The shearing process in sheet metal is a fundamental operation in the realm of metalworking and manufacturing, crucial for the precise cutting of various materials, especially sheet metals. It involves the removal of material along a designated line by subjecting it to shear forces, resulting in a clean and accurate cut.
At its core, shearing relies on the application of force to cause plastic deformation in the material, effectively separating it along a predetermined path. This process is commonly executed using specialized machines called shears, which feature sharp blades arranged in a manner to facilitate efficient cutting.
Key components of the shearing process include the workpiece, which is the material being cut, and the shear blades, which execute the cutting action. The material is positioned between the blades, and as force is applied, the blades exert sufficient pressure to induce deformation and separation along the cutting line.
Various factors influence the effectiveness of the shearing process, including the material properties such as thickness, hardness, and ductility, as well as the blade sharpness, clearance, and alignment. Proper control of these parameters is essential to achieving precise cuts with minimal distortion or defects.
The use of shears in sheet metal production has diminished through the use of cut-off tooling in CNC punching and the use of shake-out technology to separate parts from the sheet skeleton. Shears are mainly used for shearing rectangles or strips for stamping and CNC press dies.
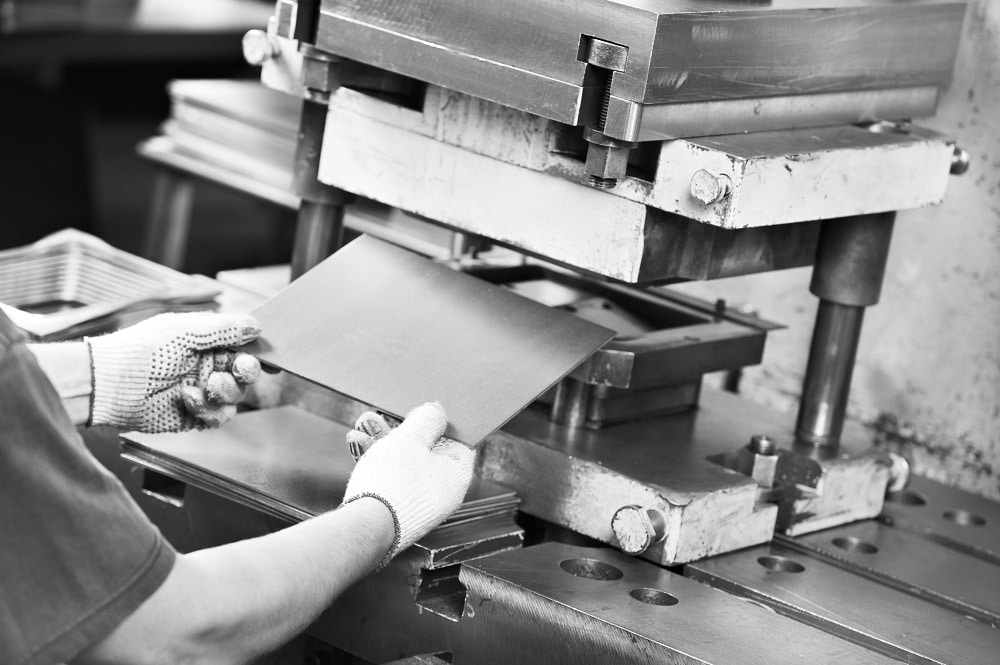
In those cases where shearing process is used to achieve final dimensions, the thickness of the material and the X-Y dimension of the part dic- tate the degree of precision which is feasible eco- nomically. Thicker material and greater X-Y dimensions require more generous tolerances.
In the broad range of sheet metal produc- tion, material thicknesses vary from 0.005 in. (0.13 mm) to 0.25 in. (6.35 mm) in ferrous and non ferrous materials. Shearing equipment varies, accordingly, from 1⁄4 in. (6.0 mm) capacity x 12 ft. (3.5 m) bed length to tiny hand operated shears with a 0.030 in. (0.8 mm) capacity and a 12 in. (300 mm) blade length.
In the X-Y dimension a tolerance of ±0.060 in. (1.52 mm) is used for thicker material and ±0.010 in. (0.26 mm) for thinner material. It is advisable to consult your metalforming supplier for the capabilities of available equipment.
Nature of Cut Edges
Whenever sheet metal is cut, whether by punches and dies, shear or slitters, the charac- teristics of the cut edges are similar (Figure 1).
Cutting action takes place in three stages as the cutting edge moves through the material: initial plastic deformation, penetration, and fracture. During initial plastic deformation, the “edge radius” or “roll over” is formed. During penetration, the “cut band” or “burnish” is cre- ated. And during fracture, the “break” or “break-off” and the burr are developed.
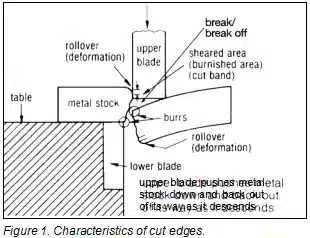
Shears and other metal cutting devices are normally maintained and adjusted to provide acceptable cut quality with nominal burrs and to limit wear on tooling and equipment. This produces a cut in which penetration occurs to a depth of approximately 1⁄3 of the material thick- ness and fracture occurs through the remaining material. Proper adjustment generates a burr which seldom exceeds 10% of the material thickness.
Equipment Characteristics
A wide variety of power shearing equipment is in use. Major machine elements common to most shears include the frame assembly, bed, table, ram, hold-down devices, gauges, the acti- vating mechanism and the blades (Figure 2). Hold-down devices, arranged along the bed near the blade, engage the stock and clamp it firmly in position for shearing.
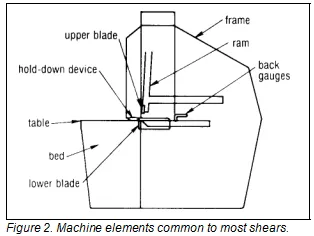
Back gauges serve to position the stock under the moving blade at a predetermined dimension. They may range from simple, posi- tive, mechanical stops to a series of probes (proximity switches) which sense the stock and activate the machine when more than one are contacted simultaneously. Depending on type and sophistication, back gauges may be set manually or programmed.
Front gauges are often used to position the stock, especially when large workpieces are involved. They may be either mechanical or programmable.
Side gauges, also known as “squaring arms,” are mounted perpendicular to the blade on either the left or right side of the bed, and assist in guiding and squaring the stock to the blade.
Operation
Regardless of construction, size or speed, all power shears operate similarly. A sheet of stock is advanced on the table until the back gauges are contacted and the line of cut is beneath the blade (Figure 3). When the machine is activat- ed, the hold-down devices clamp the stock and the angled moving blade cuts progressively across the sheet in a guillotine-like action.
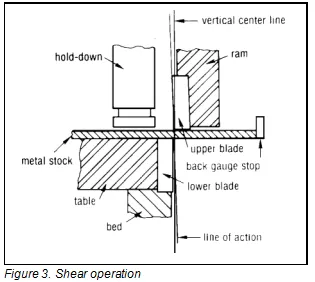
Depending on the application, power shears may be fed from the front or the back. Back feeding can reduce handling of the stock for subsequent cuts, but requires an additional operator.
Maintaining Quality
Important quality checks are performed dur- ing the shearing operation. Factors of quality control include the initial flatness of the stock, general surface and edge condition. Surface flaws and skid marks are common on coil and sheet products and are generally acceptable to the manufacturer unless such marks would cause cosmetic rejection of the finished prod- uct. Delamination, surface inclusions and other severe defects in the material may also be iden- tified and are cause for rejection.
Design Considerations
For economical production the knowledge- able designer recognizes several aspects affect- ing costs and quality during shearing and in subsequent operations. Following are several such product design considerations.
●Material Utilization:Material suppliers generally make sheet stock available in stan- dard sizes—widths of 30, 36, 48 and 60 inches. Significant savings can result from the effective use of these standard sizes by avoiding charges for extra slitting or mill preparation.Early consultation with the metalformer may permit modifying the dimensions of unseen flanges on the product to achieve an overall part layout somewhat smaller than the standard sheet size. This can avoid extra costs and reduce waste.
●Grain Direction:Grain direction in flat rolled stock (lengthwise in the coil) is not always a significant consideration. However, in some operations such as forming and bending, grain orientation can be important.On very large parts which have formed flanges or features, the designer should consult a qualified supplier prior to specifying the grain orientation and bend radius to determine if material size limitations will permit the formed features to be across the grain. This subject is explored in more detail in the chapters on Press Brake Forming and Stamping Production.
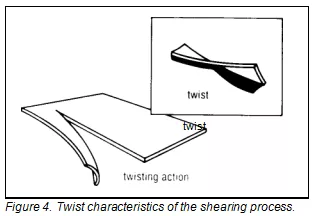
●Process Characteristics:Burrs, holddown marks and twist (Figure 4) are characteristics of the shearing process.
1. Burrs are present after shearing (as in any metal cutting operation) and are normally con- trolled within acceptable limits through proper shearing practices.
2. Hold-down marks, appearing as slight inden- tations along one side of the sheared edge of the workpiece, sometimes result from the clamping action of the hold-downs. These marks are seldom a problem. They may often be accommodated as part of an unseen flange in the final product, or may be eliminated entirely during trimming in later operations.
In critical applications, coverings on the hold-downs may be used to protect the stock. Materials with removable protective coatings are sometimes used to help reduce holddown marks and scratches that are inherent in the shearing process. These alternatives will add considerable additional cost.
3. Twist, a spiral-like curvature of the material occurs when shearing narrow strips. It is caused by the scissors action of the shear and is influ- enced by the relationship of the width sheared to the thickness and temper of the strip.
Twist is seldom an important consideration except when shearing narrow strips. When a job requires very narrow strips, roller slit coil mate- rial, (if order is of sufficient quantity) or bar stock can often be substituted.
Advantages of Shearing Process in Sheet Metal
Shearing typically is part of a bigger fabrication process, used to cut sheets into smaller sizes for use in the assembly of other products.
The shearing process in sheet metal production has the following advantages:
- Able to cut through varying diameters of sheet metal easily.
- Cost-effective means for cutting metal, especially when used in high-capacity operations.
- Produces clean, smooth-edged cuts.
- Produces no metal chips and is a virtually waste-free sheet metal cutting process.
- Quickly cuts through sheet metal in seconds.
- Requires no heating and can be done at room temperature.
- Versatile technique for sheet metal cutting, able to shear through metals that include aluminum, bronze, copper, iron, steel, and stainless steel.
There are a few disadvantages when using a shearing process in sheet metal, however. The process is less than ideal for lower volume production runs, and very hard metals – such as tungsten – cannot be cut using the shearing process. In sheet metal, it also sometimes deforms the sheets when blades are damaged or dull, because of improperly placed shear gaps or due to applying too much or too little pressure when being held down.
Another very similar sheet metal cutting process is known as die-cutting. The primary difference between shearing and die cutting involves the different types of cutting blades each sheet metal cutting process employs. While die cutting uses curved blades, shearing uses straight blades instead. Otherwise, both methods for cutting sheet metal produce straight lines to process metal sheeting with little to no waste.
Equipment Used for Sheet Metal Cutting Process
There are a number of ways to accurately achieve a smooth finish using the shearing process. In sheet metal production, many different types of machinery can perform shearing operations. Though certain machines or tools can operate manually, others use hydraulic, pneumatic, or electrical machinery. Standard shearing machines often include a table that features arms to support and guides to secure the sheet metal, along with straight-edged blades positioned above and beneath the sheets.
The sheet metal cutting process involves placing the sheet between these two blades, which are then forced together to cut the metal. With most shearing machines or implements, the lower blade is stationary while the upper blade applies a downward force on the metal sheet. Often, the upper blade is angled to ensure the force required continually lessens as the cut moves from one side to the other. For the shearing process in sheet metal, a number of different pieces of equipment can be used.
Alligator Shears
Using a hinged jaw, as per their namesake, alligator shears are used in a wide range of metal cutting operations. Powered via hydraulics, they typically are only used for cutting through smaller pieces of sheet metal.
Bench-Mounted Shears
Bench-mounted shears use a compound implement, which offers a better mechanical advantage. They are ideal for cutting medium-sized sheet metal workpieces into approximate shapes. Bench shears are versatile, able to make multiple types of cuts. These machines also come in various sizes with varying strengths and can produce clean, burr-free cuts.
Metal Guillotines
These are made up of lower and upper shears, a shear table, a device for holding the workpiece and a gauging mechanism. Metal guillotines are powered mechanically, hydraulically or manually via foot power. They work by holding the metal sheet with a ram and moving the metal blade down until it crosses a fixed blade, which cuts the metal. To reduce how much force is needed when cutting large pieces of metal, the moving blade can either be straight or set at an angle.
The sheet metal cutting process with guillotines offers both speed and economy to the shearing process. In sheet metal manufacturing, the machine is ideal for high-capacity assembly lines. As they tend to produce rougher edges than other implements used during the shearing process, in sheet metal production they are normally used to fabricate components where aesthetics are not important, or if they are to be welded later.
Power Shears
These shears are ideal for making blanks from large pieces of sheet metal. Cutting processes with power shears utilize electricity or pneumatics to run the machine, though the machine is operated by hand. The upper blade moves towards the lower blade, which stays in a fixed position and exerts tension to cut the sheet metal. Generally used for cutting straight lines or curves with larger radiuses, power shears offer flexibility, accuracy, durability, and efficiency.
Snips
Snips are hand tools designed specifically for the sheet metal shearing process. In sheet metal cutting processes, two general types of snips are used, compound action and tinner snips. The compound action snip offers a greater mechanical advantage due to a featured linkage and comes in several different varieties. These snips are used for stainless steel, mild steel or aluminum.
Tinner snips feature short blades with long handles, used commonly for cutting mild steel or tin with low carbon content. Tinner snips also come in different varieties. Used for their precision, they are primarily for more delicate sheet metal cutting processes. However, because they are operated by hand, cutting with snips is time-consuming.
Throatless Shears
Throatless shears are designed for making intricately curvy, irregular or straight cuts. Unlike many other shearing machines, throatless shears allow the workpiece to move freely.
Industries & Products That Use the Sheet Metal Cutting Process
Sheet metal cutting processes are used in many different industries. Generally, the production of sheet metal falls into three types.
These categories are:
Commercial sheet metal production involves making consumer goods, such as automobile bodies, appliances, vehicle hoods, caps, cans, mailboxes, cabinets, cutlery, and consumer electronics.
Industrial sheet metal production involves fabricating components used in other products, many of which are used to manufacture consumer products; industrial fabrication also involves making various implements like bandsaws, drill presses, hydraulic systems, and the like.
Structural sheet metal production involves the manufacture of components for construction, including structural framing studs for skyscrapers, ventilation systems, guardrails, brackets, gutters elevators, pipes, doors, metal siding, and roofing material.
Fabricating and shaping sheet metal is essential to the fabrication of a wide array of mass-produced items, and one of the more important elements of this practice involves shearing. In fact, sheet metal makes restaurants, food and beverage, farming, electronics, automobile, and many other industries possible.
To learn more about our sheet metal cutting capabilities, please contact us at Krrass Machiery today!