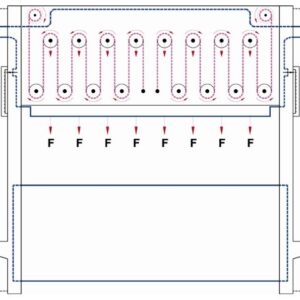
Precision and CNC Integration
Modern servo-electric press brakes often feature integrated CNC systems, like the CNC Press Brake EURO MB8 4 ~ 6-Axis from Krrass. These systems enable operators to input precise bending specifications digitally. The CNC system translates these specifications into commands that adjust the positioning and force applied by the servo motors. This automation ensures consistent and accurate bends without the need for manual adjustments, significantly improving productivity and quality control.
Conclusion
In summary, the operation of a servo-electric press brake involves the precise coordination of electric servo motors and CNC systems to manipulate metal sheets accurately and efficiently. By harnessing electric power and advanced automation, these machines offer manufacturers enhanced capabilities in bending operations while optimizing energy use and operational workflow.
Key Features of Servo Electric Press Brakes
Servo-electric press brakes are renowned for their advanced capabilities, offering several key features that enhance precision, versatility, and control in metal forming processes.
Dynamic Synchronization
Dynamic synchronization is one of the standout features of servo-electric press brakes. This refers to the precise coordination of the machine's components during the bending process. Servo motors and advanced control systems ensure that both sides of the ram move in perfect harmony, maintaining alignment throughout the entire operation. This synchronization allows for the accurate forming of complex shapes and profiles, contributing to the high precision and repeatability of the bending results.
Versatility in Complex Bending Jobs
Servo-electric press brakes are exceptionally versatile, making them ideal for handling complex bending tasks. These machines can work with a wide variety of materials, including different metal types and thicknesses, enabling manufacturers to meet diverse production requirements. Their adaptability extends to performing intricate bends, making them suitable for demanding applications in industries such as aerospace, electronics, and automotive manufacturing.
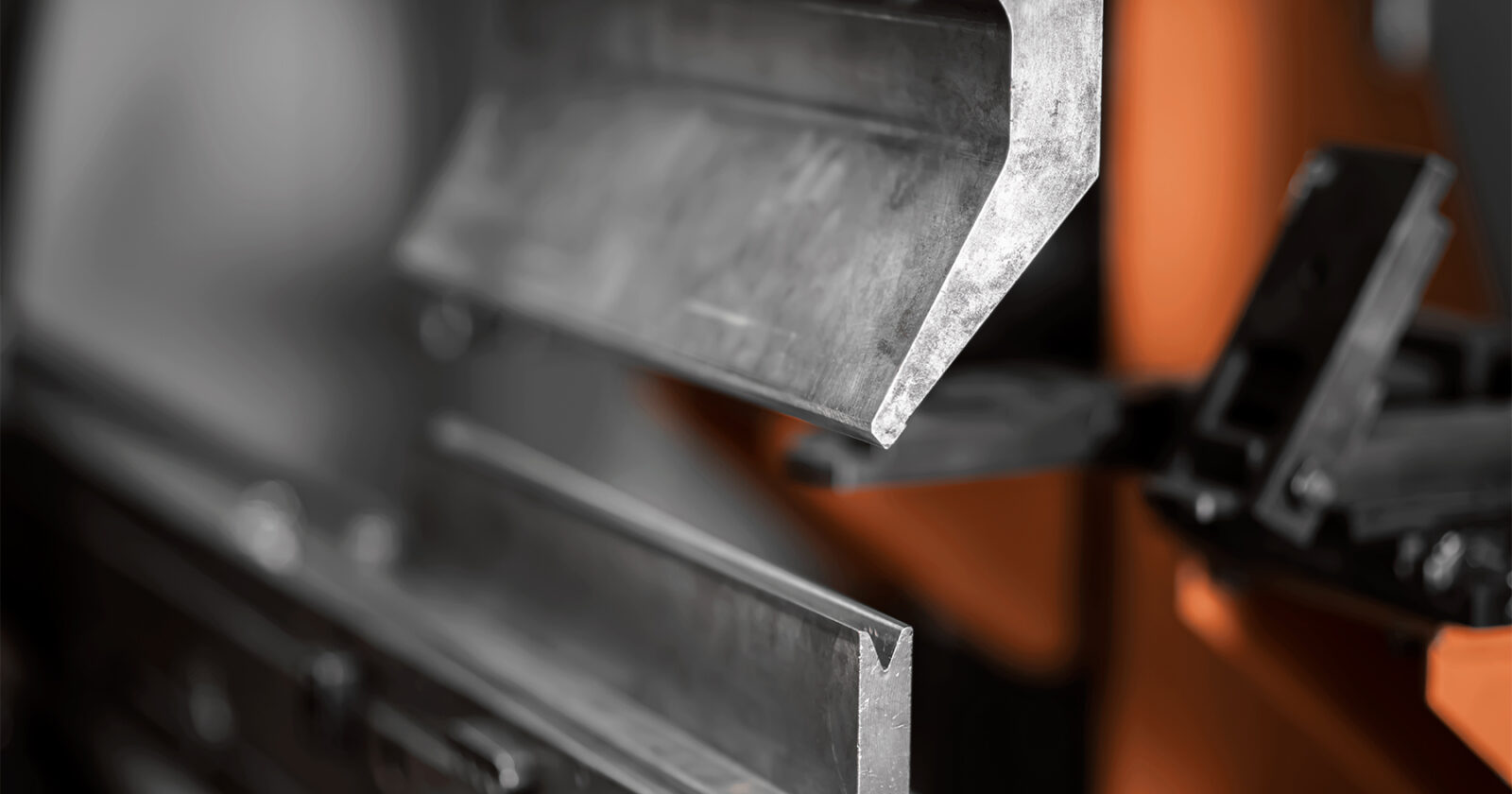
Real-Time Monitoring and Control
Advanced control systems in servo-electric press brakes facilitate real-time monitoring and control. Feedback devices, such as encoders or magnetic scales, continuously monitor the position and movement of the ram. This real-time feedback allows the control system to make instantaneous adjustments, ensuring the bending process adheres to the programmed parameters. The result is enhanced precision, consistency, and the ability to quickly adapt to changes in material or bending requirements.
Advantages of Servo Electric Press Brakes
If you are opting to invest in it, you should know why doing so will help your business. Here we recommend Krrass PBS series electric press brake, because:
Unmatched Precision in Bending
Servo-electric press brakes offer unparalleled precision in the bending process. The use of servo motors allows for extremely accurate control over the ram movement, resulting in precise angles and dimensions in the formed parts. The ability to program and control bending parameters with high accuracy ensures consistency across multiple production runs, leading to high-quality finished products. Micro-adjustments and fine-tuning capabilities enable operators to achieve tight tolerances, meeting the demanding requirements of industries such as aerospace, electronics, and automotive.
Energy Efficiency and Sustainability
Servo-electric press brakes are known for their energy efficiency, contributing significantly to sustainability initiatives in manufacturing. Unlike hydraulic press brakes that continuously run hydraulic pumps, servo-electric systems only consume power during active operation. This on-demand energy usage reduces overall energy consumption and lowers operating costs. Additionally, the absence of hydraulic fluids in the system eliminates the need for hydraulic oil, reducing environmental impact and the potential for oil leaks or spills in the production environment.
Adaptability to Various Materials
Servo-electric press brakes are versatile and can handle a wide range of materials, including different types of metals and alloys. This flexibility makes them suitable for diverse industries and applications, from forming thin sheets in electronics to bending thicker metal plates in heavy-duty manufacturing. Precise control over the ram allows for efficient bending of materials with varying thicknesses, ensuring uniformity in finished products regardless of the material being processed.
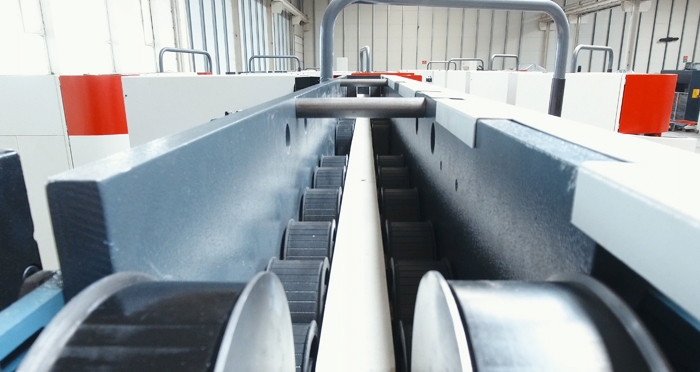
Applications of Servo Electric Press Brake
Servo-electric press brakes are indispensable in various industries that require precise bending of sheet metal and other materials. Their exceptional precision, versatility, and efficiency make them ideal for numerous applications:
Sheet Metal Fabrication
Servo-electric press brakes are widely utilized in producing sheet metal components for sectors such as automotive, aerospace, electronics, and appliances. Their high precision enables the accurate bending of complex shapes and parts, ensuring consistency and quality in the final products.
Electronics Manufacturing
In the electronics industry, where precision and small-scale production are vital, servo-electric press brakes are used to bend and form metal components for electronic devices and equipment. The ability to produce intricate bends with high accuracy is crucial for the functionality and reliability of electronic components.
Automotive Industry
Servo-electric press brakes play a crucial role in manufacturing automotive parts such as brackets, panels, and chassis components. Achieving consistent and precise bends is essential to ensure the quality, safety, and performance of these parts.
Appliance Manufacturing
Household appliances often require precisely bent components such as cabinets, panels, and brackets. The accuracy and adaptability of servo-electric press brakes make them perfect for producing these parts, ensuring they fit and function correctly within the appliance.
Aerospace Industry
In aerospace manufacturing, strict tolerances and high-quality standards are imperative. Servo-electric press brakes are employed to produce components like brackets, panels, and structural parts with precision, meeting the rigorous demands of the aerospace industry.
Job Shops and Prototyping
The flexibility of servo-electric press brakes makes them ideal for job shops and prototype production. Quick setup times and the ability to efficiently handle various bending tasks make them suitable for small-scale or custom manufacturing projects.
Medical Equipment
The medical industry demands precision-formed components for various devices and equipment. Servo-electric press brakes fulfill the stringent quality and dimensional requirements of the medical sector, ensuring the reliability and safety of medical products.
Energy Sector
Components used in the energy sector, such as brackets and enclosures for renewable energy systems or power generation equipment, benefit from the precision and consistency of servo-electric press brakes. These machines ensure that components meet the necessary specifications for optimal performance and durability.
What Are The Differences Between Servo Electric and Hydraulic Press Brake
Hydraulic and servo-electric press brakes both serve the fundamental purpose of bending metal materials into specific shapes required for various metal fabrication operations. However, they accomplish this through distinct mechanisms and technologies.
Hydraulic Press Brakes
Hydraulic press brakes rely on oil and hydraulic cylinders to produce the necessary force to bend materials. The hydraulic system provides powerful and consistent pressure, making these machines suitable for handling heavy-duty materials and high-volume production runs. The hydraulic fluid, controlled by valves and cylinders, generates the force required to move the ram and shape the metal.
Servo-Electric Press Brakes
In contrast, servo-electric press brakes use electricity to power servo motors, which generate the movement needed to bend the material. This electric-driven system allows for precise control over the ram's movement, resulting in high accuracy and repeatability. Servo-electric press brakes are known for their energy efficiency and reduced maintenance needs, as they do not require hydraulic fluid.
Both hydraulic and servo-electric press brakes can be equipped with CNC (Computer Numerical Control) controllers. CNC controllers enable operators to input specifications for bends via a computer, streamlining the process and improving accuracy. This feature allows for easier and faster control, enhancing productivity and reducing the likelihood of errors.
Key Differences
The primary differences between hydraulic and servo-electric press brakes lie in their working principles. Hydraulic press brakes use oil and hydraulic pressure, providing robust force for bending thicker and tougher materials. On the other hand, servo-electric press brakes rely on electric servo motors, offering precise control, energy efficiency, and lower maintenance. Hybrid models offer a blend of these advantages, catering to a wide range of fabrication needs.
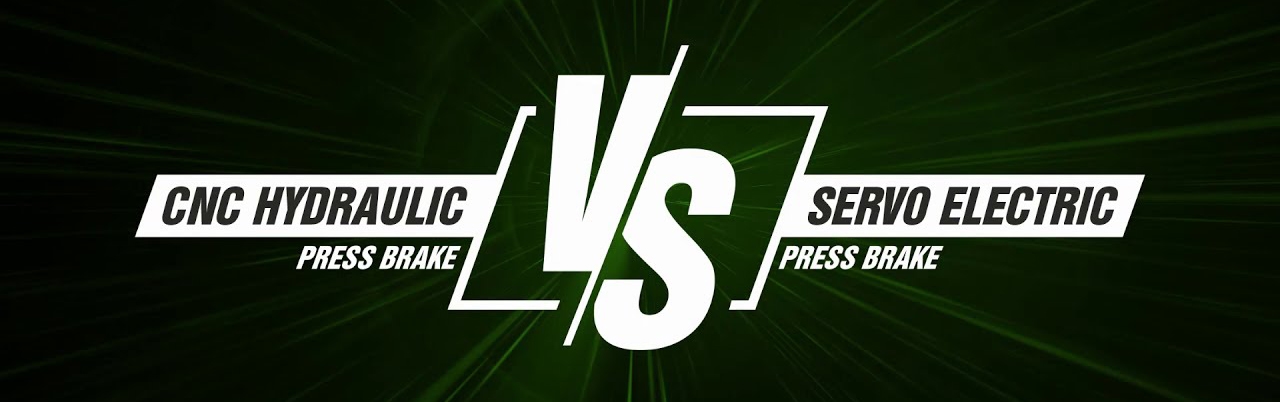
Hydraulic Press vs. Servo-Electric Press: Differences in Speed, Precision, and More
Speed and Efficiency
When considering efficiency, servo-electric press brakes shine not only due to their superior energy efficiency but also their overall operational speed. While hydraulic press machines often boast a faster initial approach speed, their advantage typically ends there.
Servo-electric press brakes, such as the Krrass PBS seovo brake, offer easier operation, even when compared to CNC hydraulic press brakes. They feature faster acceleration and deceleration, along with higher bending speeds, optimizing output and significantly boosting productivity. These advanced machines have high-dynamic mechanical drive systems that result in cycle times up to 55% shorter, translating to increased output and revenue potential for various metal fabrication industries. This speed advantage is coupled with exceptional precision.
Precision and Accuracy
Both types of press brakes deliver high accuracy for single bends. However, the difference becomes more pronounced when considering repeatability. Servo-electric press brakes often achieve accuracy within a single degree or 0.000079 inches, whereas hydraulic presses typically maintain accuracy within 0.0004 inches.
The extreme precision and repeatability of servo-electric press brakes stem from their closed-loop control systems, which ensure consistent results even with complex bend angles and depths. This high level of precision is crucial for industries where exact specifications are critical, such as aerospace and medical device manufacturing.
Maintenance and Longevity
The fundamental differences in the working principles of hydraulic and servo-electric press brakes significantly impact maintenance, repair, and longevity. Maintenance requirements can affect operational efficiency and profitability.
Hydraulic press brakes, with their reliance on oil and intricate systems of pumps, valves, and hoses, require frequent maintenance and cleaning. They are also prone to more frequent breakdowns, leading to higher repair costs and increased downtime.
In contrast, servo-electric press brakes feature fewer moving parts, resulting in lower maintenance needs and a longer machine lifespan. This durability is especially beneficial for high-volume metal fabrication operations. Additionally, manufacturers like Accurl provide ongoing support for their servo-electric press brakes, enhancing their longevity and reliability.
For those seeking the benefits of hydraulic power combined with the quiet operation and precision of servo-electric press brakes, hybrid models like the H-Brake Hybrid Press Brake Euromaster offer an excellent solution. These machines provide rapid ram speeds, consume 65% less energy, generate 70% less noise, and achieve 35% shorter cycle times.
Conclusion
Both hydraulic and servo-electric press brakes offer unique advantages that can significantly impact your metal fabrication operations. While hydraulic press brakes are robust and powerful, ideal for heavy-duty applications, servo-electric press brakes excel in speed, precision, and lower maintenance needs, making them suitable for high-precision and high-volume production. Understanding these differences can help you choose the right press brake to enhance your operational efficiency and meet specific industry requirements.
Why Servo Electric Is Quicker Than Hydraulic Press Brake
Comparison of Principles and Working Methods
Working Principle of Servo-Electric Press Brake
To begin, the metal sheet that needs processing is placed on the workbench of the servo-electric press brake. Typically, clamps or positioning devices secure the workpiece, ensuring stability during the bending process. The operator then programs and sets parameters on the servo-electric press brake through a control panel or computer interface. This involves inputting the desired bend angle, location, and workpiece dimensions.
The main power source for the press brake is the servo motor. Once the parameters are set, the servo motor operates at a precise speed and position according to the programmed instructions. It transmits power to the bending rod (also known as the ejector rod) via transmission devices such as screw rods and ball nuts. As the servo motor moves, the bending rod applies pressure to the workpiece, causing it to bend. The shape and angle of the bending rod are adjusted based on the geometric requirements of the workpiece to achieve the desired bend.
Servo-electric press brakes are often equipped with force sensors or pressure feedback systems that monitor the pressure exerted on the workpiece in real time. This allows the control system to adjust the servo motor's actions based on the set parameters, ensuring precise control over the applied force. Once the preset bending angle or shape is achieved, the servo-electric press brake stops automatically. The workpiece is then released, and the operator can remove it. The bending rod typically returns to its starting position, ready for the next operation.
Additionally, servo-electric press brakes can store multiple bending programs, allowing operators to select the appropriate one for different workpiece requirements, thereby enhancing efficiency and precision.
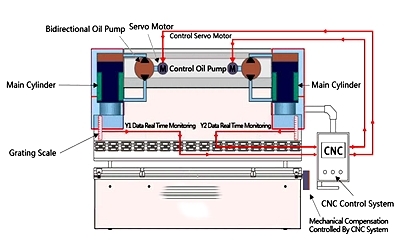
Working Principle of Hydraulic Press Brake
The hydraulic press brake's core is its hydraulic system, which includes hydraulic pumps, cylinders, and oil tanks. Before operation, the hydraulic system must be prepared to ensure adequate hydraulic oil and normal working conditions. The metal sheet to be processed is placed on the hydraulic press brake's table, with fixtures and positioning devices securing the workpiece.
The operator programs the hydraulic press brake through a control panel or computer interface, entering the desired bend angle, location, and workpiece dimensions. Once parameters are set, the hydraulic pump generates a flow of hydraulic oil, transmitting pressure to the hydraulic cylinder. The cylinder then moves, pushing the bending rod (or ejector rod) to apply force on the workpiece.
The applied force bends the workpiece. The shape and angle of the bending rod are adjusted according to the workpiece's geometric requirements to achieve the desired bend. Hydraulic press brakes often have force sensors or pressure feedback systems to monitor real-time pressure on the workpiece. The control system uses this feedback to adjust the hydraulic pump's output, ensuring the applied force reaches the predetermined value.
Once the preset bending angle or shape is achieved, the hydraulic system stops automatically. The workpiece is released, and the operator can remove it. The hydraulic cylinder returns to its starting position, ready for the next operation. Similar to servo-electric press brakes, hydraulic press brakes can store multiple bending programs, allowing operators to select the appropriate one for different workpieces, improving production efficiency and precision.
Power Delivery
The servo electric press brake utilizes a servo motor as its primary power source. Power is transmitted to the bending rod through precision transmission devices such as screws or ball nuts. This direct electric transmission allows for precise control and adjustment of motion speed and position, ensuring accurate and consistent bending operations.
In contrast, a hydraulic press brake operates using a hydraulic system where a hydraulic pump generates hydraulic pressure. This pressure is then transmitted to the bending rod through hydraulic cylinders. While hydraulic systems offer high power output capability, the nature of hydraulic transmission may result in relative instability in motion speed and position, necessitating finer control.
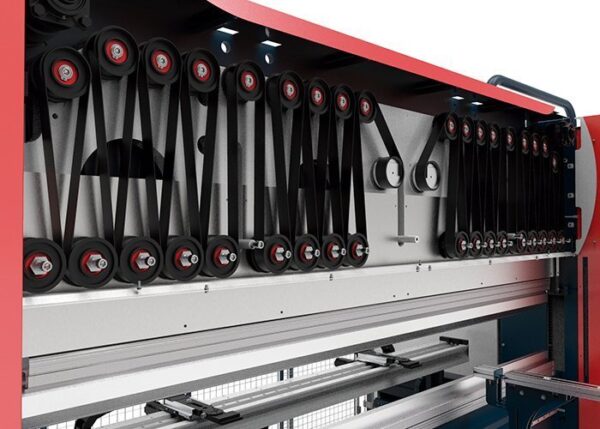
Control System
Servo electric press brakes are typically equipped with advanced CNC (Computer Numerical Control) systems. These CNC systems precisely control the rotation angle, speed, and position of the servo motor. This advanced control capability ensures high-precision and stable bending operations, making servo electric press brakes suitable for applications that demand utmost accuracy.
Control of a hydraulic press brake relies on the pressure and flow control within the hydraulic system. While hydraulic systems can achieve a certain level of accuracy, compared to servo electric systems, their control precision and stability may be slightly less refined. This can impact the consistency of bending operations, especially in applications requiring very tight tolerances.
How To Choose A Ideal Servo Electric Press Brake
- Bending Capacity: Evaluate the maximum thickness and length of materials you intend to bend. Choose a servo electric press brake that can handle your production requirements effectively.
- Accuracy and Precision: Determine the level of precision necessary for your applications. Opt for models equipped with advanced control systems and feedback mechanisms to ensure precise bending results.
- Speed and Productivity: Assess the speed of the press brake relative to your production volume. Higher speed machines can significantly boost productivity, especially in high-volume manufacturing environments.
- Flexibility and Versatility: Select a press brake that offers versatility in terms of tooling options and adjustable features. This ensures the machine can accommodate a wide range of bending tasks and material types.
- Control System: Look for a user-friendly control interface with advanced programming capabilities. A robust control system allows for efficient setup and adjustment of bending parameters, enhancing operational efficiency.
- Energy Efficiency: Prioritize models known for their energy-saving features. Servo electric press brakes are recognized for their efficiency, helping to lower operational costs over time.
- Integration with Automation: If integrating into an automated production line, ensure the press brake is compatible with automation systems and robotics. Seamless integration enhances workflow efficiency and overall productivity.
By reading this article, I hope you now have a comprehensive understanding of this type of brakes, aiding you in selecting the most suitable option. When making your purchase decision, it's crucial to buy from a trusted supplier. Krrass, as a reputable servo press brake manufacturer, offers extensive experience and ensures excellent service to meet your needs satisfactorily.
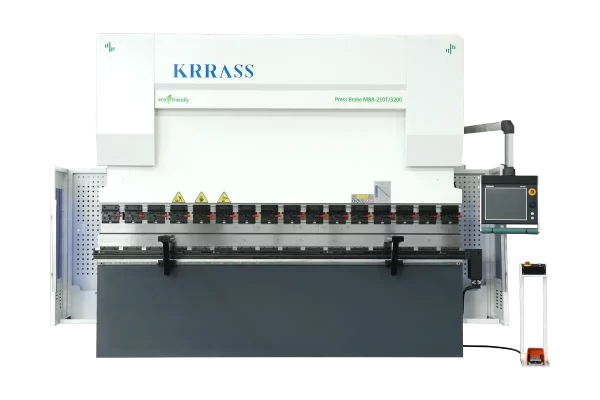
Reviewed by 1 user
Providing such a reliable and efficient machine that has positively impacted our operations, a great electric press brake machine