Abstract: If you or your company are considering purchasing a press brake to increase the processing capability of parts and improve production efficiency, please read the following information carefully. This could be of assistance to you or your company.
Many corporate decision-makers have experienced economic losses due to purchasing the wrong equipment.
I am not overstating when I say that this scenario occurs frequently.
KRRASS has been manufacturing sheet metal processing equipment for several decades, and we have witnessed many such incidents.
However, suppose you are willing to take the time to conduct thorough research. In that case, you can clearly understand the type of press brake you or your company needs, the critical factors to consider when purchasing a press brake, and how to make the correct and practical decision.
For a company looking to purchase a press brake, the manufacturers will provide various pricing options with multiple configurations.
However, as a buyer, considering all factors can be challenging. Where should you start to decide which type of press brake to choose?
The best approach is to assess your or your company's needs and use them as the core criteria when selecting a press brake.
Where should you start? The following press brake purchasing guide may be helpful to you or your company. Let's delve into it together.
What is a press brake?
You may already know the definition of a press brake, but we still want to emphasize what it is.
Many first-time buyers of press brakes or those purchasing them for their companies may need to become more familiar with what it is.
A press brake is used to bend metal sheets and comprises a worktable, slide, back gauge, hydraulic cylinder, and other parts. Using simple punches and dies, we can easily bend the metal sheet and shape it into a specific geometric shape. When turning metal sheets of different thicknesses, the opening size of the lower die's V-groove also varies, and the bending pressure required is additional. (A bending pressure gauge can calculate the needed bending pressure.)
What are the commonly overlooked considerations when purchasing a press brake?
1. Market share
In today's online ecosystem, when you search for a product online, you will likely see many manufacturers exaggerating their effects while discrediting their competitors. However, the most reliable product quality indicator is often its market share. You can determine which machines and equipment are widely used and well-received in different industries based on user feedback and which could be better and recommended. User feedback and reputation are essential because they offer primary perspectives and direct interaction with the product. We recommend paying attention to this feedback.
2. Enterprise scale
When considering a product purchase, it's essential to feel the manufacturer's reputation and the quality of their after-sales service. In today's internet age, it can take time to discern a company's trustworthy reputation from marketing claims. However, by examining the market share of a particular product brand in your industry, you can better understand its popularity and reliability.
It's also essential to look for a reputable and healthy company, as this often indicates that they are trustworthy and can provide reliable after-sales service for users. To assess a company's scale and strength, it's recommended to personally visit their factory to understand their formalities and production strength. If a visit is not possible, online factory inspections can also be conducted through video or other online methods.
KRRASS Machinery considers the different situations of users and provides online factory inspection services. Click here to start your online factory inspection journey.
3. Machine quality
The two points mentioned above are common-sense terminology unrelated to the machine itself. Now let's discuss the quality of the device.
If you are still getting familiar with press brakes, comparing the quality of machines may take a lot of work.
The size and weight of the machine are the key factors that need to be considered. Usually, more extensive and heavier machines are more robust and of higher quality because they mainly use steel in the machine.
Another critical factor is precision. Ideally, you can bring (or ship) the parts you need to process to the factory to test the accuracy of the machine, but this is only sometimes feasible. The precision of the device is affected by the back gauge, the strength of the machine body, and the mold.
If the back gauge is still chain-driven, then the accuracy of the machine cannot be guaranteed. Aluminum beams may look attractive but will likely deform after repeated collisions.
The third important factor is the screw and guide rails. Excellent companies often choose to use ball screws and linear guide rails.
Finally, the strength of the body pillar is directly related to the thickness of the selected plate. The body's power will significantly reduce if the container is too thin.
4. Punches and dies
If we compare a press brake to a soldier, the tooling is their weapon. If the quality of these weapons could be better, it would be easier to defeat the enemy.
Therefore, how can we evaluate the quality of the tooling?
The most crucial factor is the material used. Currently, 42CrMo is considered a premium material for press brake tooling, while other materials, such as Cr6W2Si, are also regarded as good choices. Ordinary users may need to learn related knowledge to distinguish these materials.
In addition, most tooling undergoes high-frequency quenching. Some manufacturers use tooling that only undergoes heat treatment at the cutting edge. However, high-quality manufacturers will use tooling that undergoes overall heat treatment.
Tooling that has undergone overall heat treatment has a hole in the tooling, a clear sign of general heat treatment.
It's important to mention that the manufacturing expenses for tooling that has undergone comprehensive heat treatment are considerably more expensive than tooling that has only undergone heat treatment at the cutting edge.
Four Guidelines for Selecting a Press Brake
When selecting a press brake, it's essential to take into account the following four principles:
Principle 1: Precision of the mechanical system's operation.
It's common knowledge that certain physical inaccuracies regarding the bending radius are unavoidable, but the concern is the degree of deviation that users can tolerate. For relatively uncomplicated machined components, minor discrepancies in accuracy may be acceptable. Still, high accuracy is usually required for most machined parts, mainly when these parts are used for production after bending.
Principle 2: Flexibility of the mechanical system required.
The more types of machined parts, the greater the demand for flexibility of the press brake. In other words, the press brake should be designed with user-friendliness in its hardware and software components. It should allow for easy expansion to ensure maximum cost-effectiveness. This way, even if the user's machining orders change frequently and there is little repetition, the time for adjusting the press brake parameters can be minimized.
Principle 3: Determine the production capacity and size of the press brake.
When choosing a press brake, it is necessary to consider the parts' size, pressure, bending length, stroke, and structural height.
Principle 4: Potential customers should also carefully consider the machine's ultimate purpose, potential known deformation, and the bending radius of the machined parts.
When purchasing a press brake, seven factors need to be considered.
Press brakes have differences in machining and technology compared to other CNC equipment. As a user of the equipment, before purchasing a press brake, you must consider all relevant factors, such as the application, deflection, bending radius, and other machined parts.
As a decision maker for equipment procurement, you must understand a press brake's performance, processing range, functions, and precision.
This is a matter of concern, as any wrong decision can increase production and possibly unrecoverable costs.
Therefore, before purchasing a press brake, consider the following seven factors, which may help you make the right choice.
1. What kind of parts do you want to produce?
Your goal in purchasing a press brake is to efficiently process your production tasks, not to buy the smallest and lightest machine possible. Most importantly, you need to consider the material type of the metal sheet and its maximum thickness and length.
For a stainless steel sheet with a maximum thickness of 3mm and length of 2500mm, an 80-ton press brake utilizing air bending would meet the requirements. However, if you need to use a bottom die, consider purchasing a press brake of about 150 tons.
If you use a low-carbon steel sheet with a maximum thickness of 6mm and a length of 2500mm, a 100-ton press brake is suitable for air bending. However, consider a more significant CNC press brake if you need to use a bottom die.
For metal sheets with a length of 1250mm or less, a smaller CNC press brake is sufficient to meet your needs. This can significantly reduce your purchasing costs. The metal sheet's size is critical in choosing the most suitable press brake.
2. Compensation system
Deflection errors are inevitable in the bending process of CNC press brakes, especially for longer workpieces.
The deflection of the press brake increases proportionally with the length of the workpiece.
Under identical loads, a press brake processing a 2500mm plate will experience four times more deflection compared to processing a 1250mm plate.
In other words, shorter press brakes with fewer shim adjustments can produce higher precision products.
Reducing shim adjustments can also shorten the preparation time of the press brake.
Fortunately, most CNC hydraulic press brakes have added hydraulic deflection compensation during manufacturing, reducing the need for operator adjustments and dramatically improving bending accuracy and production efficiency.
The CNC system controls this function.
An electromagnetic servo valve allows hydraulic oil to flow into the compensation cylinder, which causes the worktable to move upwards. As the working pressure of the press brake increases, the deflection compensation force also increases, efficiently compensating for any deflection.
Automatic offset compensation is another less efficient compensation method.
3. Material type
Compared to regular carbon steel plates, the bending pressure required for stainless steel plates increases by around 50% during the bending process. However, the needed bending pressure decreases by 50% for softer aluminum plates.
The press brake manufacturer can acquire the bending pressure parameters as per the standard.
The following data table shows the bending pressures required for 1000mm metal plates of various thicknesses and materials.
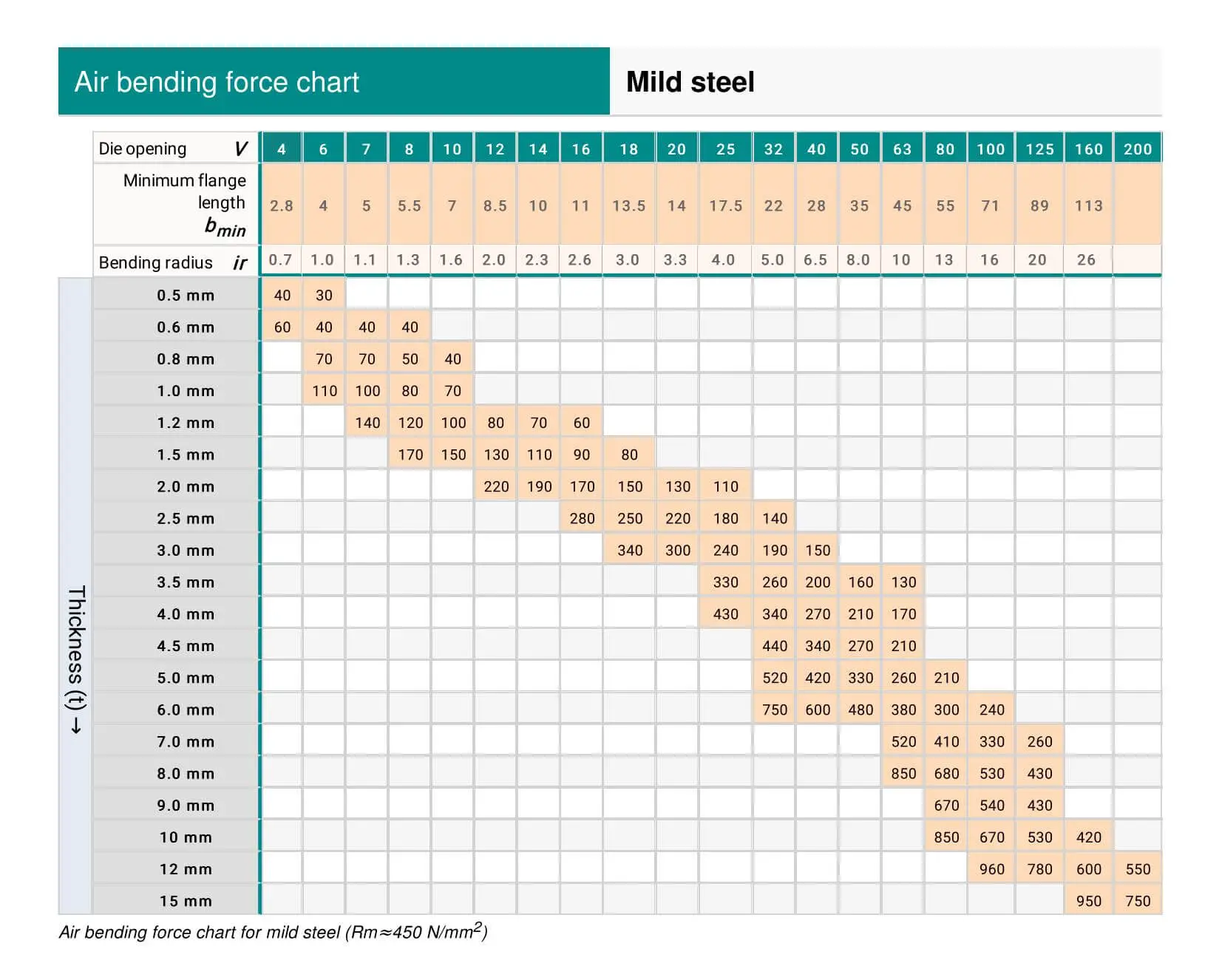
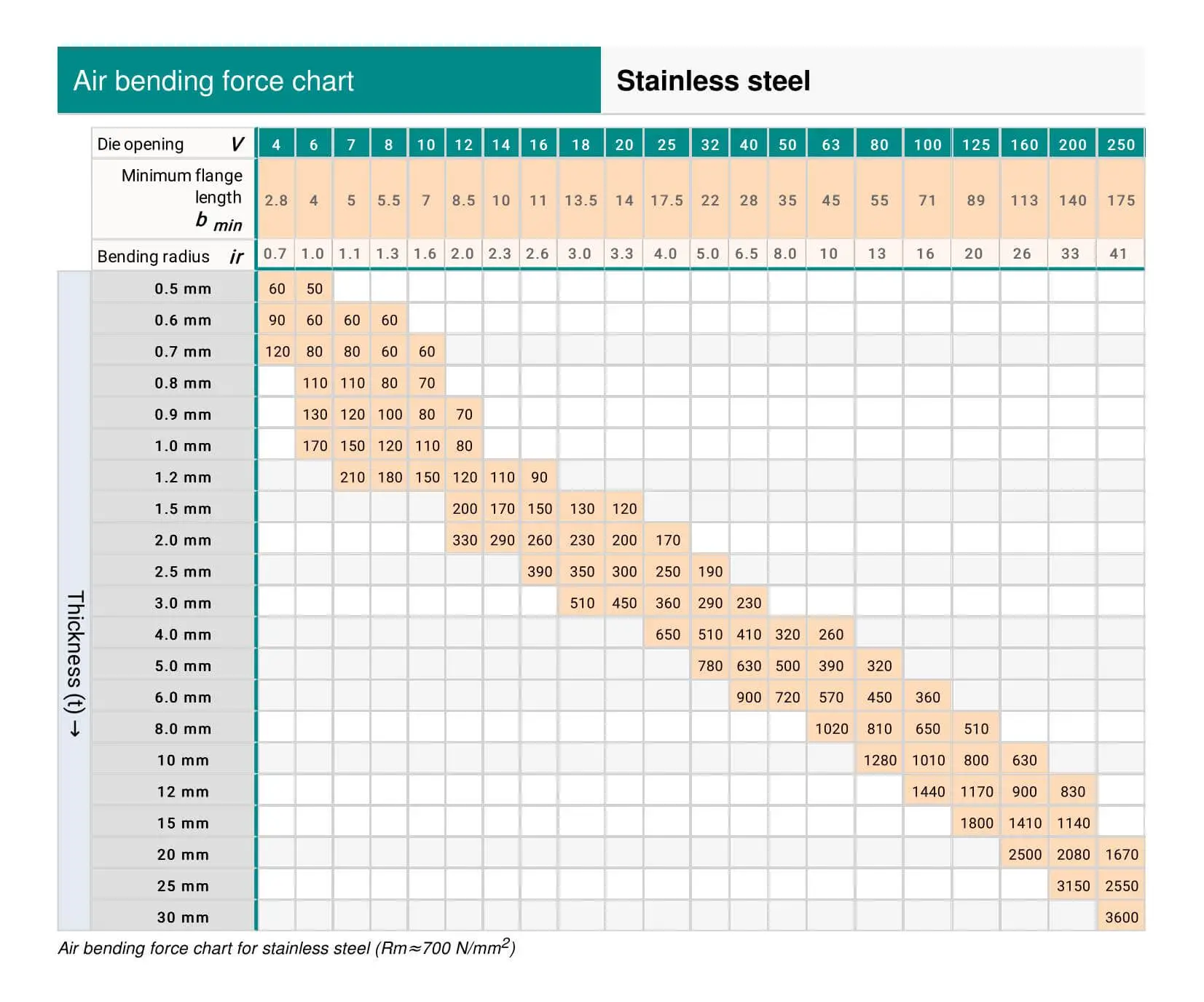
Previous image
Next image
There is also a quick way to calculate the required bending pressure for a press brake. You can use our online press brake pressure calculator to calculate the necessary press brake pressure in tons.
4. Bend radius
During air bending, the opening size of the lower die V-groove should be greater than eight times the thickness of the metal sheet.
For example, if a press brake with a lower die V-groove opening of 12 mm is used to bend a low-carbon steel plate with a thickness of 1.5 mm, the bending radius should be 1.9 mm.
If the bending radius is approximately equal to or smaller than the thickness of the metal sheet, then bottom bending is recommended.
However, in this case, the required bending pressure will be four times that of air bending. When performing air bending, it's essential to take note of the clearance between the upper and lower molds at the punch and die's base, as well as the spring-back force of the metal sheet after being bent to a 90° angle. Typically, the molds will cause the press brake to have a spring back angle of less than 2 degrees during air bending.
Therefore, for standard upper and lower mold bending processes, the angle of the upper mold punch should be between 86° and 90°.
At the bottom of the bending stroke, there should be a gap slightly larger than the thickness of the metal sheet.
5. Bend angle
The punch angle is improved because a larger bottom die is used, with a bending tonnage four times that of the blanking die. This helps reduce the spring back force within the specified bending radius.
Bottom die bending is similar to blanking, with the only difference being that the front end of the punch is converted to the required bending radius. Since the clearance between the top and bottom dies at the bottom of the bending stroke is smaller than the thickness of the metal sheet, and the bending pressure (which is ten times greater than the blanking pressure) is sufficient, this results in a reduction in the spring back force. The front end of the punch will fully contact the metal sheet.
To guarantee the durability of the press brake and ensure high-quality end products, selecting a bending machine that employs the blanking bending technique with a bending radius more significant than the metal sheet's thickness is advisable. This approach ensures high-quality end products while promoting the press brake's long-term use.
6. Bending accuracy
Choosing between a CNC press brake and a conventional press brake depends on the precision required.
A CNC press brake should be considered if a precision of ±0.5 degrees is required and cannot be changed. The repositioning accuracy of the slider can be controlled to within ±0.01 mm.
For high-precision bending workpieces, a high-precision and high-performance press brake is required.
However, the repositioning accuracy of a conventional CNC press brake slider is about ±0.5 mm, which can still produce a deviation of ±2-3 degrees under appropriate conditions.
In addition, CNC press brakes are usually equipped with a CNC controller and quick-change punch fixtures. This should be the primary consideration if you must process many small parts.
7. Punches and dies
The selection of the press brake's die directly impacts the precision of the bending process for metal sheets.
Therefore, it is crucial to inspect the punch and die carefully.
The dies come in various shapes, and different punches and dies are used for other parts.
To achieve the ideal shape of the part, the material's physical properties are mainly changed through the forming process.
Bending dies to process blank materials into parts with specific shapes and sizes under leaning pressure.
The dies used for press brakes are typically classified as either convex or concave, and they serve different purposes in sheet metal stamping and separation. A forming die has a cavity to create a specific shape, while a separation die has a blade to cut the sheet metal.
Bending dies generally made of T8 or T10 steel, and some better dies may use 42CrMo material, which has higher strength, better toughness, and wear resistance.
Cr12MoV, a type of cold-rolled die steel, is also a highly suitable material for this purpose.
42CrMo is a type of high-strength alloy steel quenched and tempered. It possesses excellent strength and toughness and can operate effectively under temperatures below 500 degrees Celsius. To ensure the longevity of each die, it's crucial to monitor wear and tear regularly. One way to check for wear on each die is to measure the die length directly from the front to the shoulder and the distance between the shoulders.
For standard dies, the allowable deviation per foot should be approximately ±0.001 inches, with a maximum total length deviation of ±0.005 inches.
For precision dies, the deviation per foot should be within ±0.0004 inches, and the total length deviation precision should not exceed ±0.002 inches.
It is best to use delicate dies for CNC press brakes and regular dies for manual and ordinary press brakes.
Answers to some common questions before deciding to purchase a press brake
How many types of press brakes are there?
Many types of press brakes depend on different needs and development stages, including manual press brakes, pneumatic press brakes, mechanical press brakes, hydraulic press brakes, hybrid power press brakes, servo-electric press brakes, fully electric press brakes, and so on.
How many types of press brake molds are there?
There are many types of press brake molds, including standard upper die for right-angle bending, acute angle upper die, flattening upper and lower dies, rounded upper die, gooseneck upper die, 1V to 4V lower dies, polyurethane lower die, hard rubber lower die, lower die guide, lower die seat, off-center die, forming die, flanging die, bending die set, and seamless bending die.
In addition, various non-standard punches and dies can also be designed to meet different needs.
1. Universal standard punch and die:
Used for bending between 90°~180°.
Advantages: suitable for thick and thin plates, durable, and widely used.
2. Acute angle punch:
Used for bending between 20°~180°.
Advantages: can bend small angles and dimensions, small radius after bending, beautiful, and angular.
3. Gooseneck punch:
Used for bending between 30°~180°.
Advantages: widely used for U-shaped products that cannot be completed with standard molds and acute angle punches.
4. Flanging die:
Used for flanging, suitable for use with acute angle punches.
First, use the sharp angle punch to bend the workpiece to an angle of less than 45°, and use the flattening die to press the flange, mainly used for reinforcing the frame.
5. Step difference die (also called Z-shaped die):
Mainly used for one-time bending of small Z-shaped workpieces, with fixed and adjustable types.
6. One-time forming die:
Including rounded corner forming die, door frame creating a die, U-shaped forming die, lamp pole forming die, etc.
It is usually used for bending complex products with multiple bending angles and styles, so one-time bending forming dies are designed to improve bending accuracy and efficiency.
7. Concentric mold
Refers to the lower die used to support the CNC press brake, composed of a mold frame and a segmented lower die.
Concentric means that when using any slot, replace the designated slot without re-centering the punch and lower die position, which is convenient for mold changing and has high bending accuracy.
Automatic compensation or hydraulic compensation, which one should be chosen?
When using hydraulic compensation, the compensation pressure is separate from the pressure of the entire system. This means that when the compensation valve works, the pressure of the whole system will decrease partially. In addition, problems such as oil leakage and pollution can occur in the hydraulic oil control system if there are such problems as tube rupture, aging of the compensation cylinder seal ring, or loose joints.
In contrast, automatic compensation relies on the CNC system to compute the required adjustment based on the material thickness, length, and the chosen mold. The system module then controls the compensation motor to adjust the deformation amount by reversing its rotation, with feedback provided by a potentiometer.
One advantage of automatic compensation is that the compensation deformation does not change with the holding time of the slide, and power is not required every time the drop enters the deceleration position. This helps to save energy throughout the entire system and eliminates the risk of oil leakage and pollution. Additionally, the use of a whole worktable also reduces manufacturing costs.
Open loop or closed loop for a press brake?
Closed loop
Closed-loop control of a press brake, also known as a feedback control system, compares the system’s actual output with the desired value, generates an error signal, and then uses it to control and adjust the work to make it close to the desired value.
Closed-loop control has high precision and fast response speed because it considers the operation of each part of the machine tool. However, compared to open-loop systems, closed-loop systems are more complex and expensive because they involve multiple components.
Open loop
Compared with closed-loop control, open-loop control of a press brake does not provide feedback on the current control results of the system. Therefore, the accuracy of the bending process in an open-loop device depends entirely on the precision of each component of the machine.
The system cannot control or compensate for parameter changes during bending, resulting in lower accuracy. External interference can also cause changes in the internal parameters of the machine, but the open-loop design is more straightforward, more stable, and easier to install and maintain.
Conclusion
Therefore, choosing open-loop or closed-loop control depends on your specific budget and the requirements of the bent workpiece. However, it should be noted that if you choose a closed-loop system, you must select a company with solid research and development capabilities. Only such enterprises can genuinely make the closed-loop function of the press brake play a long-term and uninterrupted role. Usually, small enterprises need the ability to effectively utilize the closed-loop system on the bending device.
What is the difference between a CNC press brake and a conventional press brake?
The following article explains in detail the differences between a CNC press brake and a conventional press brake:
To sum it up, the primary distinction between them lies in the presence of computerized control and automated feedback. This leads to differences in processing speed, accuracy, and efficiency.
What factors affect the price of a press brake machine?
The cost of a CNC press brake machine is influenced by several key factors, such as the machine’s tonnage, body width, component brands, mold types, product quality, and the level of after-sales service provided.
What brand of press brake is better?
The top ten press brake brands in the world are the best choices. You can choose according to your geographic location and the brand’s popularity in the local market.
The following link can provide you with information about the top ten press brake brands:
Electro-hydraulic servo press brake:
The hydraulic control system synchronously controls the two main cylinders on both sides with an electric proportional valve and grating ruler and is independently owned by the CNC system. Accurate feedback data ensures the accuracy of the slide movement.
Torsion bar synchro press brake:
The left and right swing rods are connected by a torsion bar to form a torsion bar-forced synchronization mechanism, which keeps the up and down movement of the two cylinders on both sides synchronized.
How to choose a CNC system for a press brake?
When choosing a CNC system for a press brake, several popular brands, such as Delem, Cyblec, and ESA, can be considered. Many press brake manufacturers also use their own in-house CNC systems. If you want to make an informed decision, we recommend extensive research before selecting a CNC system for your press brake. You can find comprehensive guidance on this topic by following the link below:
How to buy a good press brake?
If you have read the above content carefully, you should now clearly understand the factors to consider when purchasing a good press brake. The next step is to communicate directly with manufacturers, gain a deeper understanding of them and their products, and decide based on your budget.
Final thoughts
KRRASS has been serving the press brake manufacturing industry for decades, and we understand the importance of customers purchasing high-quality press brakes. "Good" refers to quality and includes reasonable prices and high-quality after-sales service.
We have seen too many examples where customers purchased press brakes from small factories, encountered problems without receiving technical support, and eventually contacted us to repurchase equipment. We have also witnessed agents losing a lot of money due to choosing the wrong press brake manufacturer brand.
To prevent these issues, it is highly recommended that you conduct extensive research on your options before making a final decision. Trust us; the time you invest will be worth it.
Before you go, perhaps you would like to see: