In modern industry and construction, the bending of pipes plays a vital role in creating complex pipe structures. To ensure precise and efficient bending, tube bending machines have become indispensable tools. This article will offer a comprehensive overview of tube bending machines, exploring their operating principles, different types, applications, and providing detailed guidelines for their operation and maintenance. Whether you're a beginner or an experienced professional, this article aims to provide valuable insights and practical knowledge to help you understand and work with tube bending machines effectively.
What is a Tube Bending Machine?
Pipe bending is a metal processing process that bends pipes into various shapes to meet different purposes. This process is widely used in the field of metal fabrication. Tubes formed by the tube bending process are not limited to any particular metal, but are suitable for different materials, including most metals and alloys.
When it comes to pipe bending, there is no set method, but many different options to achieve the pipe bending effect. Each method has its own unique advantages, disadvantages and prices.
One of the common methods of pipe bending is by using a pipe bender. The pipe bender is capable of precise bending of pipes and is suitable for mass production. Another method is manual pipe bending, which bends pipes by hand, which is suitable for processing needs of small batches and special shapes. There are also some advanced pipe bending techniques, such as cold pipe bending and hot pipe bending, which can achieve more complex pipe bending, but usually require more specialized equipment and technology.
Each pipe bending method has its applicable scenarios, and the selection of the appropriate method depends on factors such as specific processing requirements, pipe materials, and costs. Understanding different pipe bending methods can help practitioners in the metal processing industry make informed decisions based on actual conditions and improve production efficiency and quality of pipe processing.
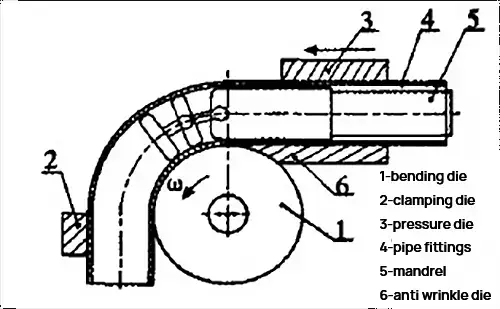
How Tube Bending Machines Work
Tube bending machines can be categorized into different types based on their bending methods, including push bending, roll bending, compression bending, and ring bending. Among these techniques, ring bending stands out as it offers relative ease in automation, making it the preferred choice for most tube bender machines. Visual illustrations can facilitate an understanding of the bending process's principles, effectively depicting the various steps involved.
The bending process utilizes a mandrel, clamping dies, and pressure dies. The mandrel is mounted on the spindle, while the clamping dies are used to secure the workpiece, preventing axial movement. The force fails to consist of a guiding die and a following die. During bending, the guiding die applies appropriate pressure to the workpiece to prevent wrinkling while the next die moves along with the workpiece. A mandrel is also used to support the inner cavity of the workpiece, preventing wrinkling, flattening, thinning, or other deformations during bending.
The spindle rotates, causing the tube to wrap around the mandrel and form a curve. The process also involves feeding the workpiece, preparing the space for the next bend, etc. The radius of the mandrel determines the bending radius, and different bending radii can be achieved by replacing mandrels of different radii.
Structure and Working Principles of Automatic Tube Bending Machines and Electro-Hydraulic Tube Bending Machines:
The hydraulic system of a tube bending machine consists of an electric oil pump, high-pressure oil pipes, quick connectors, working cylinders, and plungers. The bending head of the device includes upper-pressure plates, lower-pressure plates, die heads, and rollers—the electric oil pump outputs high-pressure oil sent to the working cylinders through high-pressure oil pipes. The high-pressure oil drives the plungers in the working cylinders to generate thrust, thus achieving bending through the bending head.
Types of Tube Bending Machines
Tube bender machines are machines used to bend tubes into various shapes, such as I-beams, channel steel, angle steel, wire, and more. They can also create coils, "U" shaped semi-pipes and spiral pipes. The categories of tube bender machines include hydraulic electric tube benders, horizontal hydraulic tube benders, and multifunctional coil tube benders.
Electric tube benders derive power from electricity, motors, gearboxes, and chain drives. In contrast, hydraulic tube benders rely on hydraulic pressure to perform various bending operations, including clamping, bending, auxiliary forward and backward movement, feeding, and core retraction.
Hydraulic tube benders are commonly used flat-circle automatic bending machines with multifunctionality, well-designed structures, ease of operation, convenient mobility, and quick installation. They find wide applications in electrical construction, highway and railway construction, boiler manufacturing, bridge construction, shipbuilding, furniture decoration, and more.
On the other hand, CNC tube benders utilize servo motors instead of hydraulic power. They can control feed and retraction, angle rotation, tube bending and retraction, auxiliary forward and backward movement, and head lifting. CNC and hydraulic tube benders differ in continuous production, processing precision, and the three-dimensional forming of pipe fittings.
CNC tube benders can cause cold bend pipes with a single or double bending radius and are widely used in various industries, including automotive and air conditioning, for bending multiple pipe fittings and conductors.
Tube Bending Process
The tube bending process begins by loading a tube into a tube bender and securing it between two primary dies: the clamping block and the forming die. The tube is also supported by two additional dies, the wiper die and the pressure die, which help guide and stabilize the material during bending.
To bend the tube, mechanical force is applied to push the pipe or tubing against the die, shaping it to match the die’s contour. In most cases, the tubing is held firmly in place while one end is rotated and rolled around the die. In other methods, rollers may be used to push the stock material through and form a simple curve.
For certain tube bending processes, a mandrel is inserted inside the tube to prevent it from collapsing during bending. The tube is held in tension by the wiper die, which ensures no creases form under stress. Wiper dies are typically made of softer materials such as aluminum or brass to prevent scratching or damaging the tube's surface.
The tooling used in tube bending machines is usually made of hardened steel or tool steel to ensure durability and long service life. However, when there’s a risk of scratching or gouging the workpiece, softer materials like aluminum or bronze may be used, particularly for parts that come in direct contact with the tube, such as the pressure die and the wiper die. These materials help preserve the surface finish of the tube as it slides by.
Tube bending machines can be powered in several ways, including manual operation, pneumatic power, hydraulic assistance, hydraulic drive, or electric servomotors, depending on the machine's design and intended application.
Press Bending
Press bending is one of the earliest methods used for cold bending pipes and tubing. In this process, a die shaped to the desired bend is pressed against the pipe, causing the pipe to conform to the die’s contour. Since the pipe is not supported internally during the process, some deformation occurs, typically resulting in an oval-shaped cross section. As a result, press bending is most suitable for applications where maintaining a consistent cross-sectional shape is not critical.
While a single die can be used to create different shapes, it is limited to bending tubes of one specific size and radius at a time. This process is commonly employed when flexibility in shape is more important than maintaining uniformity in the pipe’s cross-section.
Rotary Draw Bending
Rotary draw bending (RDB) is a highly precise bending method that uses specialized tooling or "die sets" with a constant centerline radius (CLR), also known as the mean bending radius (Rm). One of the key features of rotary draw benders is their ability to be programmed to store multiple bending jobs with varying degrees of complexity. Often, these machines are equipped with a positioning index table (IDX), allowing operators to replicate complex bends with multiple angles and planes accurately.
Rotary draw benders are widely used for bending tubes, pipes, and solid materials in applications such as handrails, frames, roll cages for vehicles, handles, piping systems, and much more. They are known for producing smooth, aesthetically pleasing bends when the correct tooling is used for the specific application. CNC rotary draw bending machines, which are often more sophisticated, can handle severe bends while maintaining high-quality standards.
Full tooling is typically required for high-precision bending, especially for challenging materials with a high diameter-to-thickness (OD/t) ratio and a small ratio between the mean bending radius (Rm) and the outer diameter (OD). To prevent issues like thinning or collapsing of the tube during bending, axial boosting—applied either at the tube’s free end or on the pressure die—is often used. Additionally, mandrels (sometimes with spherical links or balls) are employed to prevent wrinkling and ovalization of the tube.
For less complex bending tasks (when the bending difficulty factor, or BF, is low), the tooling can be simplified, and certain aids such as axial assistance, mandrels, or wiper dies may be unnecessary. In some cases, standard tooling may need to be customized to meet the specific requirements of the products being bent.
Roll Bending
Roll bending is a process in which a pipe, extrusion, or solid material is passed through a series of rollers—usually three—that gradually apply pressure to shape the material into a bend. In pyramid-style roll benders, one roll (typically the top roll) moves, while in double-pinch roll benders, two adjustable rolls (usually the bottom rolls) are used, with a fixed top roll.
One of the key advantages of roll bending is that it causes minimal deformation to the pipe’s cross-section, ensuring the integrity of the material is largely maintained. This method is ideal for producing coils of pipe or creating long, smooth bends, such as those used in truss systems or other structural applications where gradual curves are required.
What are key terminologies in tube bending?
Understanding the geometry of a bend is crucial before choosing the appropriate die for tube bending. The following terms are commonly used in the tube bending process:
Center-Line Radius (CLR). The center-line radius is the measurement from the center of the curvature to the centerline (axis) of the tube. This radius may match the die radius based on how the die interacts with the tube. For tubes with identical radial dimensions and materials, a larger CLR results in a longer curvature. CLR is commonly known as the bend radius.
Outside Diameter. For hollow tubes, the outside diameter is the measurement between two points on the outer edges of the tube's cross-section, extending through the centerline.
Inside Diameter. The inside diameter refers to the measurement between the inner edges of a tube's cross-section, extending through the centerline. It represents the size of the tube’s internal opening.
Wall Thickness. Wall thickness is determined by subtracting the inside diameter from the outside diameter of a tube. It represents the thickness of the tube's material and is typically measured with calipers for accuracy. When selecting a die for tube bending, the outside diameter and wall thickness are crucial factors to consider.
Degree of Bend. The degree of bend refers to the angle created when the tube is bent, measured in degrees. It indicates the "sharpness" of the bend: tubes with smaller bend angles exhibit sharper curves. The angle complementary to the degree of bend is known as the bend angle.
Difference Between Tubes and Pipes
Although tubes and pipes may seem similar and can be bent using comparable techniques, they actually represent distinct components. The term "tube" is broadly used to describe hollow shapes in round, square, rectangular, or oval forms, which are employed in mechanical and structural applications, as well as pressure equipment and instrumentation systems.
Pipes function as systems for transporting liquids, gases, and both cold and hot water. They are sized according to Nominal Pipe Size (NPS) and schedule numbers. NPS is a North American standard for specifying the diameters and wall thicknesses of pipes designed for various pressure and temperature conditions. The schedule number indicates the wall thickness of a pipe as a dimensionless value. In contrast, tube sizes are defined by their outside diameter, with wall thickness typically measured using Birmingham Wire Gauge (BWG) standards.
Common tube bending machine models and characteristics
Manual Tube Bending Machine:
Features: Easy to use, suitable for small batch production and simple bending needs.
Model: Manual tube bending machines usually do not have a unified model, and most of them are distinguished according to their bending capacity and applicable pipe diameter.
Electric Tube Bending Machine:
Features: It adopts electric drive, easy to operate, and is suitable for processing pipes with medium diameters and complex curved shapes.
Model: Common models include DHW-32, DHW-76, etc., where the number usually represents the diameter of the pipe with the maximum bending capacity.
Hydraulic tube bending machine:
Features: The hydraulic system is used to provide strong bending force, which is suitable for bending pipes with large diameters and complex shapes.
Model: Common models include GW-50, GW-89, etc., and the number usually represents the diameter of the pipe with the maximum bending capacity.
CNC Tube Bending Machine:
Features: It adopts computer numerical control system control to achieve high automation and precise control, and is suitable for pipe bending with complex shapes and high precision requirements.
Model: Common models include CNC38, CNC80, etc., where the numbers usually represent the diameter of the pipe with the maximum bending capacity.
Cold Formed Tube Bending Machine:
Features: Bending pipes at room temperature, suitable for pipes with high requirements on material hardness and performance, such as stainless steel, etc.
Model: Common models include CB-38, CB-90, etc., where the numbers usually represent the diameter of the pipe with the maximum bending capacity.
Hot bending tube bending machine:
Features: The pipe is bent by heating, which is suitable for pipes with high hardness and large diameter pipes.
Model: Common models include HB-50, HB-100, etc., where the number usually represents the diameter of the pipe with the maximum bending capacity.
Application field of tube bending machine
Tube Bending Machine Applications in Manufacturing
Aerospace: In the field of aerospace, it is necessary to manufacture pipes of various complex shapes, such as hydraulic system pipes, gas system pipes, etc. tube bending machines can achieve precise bending of these pipes, ensuring their safety and reliability in flight.
Automobile manufacturing: In the process of automobile manufacturing, a large number of pipelines are required for fuel systems, braking systems, cooling systems, etc. Tube bending machines play an important role in automotive manufacturing, capable of producing precision tubes that meet automotive design requirements.
Oil and gas industry: The oil and gas industry requires a large number of pipelines for transporting oil, gas and liquids. tube bending machines are able to precisely bend these pipes to accommodate complex pipe layouts and terrain conditions.
Power industry: In power plants and power equipment manufacturing, a large number of pipes are required to transport media such as cooling water and steam. The tube bending machine can meet the processing needs of pipes of different sizes and shapes.
Architectural and structural engineering: In the field of construction, it is often necessary to use curved pipes to meet the needs of complex building structures, such as bridges, high-rise buildings and industrial facilities. tube bending machines are able to provide customized pipe processing solutions for these construction projects.
Pipe bender applications in the construction industry
Water supply and drainage system: The water supply and drainage system of a building involves a large number of pipes, including water supply pipes, drainage pipes, sewage pipes, etc. These pipes need to be bent according to the building structure and design requirements to accommodate complex layouts and building shapes. tube bending machines are able to precisely bend these pipes to ensure the proper functioning of water supply and drainage systems.
HVAC systems: HVAC systems need to use a large number of pipes to transport hot and cold media, such as air-conditioning water pipes, cooling water pipes, etc. These pipes need to be bent according to the building structure and air conditioning layout to meet the heating and cooling needs of different rooms and areas. tube bending machines are able to provide custom bending of these pipes to ensure efficient operation of air conditioning systems.
Building structure: In some special building structures, it is necessary to use curved pipes to meet complex building shapes and design requirements, such as curved ceilings, curved stairs, etc. The tube bending machine can provide customized pipe processing solutions for these building structures, making the architectural form more unique and beautiful.
Firefighting system: The firefighting system of a building needs to use a large number of pipes for fire emergency rescue, such as fire hose pipes, sprinkler system pipes, etc. These pipes need to be bent according to the layout of the building and fire protection needs to ensure the efficient operation of the fire protection system. The tube bending machine can provide accurate pipe processing for the fire protection system to ensure fire safety.
Pipe bender applications in the automotive industry
Fuel system: The fuel system of a car includes fuel supply pipes, fuel tank pipes, etc. These pipes need to be bent precisely according to the structure and design requirements of the car to ensure the supply and transmission of fuel. The tube bending machine can provide high-precision bending processing for these pipes to ensure the stable and safe operation of the fuel system.
Brake system: The brake system of a car requires a large number of brake pipes for the transmission of brake fluid. These pipes need to withstand high pressure and high temperature during vehicle braking, so the requirements for the bending quality of the pipes are relatively high. The tube bending machine can meet the high-precision processing requirements of the brake pipe and ensure the reliability and sensitivity of the brake system.
Cooling system: The cooling system of a car includes radiator pipes, coolant pipes, etc. These pipes need to be bent precisely according to the layout of the engine and radiator to ensure the circulation of coolant and the effect of heat dissipation. The tube bending machine can provide customized pipe processing solutions for the cooling system to ensure the efficient operation of the cooling system.
Exhaust system: The exhaust system of a car includes exhaust pipes and tailpipes. These pipes need to be properly bent in accordance with vehicle emission standards to reduce tailpipe emissions and improve vehicle emission performance. The tube bending machine can meet the precise processing requirements of the exhaust system and ensure the environmental protection performance of the car.
How to Choose A Tube Bendng Machine in 2025
If you belong to the metalworking industry then you may know the importance of buying the right equipment. The final result in any metalworking project depends on the quality and the type of equipment used. So, if you wish to buy a tube bender, it takes consideration of multiple factors. Let’s discuss the factors that would help you select right tube bender.
- Know the Types of Tube Blenders: Generally, tube benders are categorized according to their operational mechanism. Let’s discuss a few fundamental types of bending machines.
- Open Rotary Draw Benders: This type of bender bends the tube by drawing it in a curvature. It uses die sets of specific radius and is suitable for metal tube bending.
- Mandrel Benders: A mandrel bending machine uses a series of steel balls called ball mandrel. The series of balls is passed through the tube while being supported by a curved radius to bend the tube. This machine is used for mass tube bending operations.
- Roll Benders: These benders feature a pyramid structure with three rollers situated in a triangular fashion. The tube is rolled on the rollers to bend in a specific diameter.
- Ram-Style Benders: In this type of bender, a die is pushed inside a tube with the help of ram in order to bend the tube in a specific shape. The ram can be powered by hydraulic or pneumatic or manual force.
Along with these main types of benders, there are few types of benders that are named on the basis of their power sources. These types are namely, hydraulic tube benders, pneumatic tube benders, manual benders, electric benders, and NC/CNC electromechanical benders. The function of each bender is associated with the type of actuator and similarly, the efficiencies vary. To select right tube bender, you need to consider the types and select according to your requirements.
- Analyze Your Operational Requirements: When it comes to selecting the best tube bender to suit your needs, you must analyze your requirements. The following factors are important to consider under your operational requirements.
- Speed of operation: If high-speed tube bending operation is required then manual bender may not be a suitable choice. Generally, electrical actuators and pneumatic actuators work excellent for high-speed operations. Therefore, electrical or pneumatic benders will be a choice of high-speed blending. In case of low speed or heavy-duty bending, hydraulic benders are suitable since hydraulic actuators respond well for high load applications.
- Size of Production Batch: The batch size of production should be considered while choosing right tube bender. For batch bending, mandrel bending or CNC bending is preferred.
- Cost and Demand of Operation: The budget and demand are two important factors of selection. One should only invest more if the demand is more. For high demand, the operator shall invest in efficient CNC bender or electric blenders. If the bending operations are rare then the operator can go for the less expensive manual bending machine.
- Match the Machine and Material: The bender must be compatible with the material used. You must consider the tube material, wall thickness, tube diameter, etc. According to these considerations, a suitable tube bender must be selected.
- Explore Tools and Accessories: The tube benders come along with a set of dies and bending tools. During the selection of the benders, you must look for accessories like pipe and tube bending tool kit, rolling machines, multi-purpose tube benders, etc.
- Application Requirements: This can be a little challenging question to address as there are several requirements to be considered. Perhaps, one can focus on the following questions:
- Type of material to be bended
- Maximum and minimum tube size to be achieved
- Part shapes to be achieved
- Dimensions of the tube to be bended
- Wall thickness of the tube to be produced
- Center Line Radius (CLR) of the desired bend
- Volume Consideration: This will depend on the type of bending projects that one undertakes. Some of the main considerations would be:
- Number of parts to be bended in an hour
- Number of hours the machine would be operated
- Number of times it would be operated in a day or month
- Number of times the tooling is changed
- Budget: Perhaps, this is the base of every commercial and industrial investment made and a pipe or tube bender would be no different. Although most metalworking facility owners only concentrate on high value at low investment, that is not enough. At times, a type of tube bending machine may be charged across different brands; so, you must compare the benefits and ROI that they offer.
- Quality: A tube bending equipment is a one-time investment, and you cannot afford to make a wrong decision. The quality of bends would depend on the quality of the machine used.
Along with all the mentioned factors, it is important to seek the experts’ advice while selecting right tube bending machines. Krrass from China is a company that has a team of experts to help you with this selection. This company has been actively supplying tube and pipe fabrication equipment like benders since 1995. Their experience and product quality prove their expertise.
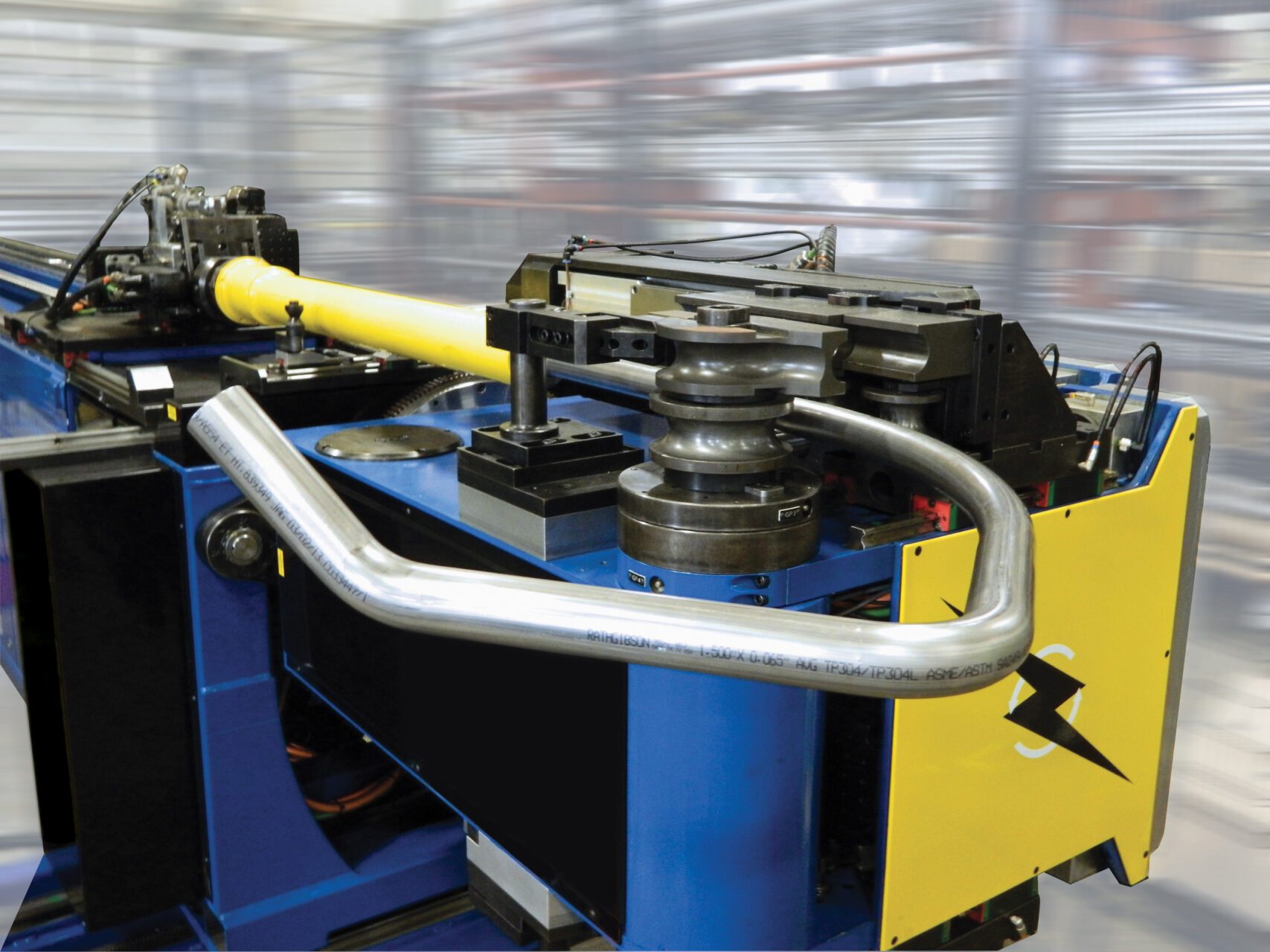
Reviewed by 1 user
The interface is user-friendly, making it accessible even for operators with limited experience,Great pipe bender