Hydraulic shearing machines, particularly the types of hydraulic shears, are essential tools in the manufacturing and metalworking industries. These machines play a crucial role in cutting and shaping metal sheets with exceptional precision and efficiency. Widely adopted across various sectors such as automotive, aerospace, construction, and shipbuilding, hydraulic shears are integral where both precision and productivity are paramount. In this article, we will explore the different types of hydraulic shears, their applications, and the significant benefits they bring to the manufacturing process.
Understanding Hydraulic Shearing Machines
Hydraulic shearing machines use hydraulic power to generate the immense force needed to cut through metal sheets. These machines are renowned for their accuracy, reliability, and versatility in cutting materials like stainless steel, aluminum, and carbon steel, ensuring clean and precise cuts in various thicknesses.
The core mechanism behind hydraulic shearing is relatively straightforward. A hydraulic system generates high pressure, which is transmitted to the cutting blade. The pressure forces the blade to move rapidly, slicing through the material placed between the upper and lower blades. This technology enables the creation of smooth, straight cuts without causing excessive heat or deformation, making it ideal for industries requiring high-quality standards in their manufacturing processes.
Types of Hydraulic Shears
Hydraulic shearing machines are available in several configurations, each perfected for different cutting needs and material types. Below, we delve into the most common types of hydraulic shearing machines used in the industry:
1. Fixed Rake Angle Shears
Fixed rake angle shears feature a constant angle between the blades, which defines the cutting angle and clearance. These machines are well-suited for cutting thicker materials and are known for their robust construction and high cutting ability. They are particularly effective for heavy-duty applications requiring consistent results over extended periods.
2. Variable Rake Angle Shears
Unlike fixed rake angle shears, variable rake angle shears offer flexibility by allowing operators to adjust the rake angle based on the material being cut. This adaptability makes these machines ideal for managing a wide range of material types and thicknesses, offering greater versatility in the cutting process.
3. NC (Numerical Control) Hydraulic Shears
Numerical control (NC) hydraulic shears are equipped with a control system that allows for precise, programmable cutting operations. The operator can input specific cutting parameters, such as dimensions and angles, making these machines perfect for tasks that require an elevated level of consistency and accuracy. NC shears are commonly used for repetitive and complex cutting operations in industrial environments.
4. CNC (Computer Numerical Control) Hydraulic Shears
CNC hydraulic shears take automation and precision to the next level. By integrating advanced computer systems, CNC shears can execute intricate cutting patterns with unrivaled accuracy and speed. These machines are especially suited for high-volume production runs, allowing manufacturers to produce copious quantities of components with exact specifications. The integration of computer technology enhances both the versatility and efficiency of the cutting process.
5. Swing Beam Shears
Swing beam shears feature an upper beam that swings horizontally to apply force to the material, delivering efficient cutting for thinner to medium-thick sheets. These machines are known for their ease of operation, making them a popular choice in environments where simplicity and reliability are key. They strike a perfect balance between performance and user-friendliness.
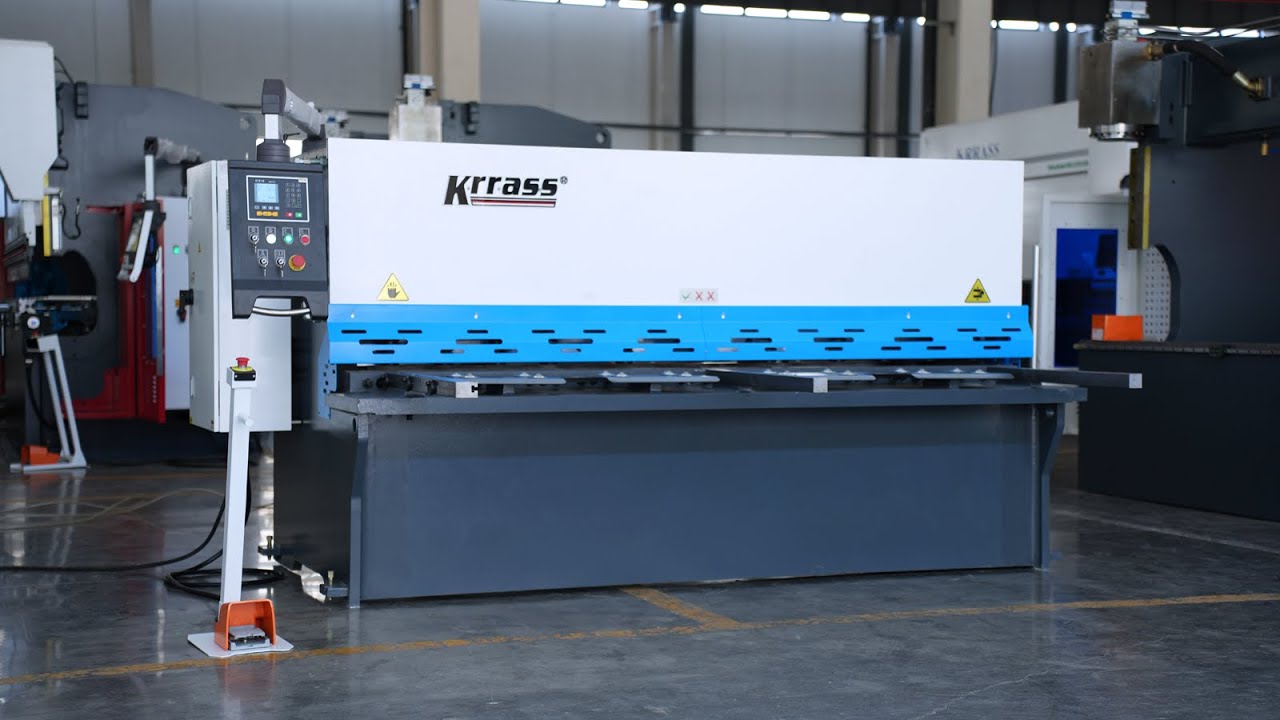
6. Guillotine Shears
Guillotine shears have a straightforward design that incorporates a vertical movement of the upper blade. These machines can cut through thick, heavy materials with ease, thanks to their robust frame and powerful cutting force. Guillotine shears are particularly effective in heavy-duty applications where high strength and durability are needed.
7. Hydraulic Guillotine Shears
Hydraulic guillotine shears combine the reliability of traditional guillotine technology with the precision and efficiency of hydraulic systems. This combination offers a smooth and consistent cutting motion, enabling the machine to manage a wide variety of materials with minimal distortion. Hydraulic guillotines are widely used for applications that demand both power and finesse.
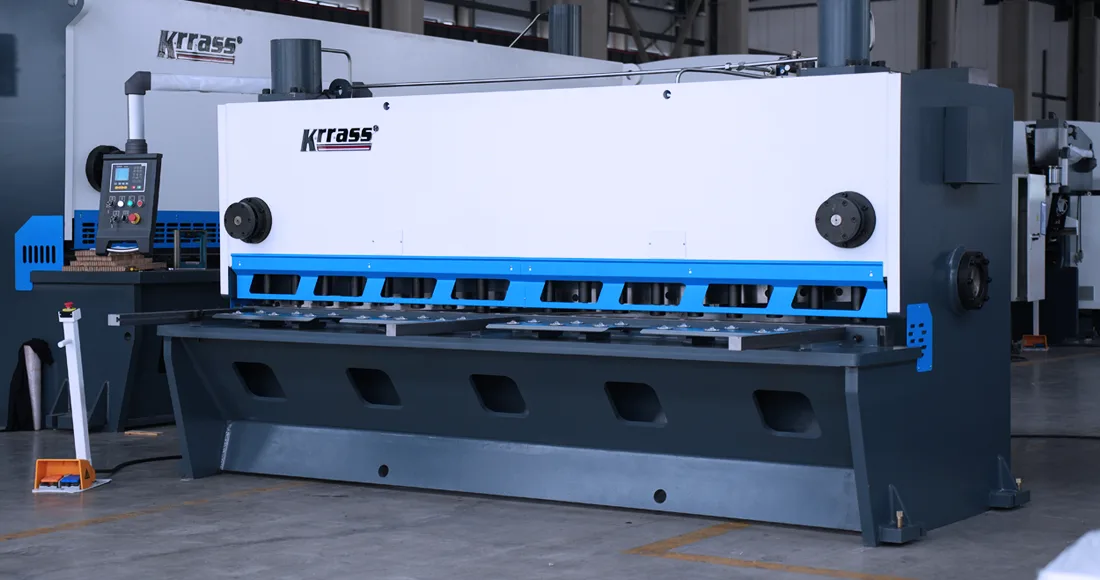
8. Tandem Hydraulic Shears
Tandem hydraulic shears consist of multiple shearing units running in tandem, which makes them ideal for cutting exceptionally long sheets or for high-volume production environments. The synchronized operation of multiple units allows for continuous and efficient processing of long metal sheets, making these machines indispensable in industries with high throughput requirements.
Applications of Hydraulic Shearing Machines
Hydraulic shearing machines are indispensable tools in a wide array of industries. Their ability to deliver precise and efficient cuts makes them a cornerstone of modern manufacturing. Below are some of the primary sectors where hydraulic shearing machines are extensively used:
Metal Fabrication
In metal fabrication, hydraulic shearing machines are essential for cutting metal sheets and plates, which are then used to create various components such as machinery parts, structural elements, and more. Their ability to produce correct cuts plays a crucial role in ensuring high-quality finished products.
Automotive Industry
The automotive industry relies on hydraulic shearing machines to cut metal parts for vehicles such as cars, trucks, and buses. These machines ensure that parts are cut with precision, allowing for efficient mass production while keeping lofty standards of quality and consistency.
Aerospace Industry
The aerospace sector depends on hydraulic shearing machines to cut and shape metal components for planes and spacecraft. Due to the demanding nature of aerospace manufacturing, these machines must offer superior precision and the ability to manage high-strength materials, both of which hydraulic shears excel at.
Construction
In the construction industry, hydraulic shearing machines are used to cut steel and other materials, which are then fabricated into structural elements such as beams, columns, and trusses. Their reliability and precision are vital for ensuring the safety and stability of building structures.
Shipbuilding
Shipbuilding companies use hydraulic shearing machines to process large metal plates for constructing ships and boats. These machines help to ensure that the parts fit together with exacting precision, which is critical in the marine industry for structural integrity.
Electronics and Electrical Appliances
Hydraulic shearing machines are also employed to cut metal components for electronic devices and electrical appliances. This includes the creation of casings and internal parts that require fine-tuned cutting accuracy for functional and aesthetic purposes.
Benefits of Hydraulic Shearing Machines
Hydraulic shearing machines offer several benefits that make them the preferred choice for a wide range of applications:
Precision
Hydraulic shearing machines deliver correct, clean cuts, minimizing material wastage and ensuring that the final products meet strict quality standards. Their high cutting precision contributes to the overall efficiency of the manufacturing process.
High Productivity
These machines can work at high speeds, which enhances productivity. With the ability to manage a wide variety of materials and thicknesses, hydraulic shearing machines increase the throughput of production lines, making them ideal for both low and high-volume manufacturing.
Versatility
Hydraulic shearing machines are available in several types, offering versatility for different applications and material requirements. Whether cutting thin sheets or thick plates, operators can select the machine best suited for their specific needs.
Ease of Use
Modern hydraulic shearing machines are equipped with intuitive controls, making them user-friendly and accessible to operators of all skill levels. This ease of use helps reduce training time and operational errors, further enhancing the efficiency of the manufacturing process.
Low Maintenance
Hydraulic systems are inherently durable and require minimal maintenance, reducing downtime and maintenance costs. This makes hydraulic shearing machines a cost-effective choice for businesses in need of reliable, long-lasting equipment.
Cost-Efficiency
By reducing material waste and improving cutting speed and accuracy, hydraulic shearing machines offer long-term cost savings. Their efficiency ensures that manufacturing processes are both economically practical and high-quality.
Conclusion
Hydraulic shearing machines are indispensable assets in the metalworking and manufacturing industries, providing unparalleled precision, efficiency, and versatility in cutting various materials. With multiple types of shearing machines to choose from, businesses can select the best machine for their specific requirements, whether it's for high-volume production, intricate designs, or heavy-duty applications. As technology advances, the role of hydraulic shearing machines in shaping the future of manufacturing and metal fabrication will only become more prominent, supporting industries across the globe in achieving higher standards of productivity and quality.