Shearing, also referred to as die cutting, shearing machinery, is a manufacturing process that cuts materials without generating chips or relying on burning or melting. When the cutting blades are straight, the process is specifically called shearing, whereas if the blades are curved, it is categorized as a shearing-type operation. The most commonly sheared materials include sheet metal and plates, though rods can also be processed. Shearing-type operations encompass techniques such as blanking, piercing, roll slitting, and trimming. This process is applied to a variety of materials, including metal, fabric, paper, and plastics, often using specialized shearing machinery to achieve precise cuts
Shearing Principle
A punch (or moving blade) is used to push a workpiece against the die (or fixed blade), which is fixed. Usually, the clearance between the two is 5 to 40% of the thickness of the material, but dependent on the material. Clearance is defined as the separation between the blades, measured at the point where the cutting action takes place and perpendicular to the direction of blade movement. It affects the finish of the cut (burr) and the machine's power consumption. This causes the material to experience highly localized shear stresses between the punch and die. The material will then fail when the punch has moved 15 to 60% of the thickness of the material because the shear stresses are greater than the shear strength of the material and the remainder of the material is torn.
Two distinct sections can be seen on a sheared workpiece, the first part being plastic deformation and the second being fractured. Because of normal inhomogeneities in materials and inconsistencies in clearance between the punch and die, the shearing action does not occur in a uniform manner. The fracture will begin at the weakest point and progress to the next weakest point until the entire workpiece has been sheared; this is what causes the rough edge. The rough edge can be reduced if the workpiece is clamped from the top with a die cushion. Above a certain pressure, the fracture zone can be completely eliminated. However, the sheared edge of the workpiece will usually experience work-hardening and cracking. If the workpiece has too much clearance, then it may experience roll-over or heavy burring.
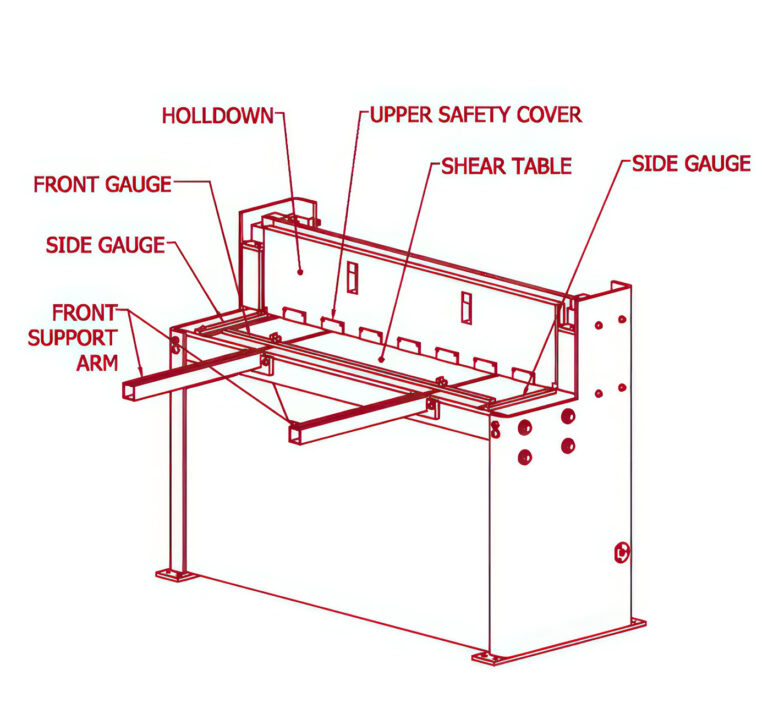
Tool materials
- Low alloy steel is used in low production of materials that range up to 0.64 cm (1⁄4 in) thick.
- High-carbon, high chromium steel is used in high production of materials that also range up to 0.64 cm (1⁄4 in) in thickness.
- Shock-resistant steel is used in materials that are equal to 0.64 cm (1⁄4 in) thick or more.
Tolerances and surface finish
When shearing a sheet, the typical tolerance is +0.1 inch or −0.1 inch, but it is feasible to get the tolerance to within +0.005 inch or −0.005 inch. While shearing a bar and angle, the typical tolerance is +0.06 inch or −0.06 inch, but it is possible to get the tolerance to +0.03 inch or −0.03 inches. Surface finishes typically occur within the 250 to 1000 microinches range but can range from 125 to 2000 microinches. A secondary operation is required if one wants better surfaces than this.
How Define a Shearing Machinery
Before we get to the workings, let us first understand what a Hydraulic Shearing Machinery is and its uses. A Hydraulic Shearing Machine is an industrial tool used for cutting metal bars and sheets that you otherwise would find difficult to cut. It includes a combination of rotating blades and disks that allow for the above-mentioned action.
Since Hydraulic Shearing Machines all have the same mechanism (more or less), they can be of different kinds based on their blades’ shapes — linear or circular. There are various ways of shaping a given material or metal, of which shearing is a method. Other methods include bending, cutting, spinning, and rolling.
The Hydraulic Shearing Machine has various uses and is a prime fabricator tool. Krrass has had consistent clients from a variety of industries that utilize these tools. It is mainly used in the manufacturing industry for producing different products.
Some prime products produced by the Hydraulic Shearing Machine are parts of ships, planes, railways, and so on. It is used in heavy-duty industries such as those mentioned above. It also can be used for other industries such as the cooking, electric, and decorative industries.
What parts and units does the shearing machine consist of?
A shearing machine typically consists of the following parts and units:
- Bed or baseThis provides a stable foundation for the machine. The entire body of the machine is strong, durable and reliable.
- Fixed bladeThis is attached to the bed and remains stationary during the cutting process. It serves as the stationary cutting edge.
- Moving bladeThis is mounted on a sliding mechanism and moves back and forth across the fixed blade to perform the cutting action. It serves as the movable cutting edge.
- Hold-down systemThis clamps the workpiece in place during the cutting process. It helps to keep the workpiece stable and prevent it from moving during the cutting process.
- Guiderail systemThis helps to align the workpiece and keep it in position during the cutting process. It helps to ensure that the workpiece is cut at the correct angle and location.
- Actuating mechanismThis controls the movement of the moving blade. It can be a foot pedal or hand lever that the operator uses to start and stop the cutting process.
- Cutting angle adjustment mechanismThis allows the operator to adjust the angle of the blades relative to each other. It allows the operator to adjust the angle of the blades to suit the specific cutting requirements of the workpiece.
- Safety guards and interlocksThese are designed to protect the operator from the cutting action. They are usually placed around the blades and other moving parts of the machine to prevent accidents.
These are the main parts of the shearing machine, their functions are as described above, depending on the specific design of the machine, additional parts may be present.
Features and Benefits of Automatic Shearing Machinery
- CNC shears before feeding using a mobile rear stopper device and electronic counter, easy to adjust the position of rear stopper.
- The whole welding frame structure is used, and the vibration aging treatment, the machine has good rigidity, high precision and good precision retention.
- The tool rest adopts steel structure. Under the action of oil cylinder, it moves up and down along the roller to realize shearing action.
- The front feeding frame adopts steel structure, which is tempered to eliminate internal stress, strong rigidity and good stability.
- The forward feed adopts imported precision ball screw, linear guide guide, and digital AC servo motor drive.
- The positioning is accurate, the operation is fast and stable, and the front feeding table is arranged with steel balls and brushes.
- The positioning speed of the three-axis CNC motor can be adjusted arbitrarily to improve work efficiency.
- The parameter adjustment function is set in the system, and the reference points of the two axes can be modified arbitrarily. Thereby adjusting the positioning value of the numerical control system.
- The system is equipped with an automatic knife retract function, which can make the feeder retreat in time during the cutting process to avoid friction between the blade and the plate during the cutting process.
- After each startup or shutdown, the two axes controlled by the CNC system can automatically find the reference point when the machine is restarted to ensure repeatable positioning accuracy.
Shearing Machinery Systems
Shearing machinery is similar to the principle of cutting paper with scissors that we use in our daily lives. The metal sheet to be cut is positioned where the blade of the Shearing Machinery will strike it, and then the upper blade descends to cut the sheet.
Shearing machinery can be classified into mechanical and hydraulic types, depending on the blade drive system.
1. Mechanical Type
In the case of the mechanical type, the blade is driven by a motor and clutch, and is characterized by its high cutting speed. Compared to the hydraulic type described below, the mechanical type is inexpensive, and since it does not use oil, maintenance is relatively simple.
2. Hydraulic Type
The hydraulic type uses hydraulic pressure generated in the cylinder to drive the blade powerfully, resulting in high cutting performance. It can cut even relatively thick metal plates, which is difficult with the mechanical type. On the other hand, care must be taken to avoid problems such as oil leakage.
How to Use the Shearing Machine
The following situations may occur during the use of the plate shearing machine:
- Start the shearing machine for idling several cycles, to ensure that under normal conditions, try to shear different thickness of the sheet, from thin to thick. Ensure users are familiar with the shearing machine performance.
- The test shear plate thickness must be adjusted to different blade clearance. If the blade clearance is not adjusted, the durability of the blade will be affected.
- Open the pressure gauge switch and observe the oil pressure value during the shearing process. The pressure should be less than 20MPa when cutting 12mm plate. The pressure of the remote pressure regulating valve No9 is set at 20-22mpa when it leaves the factory. The user must abide by this regulation and shall not increase the pressure for cutting beyond the specified material surface, resulting in machine damage.
- Sound balance during operation. Stop the shearing machine for inspection if there is any noise.
- When the plate shearer operates, the temperature of the fuel tank increases. 60 degrees, over which the power off rest.
Points to Keep In Mind When Using Shearing Machinery
There are several points to keep in mind when using Shearing Machinery to produce high-quality products and to work safely.
Specific Usage
1. Adjusting the Clearance
Clearance in shearing machinery is the distance between the upper and lower blades. Even with scissors that we use in our daily life, paper cannot be cut well with scissors that have a large gap between the two blades.
For the same reason, in shearing machinery, the clearance between the upper and lower blades is important, and the size of the clearance makes a difference in the quality of the cut surface. If the clearance is too narrow, the load on the blade is too great and the blade wears easily, shortening the life of the blade.
Conversely, if the clearance is too large, the cut surface will have sagging and burrs. The appropriate clearance is determined by the material to be cut and the plate thickness, but in general, the appropriate clearance is approximately 6~10% of the plate thickness.
2. Adjustment of Shear Angle
The shear angle is the opening angle between the upper and lower blades, just like the angle between two blades when scissors are opened. When the shear angle is large, or in scissors, when the scissors are wide open at the beginning of a cut, a small amount of force can be used to cut.
However, if the shear angle is too large, the cut material is prone to deflection (bow), twist (twist), and warp (camber).
3. Do Not Cut Materials Over the Maximum Thickness
Shearing machinery has a maximum thickness limit. Cutting material that exceeds the maximum thickness will put a heavy load on the shearing machine, and in the worst case, may result in a breakdown.
When handling a shearing machine, you should check the maximum plate thickness and be careful not to cut any material that is thicker than the machine is capable of cutting.
What is the Difference Between Shearing and Die cutting?
If you are familiar with the metal fabrication process, you may be wondering what is the difference between shearing and die cutting. In fact, they are both cutting or finishing processes that involve using a blade to remove excess material or create the desired shape for sheet metal. The main difference is that shearing uses straight edged blades, whereas the blades used in die cutting are curved.
Advantage
As we mentioned in the opening paragraph, shearing has become a popular and accepted practice in metal fabrication. In fact, this method has many distinct advantages.
First, the metal can be sheared without heating. This process is usually carried out at room temperature or when the metal is cold.
Second, it produces far less waste than other manufacturing practices. This allows manufacturers to save on cleaning costs and perform the process faster.
Finally, shearing can be used on a variety of metals, including stainless steel, bronze, aluminum, copper, and iron, to name a few.
Shortcoming
While shearing has many significant advantages, there are also some potential disadvantages to be aware of.
First, exceptionally hard metals like tungsten cannot be sheared.
Second, shearing can cause the stainless steel plate to deform if not handled carefully.
Advantages of the plate shearing machine before feeding are as follows:
- Matched with the ordinary shearing machine, compared with the rear stopper positioning more, can completely replace manual, mainly used in various sizes of plate cutting, blanking, high efficiency, blanking, can achieve automatic programming, automatic positioning, automatic cutting, automatic feeding, automatic return and other functions.
- Protection function
- Over-limit protection, when the travel to the limit will automatically stop the movement, to avoid collision.
- Self-diagnosis protection function, when the software, system or electrical failure will automatically alarm, remind check and elimination.
- Air pressure protection function, when the air pressure is too low will alarm and stop working, to avoid damage to pneumatic components.
- Voltage protection function, when the voltage fluctuation is too large, will automatically alarm and stop working, avoid damage to the servo system, electrical.
- Components and software program, choose pneumatic automatic clamp, clamping force is large, stable feeding; Easy to operate.
What are the mail applications of shearing machine?
- Metal Fabrication Industry
Shearing machines are commonly used for cutting metal sheets, steel plates, aluminum sheets, etc., for the production of automotive components, machinery parts, steel structures, etc.
- Construction Industry
Used for cutting and processing construction materials such as reinforcing bars, steel plates, etc., for the fabrication of building structures and components.
- Automotive Manufacturing
Shearing machines are used for cutting automotive body panels and parts such as doors, roofs, as well as manufacturing chassis components.
- Aerospace Industry
Used for machining metal components of aircraft, spacecraft, as well as outer casings and structural components of aerospace vehicles.
- Electronics Manufacturing
Used for cutting and processing metal enclosures, metal sheets, etc., for electronic products such as phones, computers, etc.
- Furniture Manufacturing
Shearing machines can be used for processing metal components of furniture such as tables, chairs, cabinets, etc.
- Metallurgical Processing Industry
Shearing machines are used in the cutting and shaping of metal sheets and steel during steelmaking and processing.
- Agricultural Machinery Manufacturing
Shearing machines are used for processing metal components of agricultural machinery such as harvesters, tractors, etc.
Top Shearing Machinery Manufacturers in 2024
- JMT
- JEAN PERROT
- Durmark
- Rajesh
- LVD
- Yangli
- Accurpress
- HARSLE
- KRRASS
- Primapress
How to Choose Shearing Machinery Manufacturer
During the purchase, the following points should be noted:
- Determine the specifications and parameters of the purchased machine according to your own needs and parameters, and at the same time consider the needs of future expansion of the enterprise, leaving a certain margin to determine the parameters of the machine. Especially for the shearing machinery, for the material thickness of the material to be sheared, the size of the slitting machine and other requirements, after the machine model parameters are determined, you can contact the manufacturer to purchase.
- Identify which manufacturers make the machine you want to buy. In this link, it is often the easiest to ignore, because no matter which manufacturer is contacted, the manufacturer will basically inform the professional production of this type of product. In fact, the models produced by different manufacturers are often different, and manufacturers often provide various products by adjusting goods. Therefore, users should pay special attention to choosing the one that suits them best. You can read this article to learn about the top 10 global shearing machine manufacturers, including China Hydrualic shearing machine companies.
- After contacting several companies that produce machines and obtaining the price, parameters, payment method and shipping method of the machine, the most important step is to choose the manufacturer to buy. Generally, after removing the highest price and the lowest price, choose a reliable manufacturer, so as to obtain a better price/performance ratio while ensuring the quality and after-sales service.
- Select several special manufacturers as a comparison to understand the use, quality of the machine, especially after-sales service. Taking all into consideration, choose the manufacturer with the best price and the best service.
- After confirming the manufacturer, the next step is to sign a contract, pay a deposit, take delivery or cash on delivery and other related matters. When signing a contract with a manufacturer, be sure to check whether the contract terms are breached or unreasonable.
- Obtain key documents, including quality inspection reports, product test reports, etc.