In the realm of modern industrial manufacturing, laser cutting technology has emerged as a powerful and revolutionary non-contact thermal processing technique. It has truly become an indispensable cornerstone, with its ability to utilize high-power-density laser beams to precisely melt, vaporize, ablate, or even ignite materials. The addition of high-speed airflow to whisk away the molten matter further enables the clean and accurate cutting of workpieces. However, as with any technological marvel, it is not without its drawbacks and limitations. The laser cutting machine, while a boon to productivity, can unfortunately have side effects on the human body. Therefore, understanding the side effects of laser cutting machines is essential. It is of the utmost importance that we delve deep into these side effects and take all necessary measures to ensure the safe and efficient use of this technology in the industrial landscape.
Basics of Laser Cutting
What is Laser Cutting?
Definition and Basic Principles
Laser cutting is a fascinating process that involves bombarding the workpiece with a highly concentrated laser beam of significant power density. This intense beam causes the material to rapidly undergo a series of transformations, melting it into a liquid state, vaporizing it into a gaseous form, ablating it away, or reaching the critical ignition point. Simultaneously, a precisely aligned high-speed flow of gas sweeps away the molten material, thereby achieving the clean and precise cutting of the workpiece. This remarkable technology has the versatility to cut through almost any material imaginable, be it two-dimensional or three-dimensional thin metals. The underlying working principle is a complex interplay of various elements, including the powerful electric and magnetic fields within the laser beam, the thermochemical reactions that occur as the material is heated and transformed, the fluid dynamics of the gas flow, and the constantly changing aerodynamics within the cutting zone. It is truly a marvel of modern engineering.
Brief History
The history of the laser cutting machine is a journey that dates to 1964, a time when the brilliant electrical engineer Kumar Patel made a groundbreaking discovery at Bell Labs in New Jersey. He invented the gas laser cutting process using a carbon dioxide mixture, a feat that would change the face of manufacturing forever. Since then, this technology has taken root and flourished in China. In 1976, a remarkable achievement was made when the CO2 laser cutting machine, jointly developed by the esteemed Changchun Institute of Optics and Mechanics of the Chinese Academy of Sciences and the Changchun First Automobile Manufacturing Plant Car Branch, along with other collaborating units, successfully cut the cover parts of the iconic "Hongqi" car. This was a momentous occasion that signaled the growing prowess of laser cutting technology in the automotive industry. Today, fiber lasers have emerged as the dominant force in cutting applications, and the average installed power in the market continues to soar year after year, a testament to the continuous evolution and improvement of this technology.
Types
The world of lasers offers several main types, each with its own unique set of characteristics and applications. The CO2 laser, with its remarkable efficiency and long lifespan, has found widespread use in industry, especially when it comes to high-speed cutting operations. It has proven to be a dependable workhorse in many manufacturing processes. On the other hand, the Nd:YAG laser is the choice of discerning high-end users, thanks to its outstanding beam quality and superior cutting efficiency. This laser is often favored for applications that demand the utmost precision. When it comes to selecting the right laser for a particular task, users must carefully consider the actual application requirements and the properties of the material to be cut. It is a decision that can impact the quality and efficiency of the cutting process.
Applications of Laser Cutting
Industries Benefiting from Laser Cutting
- Automobile Manufacturing Industry: The automobile manufacturing industry has wholeheartedly embraced laser cutting machines, and for good reason. These machines have become an essential part of the production process, being used to intricately process various components such as car doors, exhaust pipes, and many others. The traditional methods of manual or conventional processing often struggle to achieve the level of precision and efficiency required for these parts, which are often left with unsightly and unwanted edges or burrs. Laser cutting, however, swoops in like a hero, capable of handling even the smallest and narrowest of material areas with ease. It not only significantly reduces the amount of heat generated during the cutting process but also minimizes material waste, leading to a remarkable improvement in the precision and overall efficiency of automobile components. This means that cars can be built with greater accuracy and quality, ensuring a smoother and safer driving experience for consumers.
- Aerospace Industry: In the highly demanding and safety-critical aerospace industry, laser cutting technology has found its rightful place. It is applied with great care and precision in the production of crucial components such as aircraft fuselages and wings. The ability to achieve high-precision processing of materials is of utmost importance here, as even the slightest deviation could have catastrophic consequences. Laser cutting ensures that these parts are fabricated with the utmost accuracy, minimizing the effects of mechanical stress that could potentially compromise the structural integrity of the aircraft. This technology plays a vital role in ensuring the safety and reliability of air travel, allowing planes to soar through the skies with confidence.
- Electronics and Semiconductor Industry: The electronics and semiconductor industry are a realm where precision is king, and laser cutting technology has proven to be a worthy ally. It is employed in the delicate art of precision machining, enabling the production of high-precision and tight-tolerance components that are the lifeblood of this industry. From tiny microchips to intricate circuit boards, laser cutting allows for the creation of products that meet the exacting standards and demands of modern electronics. This technology has been instrumental in the rapid advancement of this industry, powering the devices that have become an integral part of our daily lives.
- Medical Devices and Equipment Industry: In the noble field of medical devices and equipment, laser cutting is a key player in the pursuit of high-precision manufacturing. It is used to craft a wide range of essential items, including life-saving surgical instruments, dental equipment, and other crucial medical devices. The precision and accuracy offered by laser cutting are invaluable in ensuring the effectiveness and safety of these medical tools. Every cut and contour are crafted with the utmost care, as the slightest imperfection could have serious implications for patient health. This technology is truly a lifesaver in the medical world.
- Decorative Industry: The decorative industry has also harnessed the power of laser cutting machines to bring beauty and creativity to life. These machines are used to cut intricate and complex patterns and graphics, such as those found on automotive interior panels. This allows for quick customization and the creation of personalized products that meet the ever-evolving tastes and preferences of consumers. Laser cutting has opened a world of possibilities in the decorative realm, enabling designers to push the boundaries of creativity and bring unique and stunning designs to market.
Common Materials Processed by Laser Cutting Machines
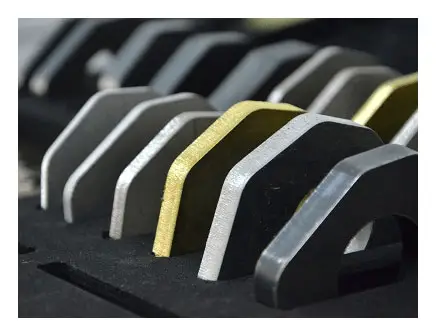
Laser cutting machines are like versatile artisans, capable of working with a diverse range of materials. Metals, plastics, and wood are just a few of the materials that fall under their cutting prowess. They can also manage non-metal materials with equal finesse. For instance, continuous laser cutting technology has been specifically designed to excel in cutting non-metal materials. The advantages of laser cutting technology are truly remarkable. Its wide range of processing capabilities means that it can manage an array of varied materials, adapting to the needs of various industries. The minimal deformation it causes ensures that the integrity of the material is maintained, while the high precision achieved is a testament to its technological superiority. Additionally, it is energy-efficient and can be automated, reducing the need for excessive human intervention. Compared to other cutting methods, laser cutting stands far above the rest. It offers a level of cutting precision and accuracy that is simply unrivaled, with significantly smaller heat-affected zones and less material deformation. This not only reduces material waste and the associated pollution but also lowers maintenance costs and enhances operational safety. It is truly a meaningful change in the world of cutting technology.
Health and Safety Side Effects
Physical Hazards
Eye Damage
During the operation of a laser cutting machine, the laser beam is a source of great danger to the eyes. With its high concentration and monochromatic nature, it has the potential to cause immediate and direct damage. Imagine staring at the cutting head for an extended period, observing the bright sparks flying, and suddenly feeling a sharp, stinging sensation in your eyes. It is a truly unpleasant experience. But the danger does not stop there. The laser light can focus on the retina, magnifying the energy intensity to a dangerous level, potentially causing severe damage to the cornea or retina. Infrared lasers are especially menacing in this regard. Even the body's natural protective "blink reflex" may not be enough to prevent immediate and potentially irreversible damage to the eyes. It is a risk that should never be taken lightly.
Skin Damage
When the laser beam contacts the skin, the consequences can be equally concerning. If the energy (power) of the laser is too high, it can cause damage to the skin. While the body has the remarkable ability to repair tissue to some extent, the functionality of the affected area may be compromised. Prolonged exposure to the laser is even more dangerous, as it can lead to burns and the formation of unsightly scars. The laser can inflict damage through photochemical or thermal burns, and depending on the wavelength, it can penetrate different layers of the skin, from the epidermis to the dermis, causing a range of damage levels. For example, UV lasers are known to be particularly harmful, capable of causing not only burns but also increasing the risk of skin cancer and accelerating the aging process of the skin. It is a sobering reminder of the importance of proper protection.
Respiratory Risks
The operation of a laser cutting machine can pose a significant threat to the respiratory system. As the machine cuts through materials, especially special metal materials, a combination of elevated temperature and gas is produced, resulting in the generation of copious amounts of dust. This dust is not just ordinary dust; it often contains a complex mixture of chemical components. Accidental inhalation of this dust-laden air can cause immediate irritation and damage to the respiratory system. But the danger does not end there. Long-term inhalation of these harmful substances can lead to a host of serious health problems. The respiratory mucosa becomes irritated and inflamed, and over time, the lung tissue can develop fibrosis, a condition known as welder's pneumoconiosis. This debilitating condition is often accompanied by other health issues such as manganese poisoning, fluorosis, and metal fume fever. The long-term effects are truly alarming, as they increase the risk of respiratory infections, asthma, bronchitis, and even lung cancer. It is a particularly concerning issue for vulnerable groups such as children and the elderly, who are more susceptible to the harmful effects of air pollution. We must take every precaution to protect those who work with or are exposed to laser cutting machines.
Auditory Side Effects
One cannot ignore the undeniable problem of noise generated during the operation of a laser cutting machine. The noise is not just a nuisance; it can have a profound impact on both hearing and the overall working environment. Picture a workshop filled with the deafening roar of the machine, drowning out all other sounds. Long-term exposure to such elevated levels of noise can leave a lasting imprint on a person's hearing and health. Scientific studies have shown that noise levels above 85 - 90 decibels can start to damage the delicate structures of the cochlea, the organ responsible for hearing. And when the noise reaches a staggering one hundred decibels, the damage can be irreversible, leading to permanent hearing loss. It is a silent threat that lurks in the background, gradually eroding the well-being of those who work in such environments. We must find ways to mitigate this noise pollution and protect the hearing of the workers.
Environmental and Mechanical Impacts
Air Quality Concerns
The laser cutting process is not without its environmental consequences. As the laser cuts through materials, it produces a significant amount of dust and fumes. These byproducts are not only a nuisance but can also be a serious threat to the environment and human health. The dust may contain toxic substances such as heavy metals and organic compounds, which, if released into the air and water without proper control, can cause widespread pollution. The smoke and harmful gases generated are in a gaseous state, allowing them to freely circulate within the workshop. If left unchecked, they can pose a serious risk to the health of the workers, potentially causing respiratory problems and other health issues. It is a situation that demands our immediate attention and the implementation of effective control measures to protect both the environment and the people who work in these settings.
Material Waste and Efficiency
Material waste is an issue that has plagued traditional cutting methods for years, and laser cutting is no exception. In traditional cutting processes, a large amount of material is often wasted due to the large cutting gaps and long distances required. However, laser cutting technology has brought a glimmer of hope in this regard. By optimizing the arrangement of parts and utilizing innovative tools like Fabricaide, it has the potential to significantly reduce material waste. This is not only beneficial for the environment but also makes economic sense, as it reduces the cost of raw materials and waste disposal. It is a step in the right direction towards more sustainable manufacturing practices.
Energy Consumption
The laser cutting machine is a power-hungry beast, with its main energy-consuming parts being the machine tool host, water cooler, and dust removal device. The high energy consumption not only contributes to increased operating costs but also has an impact on the environment. As we strive for more sustainable manufacturing, finding ways to reduce the energy consumption of these machines becomes a top priority. This could involve the development of more energy-efficient components, improved cooling systems, or the implementation of smart energy management strategies. Every effort counts in the pursuit of a greener and more sustainable future.
Operational Hazards
Equipment Malfunctions
Equipment malfunctions are an all-too-common occurrence in the world of laser cutting machines. Problems such as the machine failing to return to its origin when turned on, cutting circles that are far from perfect, and error messages like "exceeding limit data error" flashing on the panel display can disrupt production and cause frustration. Even more concerning are issues like leaks and ignition in the high-pressure headwater pipe of the laser tube, which can pose a serious safety risk. These malfunctions not only result in downtime and lost productivity but can also have potentially catastrophic consequences if not addressed promptly and properly.
Precaution Maintenance
To prevent these dreaded equipment malfunctions, precautionary maintenance is an absolute must. This involves a comprehensive approach that includes regular and meticulous checking of the equipment, timely maintenance, and repair, and ensuring that all components are in optimal working condition. It requires careful planning and scheduling, with a well-defined maintenance plan in place. Regular inspections should be conducted, and any issues should be addressed promptly. Keeping detailed records of equipment checks and maintenance reports is also crucial, as it allows for effective tracking and management of the equipment's operating status. By investing time and effort in precautionary maintenance, we can significantly reduce the likelihood of equipment failures and ensure the smooth operation of the laser cutting machine.
Safety Checking
In addition to precautionary maintenance, regular safety checks are an essential part of ensuring the safe operation of the laser cutting machine. This involves a thorough inspection of the electrical and hydraulic systems, ensuring that all connections are secure and dependable, with no loose or damaged parts. Adequate preventive measures should also be implemented, such as installing sturdy baffles to prevent cutting sparks from flying and causing potential harm. These safety checks are not just a formality; they are a crucial line of defense against accidents and injuries.
Fire Risk
Although laser cutting machines are designed to operate with a certain level of safety, the risk of fire is always present, especially when dirt and debris accumulate. A small spark can quickly ignite these combustible materials, leading to a potentially disastrous fire. In the event of a fire, quick and decisive action is required. If the fire is small, it can be extinguished using a fire extinguisher but always remember to cut off the power supply first to prevent further complications. However, if the fire grows out of control, it is essential to sound the nearest alarm and evacuate the area immediately. Do not use the elevator, as it may become a death trap in a fire. Instead, make your way to the nearest exit and help others to do the same. Close the doors to the fire area and its surroundings to contain the fire and smoke, but do not lock the doors, as this could impede the efforts of firefighters. Fire safety is a matter of life and death, and we must always be prepared.
Operator Error and Training
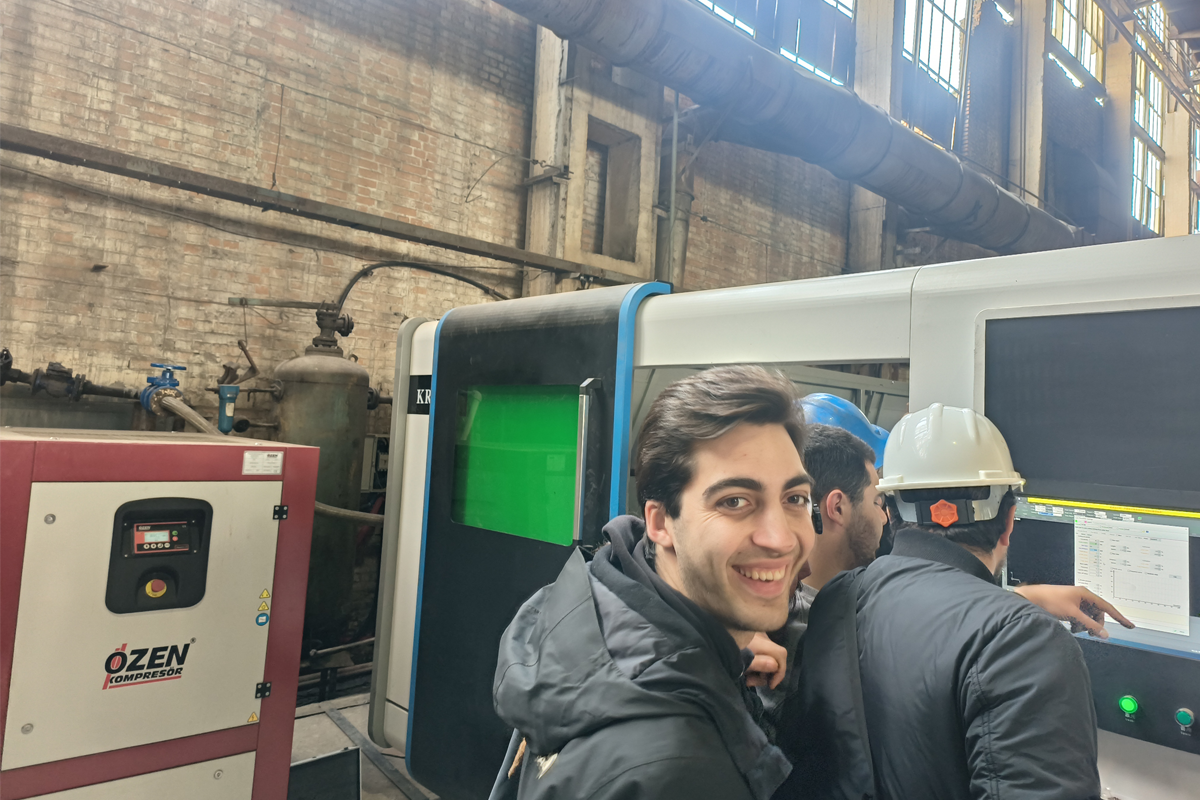
The actions of the operator play a crucial role in the safe operation of the laser cutting machine. Improper operation can lead to accidents that could have been easily avoided. This is why regular technology updates and comprehensive training courses are of utmost importance. These training programs should cover a wide range of topics, including the latest technological advancements, safety operation procedures, operation techniques and precautions, safety and maintenance knowledge, and the proper use of eye protection equipment. By providing operators with the necessary knowledge and skills, we can help them better adapt to the working environment and significantly reduce the risk of safety incidents. A well-trained operator is not only more efficient but also a key factor in maintaining a safe workplace.
Mitigating the Side Effects of Laser Cutting Machines
Safety Equipment and Protocols
When it comes to protecting oneself from the potential hazards of laser cutting machines, safety equipment is our first line of defense. Laser protective goggles, protective eye masks, and protective clothing are essential items that can effectively shield the eyes, skin, and hands from the harmful effects of laser radiation and flying splash materials. These items are not just accessories; they are life-saving equipment. Additionally, strict adherence to specific safety protocols is non-negotiable. Prohibiting smoking in the cutting area, especially near oxygen cylinders, is a simple yet crucial rule that can prevent a potential disaster. The presence of multiple fire extinguishers and other safety equipment is also vital, as they can provide a quick response in case of an emergency. When choosing a laser cutting machine, it is essential to select a reputable supplier whose machines comply with FDA regulations. This ensures that the equipment meets the highest standards of safety and quality.
Training and Awareness
Continuous safety education is the cornerstone of a safe working environment. This education should be comprehensive and cover a wide range of topics. Theory training provides the foundation, explaining the principles and potential risks associated with laser cutting. Safety operation procedures are the practical guidelines that operators must follow to ensure their safety and the proper functioning of the machine. Operation techniques and precautions equip operators with the skills and knowledge to manage the machine safely and efficiently. Safety and maintenance knowledge is essential for understanding how to keep the machine in good working condition and prevent malfunctions. And let us not forget the importance of eye protection, which is often overlooked but can mean the difference between sight and blindness. By offering a continuous stream of safety education resources, we can raise awareness and ensure that everyone involved in the operation of laser cutting machines is well-informed and prepared.
Technological Advances
The field of laser cutting technology has witnessed remarkable progress in recent years. The development of super high-power fiber laser cutting technology is a prime example of this innovation. This technology has revolutionized the cutting of thick sheets, allowing for fast and high-quality results. The ability to use air as an auxiliary gas has further enhanced its capabilities, making the process more efficient and cost-effective. It is truly a meaningful change in the industry, opening new possibilities for manufacturing.
The use of flat laser cutting machines has also had a significant positive impact. By optimizing the cutting process, these machines have been able to reduce waste and improve the utilization rate of remaining materials. This not only benefits the environment by minimizing material waste but also helps businesses save on costs and increase productivity. It is a step towards more sustainable and efficient manufacturing.
Moreover, the application of laser cutting in the medical field, such as in bloodless incisions and minimally invasive surgeries, has been a breakthrough. This technology has reduced the risks associated with traditional surgical methods, allowing for more precise and less invasive procedures. It has not only improved patient outcomes but also increased the efficiency of surgical operations. Surgeons can now perform complex procedures with greater accuracy and less trauma to the patient.
As technology continues to advance at a rapid pace, laser cutting machines are gradually evolving towards automation and intelligence. This means that they will be able to operate with even greater precision and efficiency, reducing the need for human intervention and minimizing the potential for errors. The future of laser cutting technology looks bright, with the potential to transform various industries and improve our lives in countless ways. We can look forward to even more innovative applications and advancements in the years to come.
Conclusion
Although laser cutting machines have undeniably revolutionized production efficiency, we cannot ignore the potential harm they can cause to the human body. It is, therefore, of paramount importance that we take initiative-taking steps to address these issues. Strengthening safety awareness among operators and those working in proximity to these machines is the first and most crucial step. This can be achieved through comprehensive training programs and the dissemination of safety information.
Implementing effective protection measures is equally essential. This includes providing and ensuring the proper use of safety equipment such as goggles, masks, and protective clothing. Regular maintenance and safety checks of the machines should also be conducted to prevent malfunctions and ensure their safe operation.
Furthermore, continuous technological innovation is the key to mitigating the side effects of laser cutting. By investing in research and development, we can develop safer and more efficient laser cutting technologies. This will not only protect the health and safety of workers but also contribute to the sustainable development of the industry.
In conclusion, by working together to enhance safety awareness, implement protection measures, and drive technological innovation, we can minimize the negative impact of laser cutting on human health and promote the healthy and sustainable development of this powerful technology. Let us strive towards a future where the benefits of laser cutting can be fully realized without compromising the well-being of those involved. KRRASS Machine Tool, as a specialized company in producing laser cutting machines, is committed to providing high-quality and safe equipment. We are always ready to offer our expertise and assistance. Whether you need to browse our official website for more information or seek help from our professional sales team, we are here to support you in your journey towards safer and more efficient manufacturing.