Over the years, the metalworking industry has made remarkable progress. However, traditional methods still bring many challenges that impede work efficiency and precision. The introduction of tube laser cutting machines has effectively solved many persistent problems and revolutionized the industry. Below, we will explore 10 common problems in the traditional metalworking field that tube laser cutting machines have successfully addressed.
1. Precision and Accuracy
Traditional metal cutting methods, such as sawing and mechanical cutting, often struggle to achieve the high precision required for complex designs. In contrast, tube laser cutting machines utilize advanced laser technology to achieve unparalleled precision and can produce complex shapes with minimal deviation. This ensures that each cut is precise and consistent.
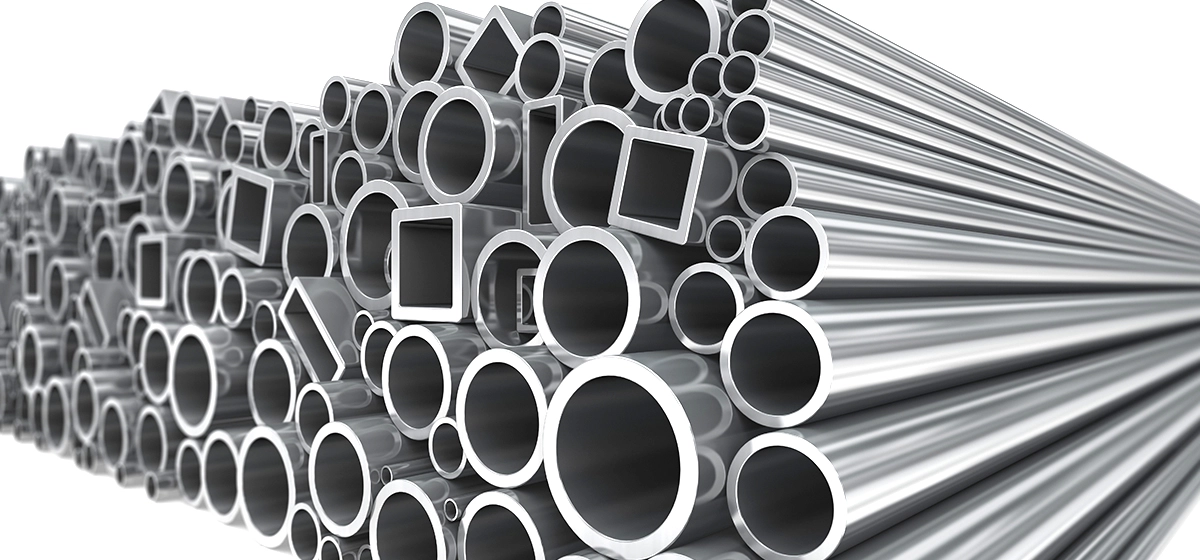
2. Material Waste
Traditional cutting techniques often result in significant material waste due to the need for multiple passes and the inability to optimize cutting effectively. However, tube laser cutting machines can achieve more automated nesting of spare parts and minimize the need for secondary processing, thereby minimizing material waste. This ultimately leads to cost savings and improved resource utilization.
3. Cutting Speed and Efficiency
Traditional cutting methods can be time-consuming, especially when dealing with complex designs or thicker tubes. However, tube laser cutting machines work much faster, greatly shortening production time. The combination of speed and precision enables faster manufacturing turnaround times and higher productivity.
4. Design Flexibility
One of the main limitations of traditional metal tube processing equipment is the lack of flexibility in design changes or customization. In contrast, tube laser cutting machines offer unparalleled flexibility, allowing for easy modification and adjustment without the need for additional tools or setup. This flexibility is particularly beneficial in industries that require customization or small-batch production.
5. Complex Shapes
Producing complex shapes using traditional cutting methods is often a challenge as it requires multiple tools and setups, which increase production time and cost. Tube laser cutting machines can effortlessly handle complex shapes and contours, making it easy to create intricate designs.
6. No Need for Post-Processing
To achieve the desired quality, traditional cutting techniques usually require extensive post-processing, such as deburring or grinding. Tube laser cutting machines produce clean, smooth edges and generally do not require additional finishing work, saving time and labor costs.
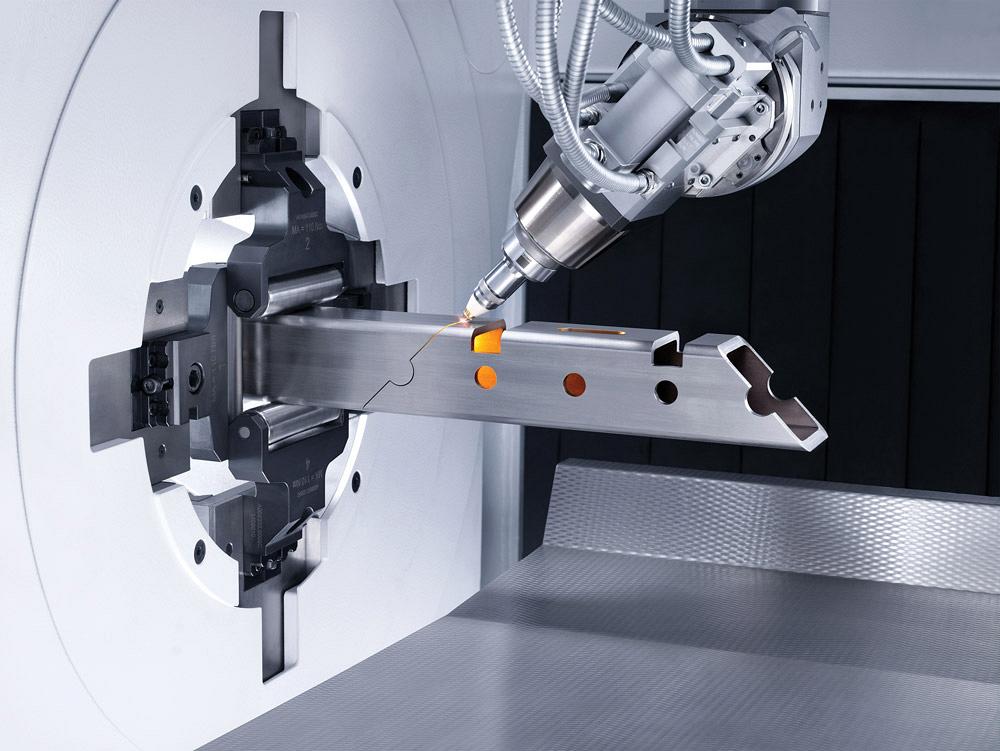
7. Minimal Tool Wear
Mechanical cutting methods rely heavily on physical tools, which may wear out over time, requiring maintenance and replacement costs. On the other hand, tube laser cutting machines use a non-contact pattern, which means minimal tool wear. This not only extends the machine's service life but also minimizes downtime and maintenance costs.
8. Material Versatility
Traditional metal tube processing equipment may struggle with different types of materials, especially when switching between metals of different thicknesses or compositions. Tube laser cutting machines are highly versatile and can cut a wide variety of materials, including low-carbon steel, stainless steel, aluminum, brass, and more. In terms of shape, they can easily handle round, square, rectangular, and elliptical tubes, as well as I-beams and H-beams. This versatility makes them ideal for manufacturers using diverse tubes.
9. Environmental Impact
Traditional cutting methods often lead to a large amount of waste and emissions, affecting the surrounding environment. Tube laser cutting machines are more environmentally friendly as they produce less waste and require less energy.
10. Cost-Effectiveness
Although the initial investment in tube laser cutting machines may be higher than that of traditional equipment, the long-term benefits are considerable. Reduced material waste, maintenance costs, and production time, combined with improved precision and versatility, can result in significant savings over time. For many users, this cost-effectiveness makes tube laser cutting machines an attractive option for cutting metal tubes.
Conclusion
Tube laser cutting machines have evolved into a powerful solution to many challenges that traditional metalworking has difficulty dealing with. Their performance in terms of precision, waste reduction, cutting speed, and design flexibility makes them an essential tool in modern manufacturing. By solving these 10 key problems, tube laser cutting technology is paving the way for more efficient, cost-effective, and environmentally friendly metalworking solutions.