Imagine cutting through metal tubes with the precision of a laser, effortlessly shaping complex and intricate designs. This article breaks down the critical relationship between material thickness and cutting speed in tube laser cutting, providing an essential reference chart to perfect your cutting settings. Whether you’re a seasoned professional or an enthusiastic newcomer, understanding these dynamics can significantly enhance your cutting results. Dive into this guide to discover how you can achieve faster, cleaner cuts while maximizing the full potential of your laser cutting machine.
Tube laser cutting has transformed the metal fabrication industry, offering unmatched precision and efficiency in producing complex designs. This advanced technology uses high-powered lasers to cut through a wide range of materials, including metals, plastics, and ceramics. For both professionals and hobbyists, understanding the connection between cutting thickness and speed is essential to unlocking the full potential of tube laser cutting technology. With the right knowledge, you can enhance your cutting efficiency and achieve superior results.
Table of Contents
Understanding Tube Laser Cutting
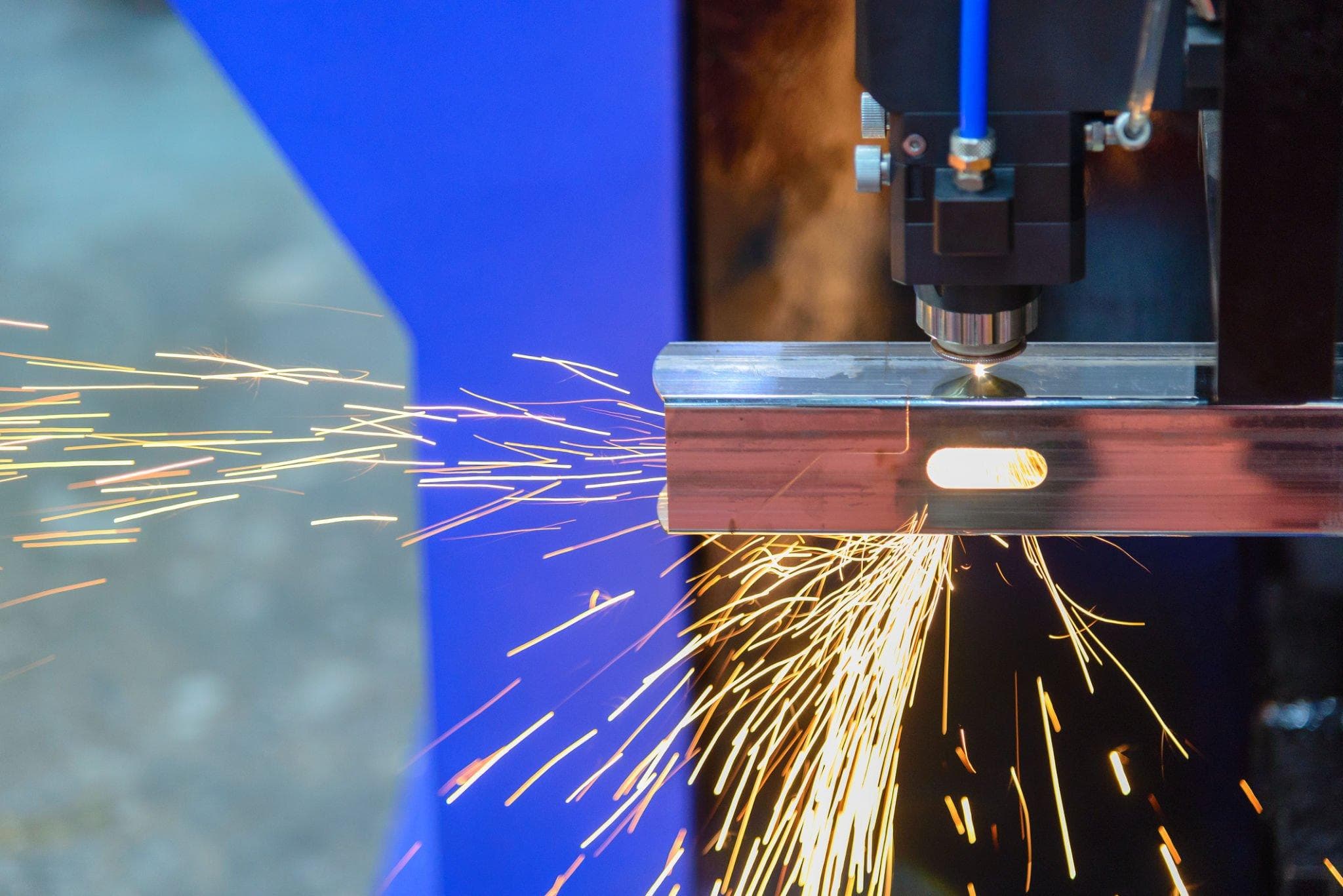
Tube laser cutting is a high-precision manufacturing process that uses lasers to cut various shapes and features into metal tubes. The process involves directing a high-powered laser beam—typically a fiber laser or CO2 laser—toward the material being cut. The exceptional accuracy and precision of the laser beam make it ideal for creating small, intricate cuts, even in the most complex geometries.
Among the two primary types of lasers used for tube laser cutting, fiber lasers and CO2 lasers stand out. Fiber lasers generate light by pumping energy into a doped optical fiber, offering excellent beam quality, precision, and high processing speeds. CO2 lasers, on the other hand, use a mixture of carbon dioxide, helium, and nitrogen to generate light. While CO2 lasers offer a larger heat-affected zone, which can cause discoloration or warping in some materials, they stay a versatile choice for various cutting applications.
The efficiency of the laser cutting process is also influenced by the power of the laser cutting machine. A more powerful laser enables faster processing and can cut through thicker materials. Laser cutting machines come in a variety of power levels, ranging from low-powered diode lasers for thin materials to high-powered industrial lasers capable of cutting thick and dense materials.
In tube laser cutting, understanding the factors that influence cutting speed and material thickness is vital for producing efficient and high-quality products. These factors include:
- Laser Power: Higher laser power allows for cutting thicker materials at faster speeds, significantly improving the overall efficiency of the cutting process.
- Material Type: Different metals, such as steel, aluminum, and copper, show varying properties that can affect cutting speed and overall efficiency.
- Beam Quality: The quality of the laser beam plays a crucial role in cutting speed and accuracy. A well-focused and stable beam ensures faster, cleaner cuts, reducing errors and waste.
A Tube Laser Cutting Thickness & Speed Chart provides invaluable information for manufacturers in selecting the best machine settings for different material thicknesses. This chart typically presents a detailed table, outlining the cutting speeds and maximum material thicknesses compatible with specific laser models, power ratings, and laser types. Using this chart helps ensure high performance while keeping cost-effectiveness and efficiency in the cutting process.
Tube Laser Cutting Thickness & Speed Chart
The following table presents cutting speeds for various materials at different thickness levels and laser power ratings, offering an essential guide for maximizing laser cutting performance:
Material | Thickness (mm) | 1000W | 1500W | 2000W | 3000W | 4000W | 6000W |
---|---|---|---|---|---|---|---|
(m/min) | (m/min) | (m/min) | (m/min) | (m/min) | (m/min) | ||
Carbon Steel Air | 1 | 12.0-15.0 | 15.0-20.0 | 25.0-30.0 | 28.0-35.0 | 30.0-38.0 | 35.0-42.0 |
2 | 3.5-4.5 | 5.0-8.0 | 7.0-10.0 | 8.0-12.0 | 10.0-16.0 | 20.0-28.0 | |
3 | 1.5-3.0 | 2.0-4.0 | 2.5-4.5 | 3.0-5.0 | 8.0-15.0 | ||
4 | 1.5-2.3 | 2.5-3.5 | 7.0-12.0 | ||||
5 | 1.0-2.2 | 5.0-9.0 | |||||
6 | 3.0-6.0 | ||||||
Carbon Steel O2 | 1 | 15.0-22.0 | 18.0-25.0 | 22.0-30.0 | 25.0-38.0 | 30.0-44.0 | 35.0-48.0 |
2 | 3.5-5.0 | 3.8-5.0 | 5.0-6.0 | 5.5-7.0 | 5.5-7.7 | 6.0-8.25 | |
3 | 2.5-3.85 | 2.8-3.8 | 3.5-4.3 | 3.6-5.0 | 3.7-5.5 | 4.0-5.5 | |
4 | 2.0-3.3 | 2.3-3.5 | 2.8-4.0 | 3.0-4.5 | 3.5-4.62 | 3.5-5.0 | |
5 | 1.4-2.0 | 1.6-2.5 | 2.5-3.0 | 2.5-3.3 | 2.5-4.0 | 3.0-4.2 | |
6 | 1.2-1.65 | 1.4-1.8 | 2.2-2.5 | 2.3-2.8 | 2.5-3.52 | 2.6-3.52 | |
8 | 0.9-1.32 | 0.9-1.3 | 1.3-1.8 | 1.8-2.2 | 2.0-2.8 | 2.0-2.8 | |
10 | 0.6-0.9 | 0.8-1.2 | 1.2-1.5 | 1.2-1.6 | 1.2-2.2 | 1.8-2.3 | |
12 | 0.4-0.7 | 0.7-1.0 | 0.8-1.0 | 1.0-1.3 | 1.0-1.76 | 1.6-2.1 | |
16 | 0.5-0.7 | 0.6-0.8 | 0.6-0.9 | 0.7-1.0 | 0.7-1.0 | ||
20 | 0.5-0.8 | 0.6-0.9 | 0.65-0.95 | ||||
22 | 0.66-0.9 | 0.6-0.77 | |||||
25 | 0.4-0.65 | ||||||
Stainless Steel N2 | 1 | 16.5-22.0 | 20.0-26.0 | 27.5-33.0 | 31.0-38.5 | 33.0-45.0 | 50.0-65.0 |
2 | 4.5-6.1 | 7.0-10.0 | 9.0-11.0 | 10.0-16.5 | 10.0-20.0 | 30.0-40.0 | |
3 | 2.0-3.1 | 4.5-5.5 | 4.5-5.5 | 7.0-10 | 7.5-12.0 | 18.0-25.0 | |
4 | 1.0-1.65 | 2.0-2.5 | 2.2-2.8 | 5.0-7.2 | 5.5-9.0 | 10.0-15.5 | |
5 | 0.4-0.7 | 1.5-2.0 | 1.5-2.0 | 1.8-2.45 | 4.0-5.5 | 8.0-13.5 | |
6 | 0.2-0.45 | 0.6-0.9 | 0.7-1.32 | 1.0-1.65 | 2.6-4.5 | 6.0-9.0 | |
8 | 0.2-0.45 | 0.35-0.6 | 1.2-2.0 | 1.6-2.8 | 4.0-5.5 | ||
10 | 0.7-1.0 | 0.7-1.65 | 1.8-2.8 | ||||
12 | 0.5-0.9 | 1.2-1.65 | |||||
14 | 0.8-1.2 | ||||||
16 | 0.6-0.9 | ||||||
Aluminum N2 | 1 | 10.0-13.2 | 15.0-27.5 | 22.0-31.0 | 25.0-30.0 | 28.0-32.0 | 35.0-45.0 |
2 | 2.0-4.5 | 7.0-8.6 | 10.0-13.2 | 15.0-18.0 | 16.0-20.0 | 20.0-25.0 | |
3 | 0.6-1.32 | 2.5-4.0 | 5.0-6.6 | 7.0-8.0 | 10.0-12.0 | 14.0-16.0 | |
4 | 1.0-1.65 | 1.5-2.2 | 5.0-6.0 | 6.0-7.0 | 8.0-10.0 | ||
5 | 0.6-0.9 | 1.0-1.3 | 2.5-3.0 | 4.0-5.0 | 5.0-7.0 | ||
6 | 0.4-0.7 | 0.6-0.9 | 1.5-2.0 | 2.5-3.0 | 3.5-4.0 | ||
8 | 0.4-0.7 | 0.5-0.8 | 1.0-1.3 | 1.5-2.0 | |||
10 | 0.3-0.4 | 0.8-1.0 | 1.0-1.2 | ||||
12 | 0.6-0.8 | 0.6-0.7 | |||||
14 | 0.3-0.5 | 0.4-0.6 | |||||
16 | 0.3-0.4 | ||||||
Brass N2 | 1 | 14.0-20.0 | 15.0-22.0 | 20.0-27.0 | 20.0-28.0 | 25.0-30.0 | 30.0-40.0 |
2 | 3.0-4.5 | 4.0-7.2 | 7.7-8.8 | 7.0-13.2 | 12.0-15.0 | 15.0-18.0 | |
3 | 1.0-1.55 | 1.1-1.5 | 3.0-4.5 | 5.0-7.2 | 5.5-7.7 | 12.0-14.0 | |
4 | 1.0-1.2 | 1.3-1.8 | 2.5-3.0 | 3.5-5.5 | 8.0-10.0 | ||
5 | 0.6-0.9 | 0.8-0.9 | 1.6-2.0 | 2.0-3.5 | 5.0-5.5 | ||
6 | 0.4-0.6 | 0.8-1.2 | 1.4-2.2 | 3.2-3.8 | |||
8 | 0.3-0.4 | 0.8-1.0 | 1.5-1.8 | ||||
10 | 0.4-0.6 | 0.8-1.0 | |||||
12 | 0.6-0.7 |
Factors Influencing Cutting Parameters
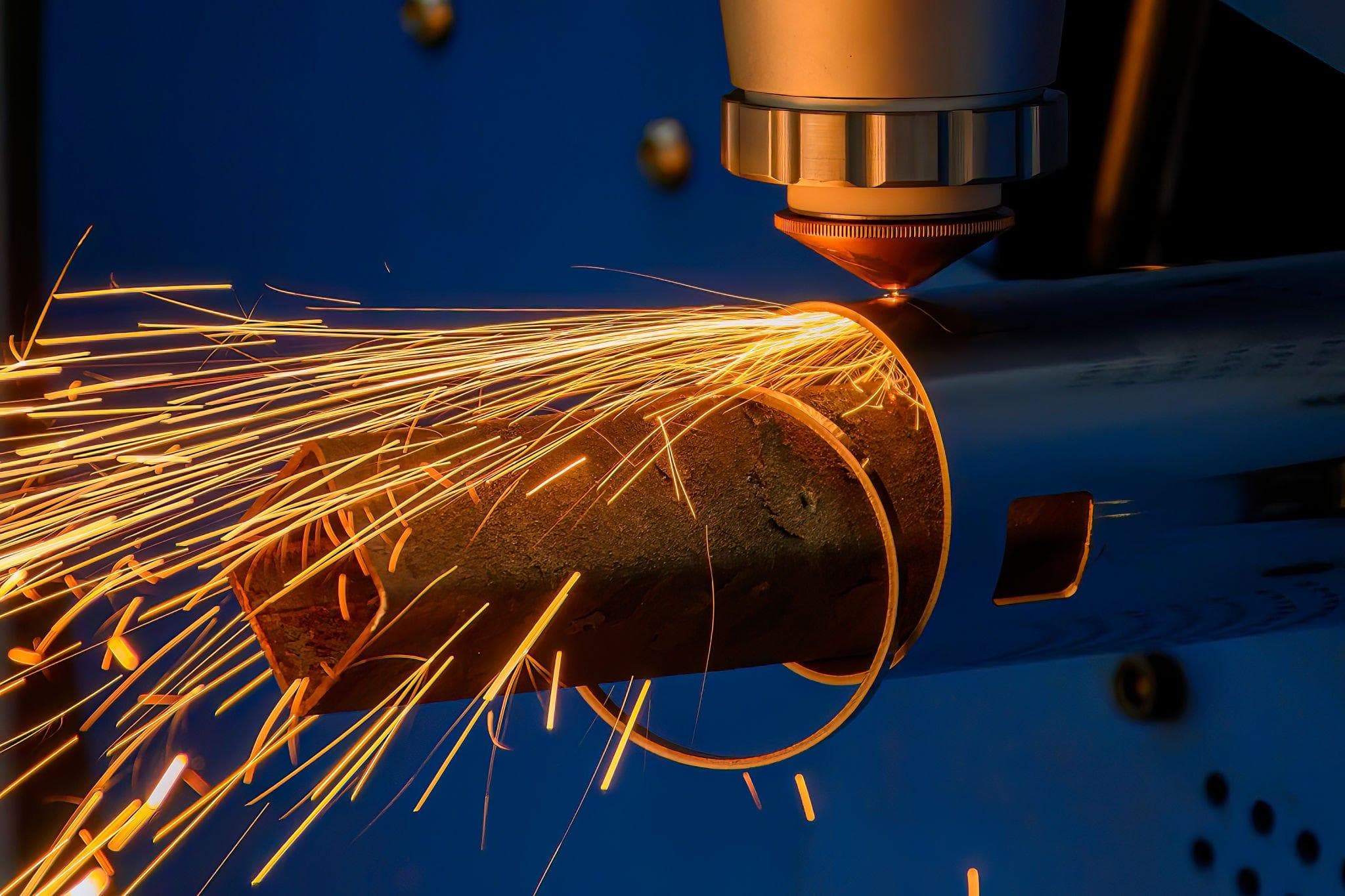
- Power and Energy: Laser power and energy density directly correlate with the wattage of the laser system used. A higher wattage laser generates more heat, enabling faster cutting speeds. The nozzle also plays a crucial role in perfecting the power and energy density of the beam, so selecting the right nozzle size is essential to ensure a smooth cutting process.
- Focus and Spot Size: Adjusting the laser focus and spot size on the cutting material is another key factor. Smaller spot sizes result in higher energy densities, which allow for more precise cuts. Larger spot sizes can help achieve faster cutting speeds but might not offer the same level of detail and precision.
- Assist Gas and Pressure: The type of assist gas (such as oxygen, nitrogen, or compressed air) and its pressure directly influence the cutting process. Oxygen accelerates the cutting speed but may compromise cut quality due to excess heat, while nitrogen minimizes heat-affected zones and results in cleaner cuts. Choosing the right gas and adjusting the pressure optimally is essential for high-quality and efficient cutting.
By understanding these key factors and using the Tube Laser Cutting Thickness & Speed Chart, manufacturers can perfect their cutting processes, achieve superior results, and enhance operational efficiency. This knowledge not only ensures quality and precision but also plays a vital role in minimizing waste, improving overall productivity, and achieving cost-effective results.
Leveraging the right settings for your specific project is critical for maximizing the potential of your tube laser cutting machine, whether it’s a low-powered model or a high-powered industrial system. Perfect your cutting process and watch your productivity soar.