In today's fast-paced manufacturing world, the demand for precision, efficiency, and versatility is higher than ever. Enter the fiber laser cutting machine for metal—a revolutionary technology that is transforming metal fabrication industries across the globe.
This guide aims to provide an in-depth understanding of fiber laser cutting machines, highlighting their operation, benefits, applications, and how to choose the right machine for your needs. Whether you are a seasoned professional or new to the field, this comprehensive guide will equip you with the knowledge to harness the full potential of fiber laser cutting technology and stay ahead in the competitive landscape of metalworking.
Introduction To Fiber Laser Cutting Machine For Metal
Laser cutting has become a preferred technology in many industries due to its precision and accuracy. One of the latest advancements in this technology is the Fiber Laser Cutting Machine. Fiber cutting machines are highly efficient, and the laser beam can be focused on very small spot sizes, enabling it to cut intricate shapes with high precision.
What Is Laser Cutting
Laser cutting is a technique used to cut or engrave hard materials by burning, melting or vaporizing. The process has multiple industrial applications across various industries and can be used to drill holes or cut shapes in metal and other materials on a production line.
Laser cutting is also used as an artistic technique to engrave decorative designs on surfaces.The primary advantage of laser cutting technology is its accuracy, and the high power beam is concentrated through a laser cutting nozzle for pinpoint accuracy. Modern laser cutting generally uses CAD technology, allowing artists and engineers to create intricate designs with an industrial laser.
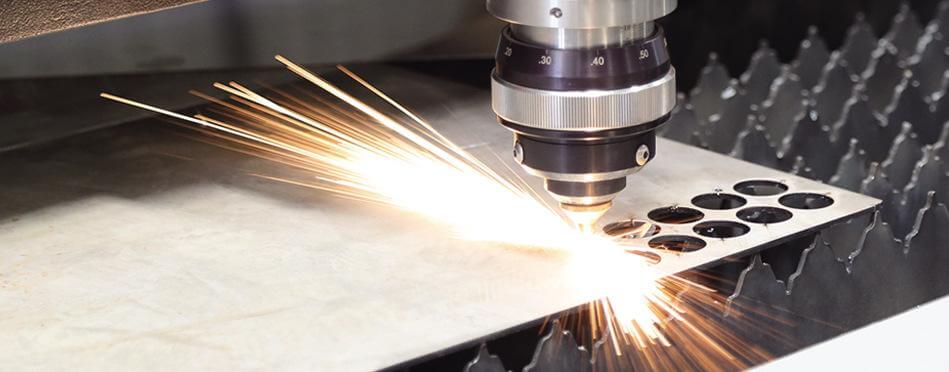
How Does Laser Cutting Work
A laser works by energizing the atoms in a solid, liquid or gas medium. This requires an energy pump, which could be an electrical current or even a second laser. As the atoms in the medium absorb energy, they start emitting light. This light is concentrated by placing a mirror at each end of the medium, creating an optical cavity.Laser cutting works by focusing a laser beam onto sheet metal or another hard material. Mirrors, lenses and compressed gases such as carbon dioxide allow technicians to adjust the laser beam focus through a laser cutting nozzle.
The narrow beam then melts or burns away the material, and the technician can then move to the next area by moving the cutting materials or laser head. CAD technology allows the laser head to move across the cutting sheet metal or other material automatically.
History and Evolution of Laser Cutting Technology
1. The Birth of the Laser (1960s)
The story of laser cutting begins with the invention of the laser itself. In 1960, Theodore Maiman developed the first working laser at Hughes Research Laboratories. This ruby laser marked the start of a new era in precision cutting and machining.
2. Early Experiments and Industrial Adoption (1960s-1970s)
By the late 1960s and early 1970s, researchers and engineers started experimenting with laser technology for cutting applications. The first laser cutting machine was introduced in 1965 by the Western Electric Engineering Research Center, which used a carbon dioxide (CO2) laser to cut holes in diamond dies. This marked the first industrial application of laser cutting.
3. Advancements in CO2 Lasers (1970s-1980s)
CO2 lasers became the standard for industrial laser cutting due to their ability to cut a wide range of materials, including metals, plastics, and wood. Throughout the 1970s and 1980s, improvements in laser power and beam quality allowed for more precise and efficient cutting processes, making CO2 laser cutting machines a staple in manufacturing.
4. Introduction of Fiber Lasers (1990s)
The development of fiber laser technology in the 1990s revolutionized the laser cutting industry. Unlike CO2 lasers, fiber lasers use optical fibers doped with rare-earth elements to amplify the laser beam. This innovation brought several advantages, including higher efficiency, better beam quality, and lower maintenance requirements. Fiber lasers quickly gained popularity for their superior performance in cutting metals.
5. Modern Advancements and Automation (2000s-Present)
In the 2000s and beyond, laser cutting technology continued to advance with the integration of computerized numerical control (CNC) systems, automation, and software enhancements. These developments have significantly increased the speed, accuracy, and versatility of laser cutting machines. Today, fiber laser cutting machines are capable of handling complex geometries and intricate designs with unparalleled precision.
6. Future Trends and Innovations
Looking ahead, the laser cutting industry is poised for further innovation. Advances in laser sources, such as ultrafast lasers and green lasers, are expanding the range of materials that can be efficiently cut. Additionally, the integration of artificial intelligence (AI) and Industry 4.0 technologies promises to enhance the automation and optimization of laser cutting processes, driving even greater efficiencies and capabilities.
Applications of Fiber Laser Cutting Machine For Metal
1. Cutting and Shaping: Fiber lasers are widely used for cutting and shaping various metals such as steel, aluminum, copper, and brass. Their precision and speed make them ideal for intricate designs and complex parts.
Sheet Metal Processing: Perfect for cutting thin to thick sheet metals with high precision, minimizing waste and reducing the need for secondary processes.
2. Automotive Industry
Component Manufacturing: Used to manufacture precise and durable components like gears, exhaust parts, and intricate body components.
Prototyping: Fiber lasers are crucial in the rapid prototyping of new automotive parts, allowing for quick iterations and testing.
3. Aerospace Industry
Structural Components: Essential for cutting lightweight and strong materials used in aerospace structures, ensuring high precision and quality.
Maintenance and Repair: Used for the precise cutting and removal of damaged sections of aircraft components, facilitating efficient repairs.
4. Electronics Industry
Microelectronics: Ideal for cutting and etching fine patterns on circuit boards and microelectronic components.
Battery Manufacturing: Used in the precise cutting of battery foils and components, ensuring high performance and safety.
5. Jewelry and Fashion
Intricate Designs: Fiber lasers enable the creation of detailed and intricate designs on various metals, perfect for custom jewelry and fashion accessories.
Engraving and Marking: Widely used for engraving logos, serial numbers, and personalized messages on jewelry items.
Why Use Fiber Laser Cutting Machine For Metal
Fiber laser cutting machine for metal guarantee high speed and power performance. The fiber laser also allows a yield about 10 times higher when compared to the CO2 laser. The low environmental impact and the impeccable quality of the workmanship offer equally indispensable advantages for companies. In sectors increasingly pressed by customisation needs and tight deadlines, the acquisition of a laser metal cutting machine really makes the difference. Among the advantages for the company:
- Production times halved
- Reduction of energy consumption
- Reduction of warehousing costs
- Very high cutting quality
- High levels of customisation
Efficiency and versatility are combined with the valuable advantage of working without having to constantly change the tool and without mechanical contact with the material. This increases the safety for the operator who presides over the processing and the safety of the material itself, avoiding the risk of damage. The result is a more efficient and safe working environment and a reduction in waste that benefits the environment and the warehousing economy.
What Metals Can Be Cut By Fiber Laser
With a fiber optic laser beam, the maximum cutting power is concentrated in an infinitesimal diameter the size of a hair. Compared to gas laser sources, such as CO2, the fiber laser has a wavelength 10 times lower, about 1μm, which allows it to be better absorbed by the material. For this reason, a fiber laser machine can also cut metals such as copper and brass, which are not suitable for cutting with CO2 lasers. Among the metals indicated for fiber laser cutting include:
- Iron
- Steel
- Galvanised steel
- Stainless steel
- Aluminium
- Brass
- Copper
- Titanium
What Materials Fiber Laser Can't Cut
Despite the many excellent features of fiber laser cutting machines, there are still several materials they cannot cut. So, what materials are unsuitable for cutting with fiber laser cutting machines?
First of all, we need to be clear that the fiber laser cutting machine belongs to the category of metal cutting machine, so it can be used to process metal. But for the non-metal materials such as cloth, leather, it is not the better choice.
Secondly, the fiber laser cutting machine cannot cut the MDF, which mainly include fiberboard, wood fiber, and plant fiber, and some materials are made of urea-formaldehyde resin and artificial board made of adhesive. Because fiber laser cutting machine is belong to hot-processed. It will cause burning and burn the cutting edge, therefore it fail to meet the perfect cutting requirements. Therefore, these types of materials are currently not process with fiber laser cutting machines.
Besides, some materials are highly reflective and do not absorb the laser wavelength effectively. As a result, a significant portion of the laser energy is reflected back, which can damage the protective lens. Due to this issue, these highly reflective materials are currently not suitable for processing with fiber laser cutting machines.
Fiber Laser Cutting Parameters For Metal
Key Parameters Need Look For
Fiber laser settings are the key characteristics that define the behavior and output of a laser. These parameters include the following:
Wavelength:
The distance between two consecutive peaks or troughs of the laser beam’s electromagnetic wave. The wavelength determines the laser’s color and affects its interaction with materials.
Power:
The amount of energy per unit of time the fiber lasers deliver. A laser cutter’s power determines its cutting or engraving speed and ability to penetrate or heat up materials.
Pulse duration:
The time interval over which the laser emits a pulse. Pulse duration affects the laser’s material removal rate and thermal effects.
Repetition rate:
The number of pulses emitted per unit of time. Repetition rate affects the laser’s throughput and efficiency.
Beam quality:
A measure of how closely the laser beam’s properties match that of an ideal, single-mode Gaussian beam. Beam quality determines the laser’s focusability and spot size.
Polarization:
The orientation of the electric field vector of the laser beams. Polarization affects the laser’s interaction with certain materials and optical components.
Mode structure:
The spatial distribution of the laser beam’s intensity across its transverse dimensions. Mode structure determines the laser’s cutting or drilling pattern and the quality of its edges.
How Do Laser Parameters Influence Laser Cutting Quality?
Laser parameters play a crucial role in determining the quality of laser cutting. Here are some ways in which fiber laser settings can influence cutting quality:
- Power Laser power significantly affects cutting speed and quality. Higher power can increase cutting speed but may cause more thermal damage to the material, resulting in rougher edge quality. Lower power settings offer finer control, producing higher edge quality.
- Pulse Frequency Pulse frequency determines the number of laser pulses fired at the material per second. A higher pulse frequency can yield smoother and more precise cuts but may increase the likelihood of thermal damage. Lower pulse frequencies provide better control over the cutting process.
- Wavelength The laser beam's wavelength influences the material's absorption characteristics. Different materials absorb laser light differently, so the optimal wavelength for cutting varies with the material. For instance, CO2 lasers with longer wavelengths of 10.6 microns are ideal for cutting non-metallic materials, while fiber lasers with shorter wavelengths of 1 micron are better suited for metals. Understanding the differences between CO2 and fiber laser technology is essential for selecting the right laser for your application.
- Lens Type The focusing lens in the laser cutting system impacts beam quality and focal spot size, affecting the cutting quality. Different lens types cater to various cutting applications, such as general-purpose cutting lenses and collimating lenses for marking and engraving.
- Laser Beam Diameter The diameter of the laser beam affects its focusability and intensity. Smaller beam diameters offer higher precision and finer detail in the cutting process but may be more prone to deflection or beam distortion.
In summary, selecting the appropriate fiber laser settings for your cutting application can significantly impact cutting speed, precision, and quality. By understanding the roles of power, pulse frequency, wavelength, lens type, and beam diameter, you can optimize your laser cutting process to achieve superior results.
Choose the Parameters For Different Cutting Materials
Material | 1000W | 2000W | 3000W | 4000W | 5000W | 6000W |
Aluminium | 2 mm | 4 mm | 6 mm | 8 mm | 10 mm | 12 mm |
Brass | 1 mm | 3 mm | 5 mm | 7 mm | 9 mm | 11 mm |
Carbon Steel | 0.5 mm | 2.5 mm | 5 mm | 7.5 mm | 10 mm | 12.5 mm |
Stainless Steel | 1 mm | 3 mm | 5 mm | 7 mm | 9 mm | 11 mm |
Material | 7000W | 8000W | 9000W | 10000W | 11000W | 12000W |
Aluminium | 14 mm | 16 mm | 18 mm | 20 mm | 22 mm | 24 mm |
Brass | 13 mm | 15 mm | 17 mm | 19 mm | 21 mm | 23 mm |
Carbon Steel | 15 mm | 17.5 mm | 20 mm | 22.5 mm | 25 mm | 27.5 mm |
Stainless Steel | 13 mm | 15 mm | 17 mm | 19 mm | 21 mm | 23 mm |
Note: The tables provide a general guideline, and the actual performance may vary depending on the specific laser machine and its configuration. It is always recommended to consult the laser cutting machine manual or the laser cutting machine manufacturers for the most accurate settings. For 3000W Fiber laser cutting machine cutting parameter, your can click here for read. For high-power like 12000W fiber laser cutter parameter, you can can click here for more details.
Common Misconceptions About Laser Parameters
Laser cutting parameters play a crucial role in laser cutting, but some common misconceptions can lead to suboptimal cutting quality. Here are some misconceptions to watch out for:
- "More power always equals better cutting quality." While increasing laser power can boost cutting speed, it also raises the risk of thermal damage to the material. It's essential to find the optimal power setting for the desired cutting quality rather than simply increasing the power.
- "The higher the pulse frequency, the better the cutting quality." Higher pulse frequencies can provide smoother and more precise cuts, but they also increase the risk of thermal damage to the material. It's crucial to determine the optimal pulse frequency for the specific material and desired cutting quality.
- "Beam quality doesn’t matter as long as the laser is powerful." Beam quality significantly impacts cutting quality, as it affects the focusability and intensity of the laser beam. A poor-quality beam can result in poor cutting quality, regardless of the laser power.
- "All lenses are the same." Different lens types can influence beam quality and focal spot size, greatly affecting cutting quality. Choosing the right lens type for the specific cutting application is essential.
- "Laser parameters don’t need to be adjusted once they’re set." Fiber laser settings should be regularly monitored and adjusted to maintain optimal cutting quality. Factors such as material type, thickness, and cutting speed can all impact the optimal settings for a given cutting job.
Fiber Laser Cutting Machine For Metal Price
Type of Laser Cutting Machine | Price Range ($) |
CO2 / Gas | $2,000 to $1,000,000 |
Diode | $350 to $2,000 |
Fiber | $30,000 to $600,000 |
The best laser cutting machines for metals are fiber lasers, followed by CO2 lasers. The choice between these types depends on several factors, including the specific metal and its reflectivity, the metal's melting and vaporization temperatures, and the thickness of the workpiece.
Choosing the Right Laser Cutter
- Metal Type and Reflectivity:
- Fiber Lasers: Metals absorb shorter wavelengths, such as blue, violet, and ultraviolet, which are emitted by fiber lasers, making them highly effective for cutting metals.
- CO2 Lasers: These emit longer red and infrared wavelengths, which metals readily reflect. This makes CO2 lasers less effective for certain metals, particularly those with high reflectivity.
- Melting and Vaporization Temperatures:
- The temperatures at which the metal melts and vaporizes influence the laser power needed. Higher temperatures require more powerful lasers to achieve efficient cutting.
- Workpiece Thickness:
- Thicker materials necessitate higher power and energy density for effective cutting, impacting the choice and specification of the laser cutter.
Price Range
- Fiber Laser Cutters: Typically range from $30,000 to $600,000. They are preferred for their efficiency and ability to cut a variety of metals.
- CO2 Laser Systems: Prices vary from $10,000 to $200,000, offering a more affordable option for applications where their wavelength limitations are less impactful.
Fiber Laser vs. CO2 Laser: Which Is Better for Metal Cutting
Fiber lasers and CO2 lasers are two popular technologies used for metal cutting, each with its own set of advantages and limitations. Here's a comparison to help you determine which is better suited for your metal cutting needs:
Fiber Laser Cutting
Key Features:
- Fiber lasers use optical fibers doped with rare-earth elements to produce the laser beam.
- They operate at wavelengths around 1 micron, which is highly absorbed by metals, making them ideal for metal cutting applications.
- Fiber lasers offer high beam quality, allowing for precise and efficient cutting of various metals, including stainless steel, aluminum, brass, and copper.
- These lasers are known for their high cutting speeds, enabling rapid production and increased throughput.
Advantages:
- Superior cutting speed and efficiency, resulting in higher productivity.
- High beam quality ensures excellent cutting precision and edge quality.
- Low maintenance requirements and reduced operating costs compared to CO2 lasers.
- Suitable for both thin and thick metal cutting applications.
Limitations:
- Limited versatility for non-metallic materials due to the specific wavelength range.
- Higher initial investment costs compared to CO2 lasers.
CO2 Laser Cutting
Key Features:
- CO2 lasers use a gas mixture to produce the laser beam, typically operating at a wavelength of 10.6 microns.
- They offer versatility for cutting a wide range of materials, including metals, plastics, wood, and organic materials.
- CO2 lasers can provide high power output, making them suitable for thick metal cutting applications.
Advantages:
- Versatility in material compatibility, allowing for cutting of both metallic and non-metallic materials.
- Lower initial investment costs compared to fiber lasers for certain applications.
- Can provide high power output for thick metal cutting requirements.
Limitations:
- Slower cutting speeds compared to fiber lasers, resulting in reduced productivity.
- Lower beam quality may lead to rougher edge finishes and reduced cutting precision, particularly for thin metals.
- Higher maintenance requirements and operating costs due to gas consumption and more complex optical systems.
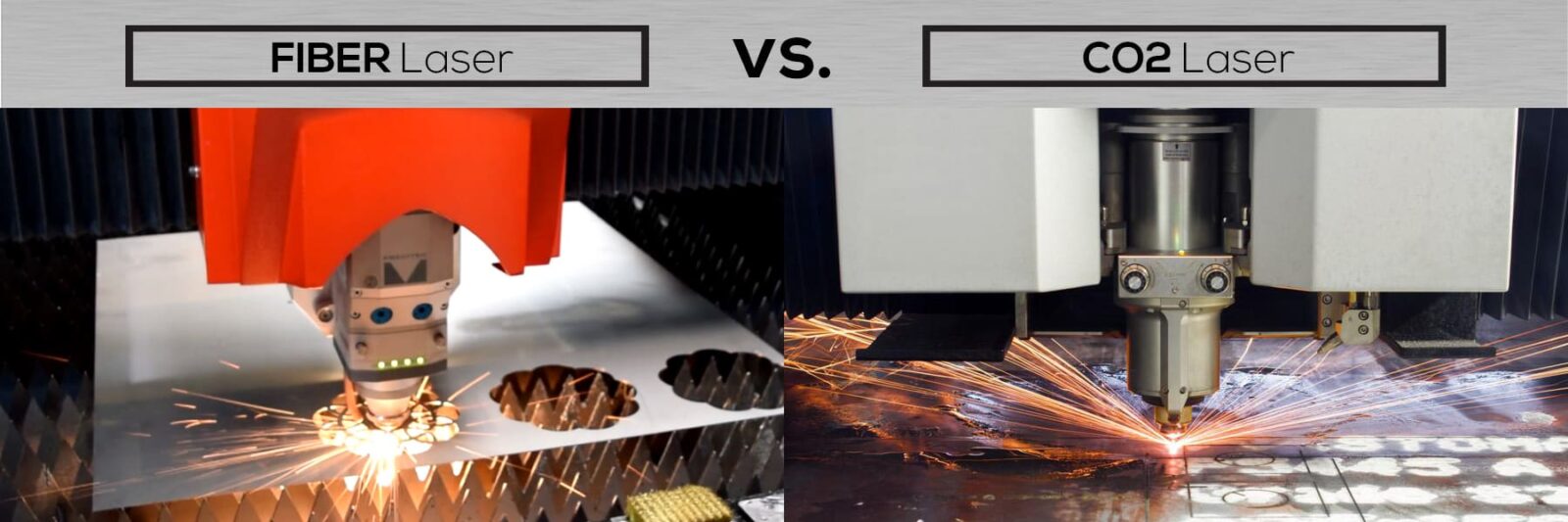
Fiber Laser vs. CO2 Laser: How To Choose For Your Project
When determining which laser to use for your project, there are several factors to take into consideration.
Type of material
Some metals, such as aluminum, are highly reflective and therefore do not absorb a CO2 laser beam very well. Still others, such as copper and brass, are so reflective that they are practically impossible to cut with a CO2 laser. In these applications, a fiber laser would be the better choice as its wavelength is more readily absorbed. Carbon steel and stainless steel can be easily cut with either laser method.
Material thickness
As mentioned earlier, the two types of lasers perform differently depending on the thickness of the material being cut. CO2 lasers have a longer wavelength than fiber lasers, and so they work better for thicker materials. “The long-wavelength works like a long sharp saw while the short wavelength works like a really sharp needle or drill. The really long sharp saw will be better at cutting thick stuff while a really sharp needle/drill will work better at piercing through thin stuff faste".-(Krrass Engineer) . The fiber laser works much better for thinner materials than a CO2 laser..
Finished edge
If a clean edge is your priority, CO2 laser cutting is the ideal choice, as it produces much smoother surface edges compared to fiber laser cutting. However, you can still achieve smooth edges on fiber laser-cut parts by using additional finishing and deburring techniques.
Below table outlines the primary distinctions between CO2 and fiber laser cutting technologies, making it easier to determine which type might be best suited for different applications.
Feature | CO2 Laser Cutting | Fiber Laser Cutting |
Wavelength | 10.6 micrometers | 1.06 micrometers |
Material Suitability | Best for non-metals (wood, acrylic, glass, plastics) | Best for metals (steel, aluminum, copper, brass) |
Cutting Speed | Slower on thin metals, faster on thicker materials | Faster on thin metals, slower on thicker materials |
Beam Quality | Lower beam quality | Higher beam quality |
Focal Diameter | Larger focal diameter | Smaller focal diameter |
Efficiency | Lower electrical efficiency | Higher electrical efficiency |
Maintenance | Requires regular maintenance | Maintenance-free operation |
Lifespan | Shorter lifespan | Longer lifespan (minimum 100,000 operating hours) |
Cost | Generally lower initial cost | Higher initial cost but lower operational costs |
Size | Larger in size | More compact design |
Applications | Non-metal engraving, cutting thick non-metals | Metal cutting, industrial cleaning, high-precision marking |
Cooling Requirements | Higher cooling requirements | Lower cooling requirements |
Future Of Fiber Laser Cutting Machine For Metal
Continuous advancements in fiber laser technology are revolutionizing the metal cutting industry. With the global fiber laser market projected to grow rapidly, the future looks promising for this innovative technology. Let’s explore some key trends and developments shaping the future of metal cutting with fiber lasers.
Trends and Developments
Increasing Power and Cutting Speed
Fiber laser technology is constantly evolving, with significant efforts directed toward enhancing power levels and cutting speeds. Higher-powered fiber lasers facilitate faster and more efficient metal cutting, significantly reducing production time and boosting productivity. As power levels continue to climb, we can anticipate even greater cutting speeds and the capacity to process thicker materials more effectively.
Integration of Automation and Industry 4.0
The integration of automation and Industry 4.0 principles is transforming fiber laser metal cutting systems. This includes the incorporation of robotics, advanced material handling systems, and sophisticated software for automated loading, unloading, and part sorting. Real-time monitoring, data analytics, and enhanced connectivity contribute to improved process control, predictive maintenance, and overall operational efficiency. The future of metal cutting with fiber lasers will see an increased adoption of these technologies, leading to higher levels of automation and productivity.
Development of Hybrid Laser Cutting Systems
Hybrid laser cutting systems that combine laser technology with other cutting methods, such as waterjet or plasma cutting, are gaining traction. These hybrid systems offer the combined advantages of multiple cutting technologies, providing increased versatility and the capability to handle a broader range of materials and thicknesses. This trend towards hybrid systems enhances the flexibility and adaptability of metal cutting processes, meeting diverse industrial needs.
In conclusion, the future of fiber laser cutting machine for metal is bright, driven by advancements in power, automation, and hybrid technologies. These developments promise to enhance efficiency, productivity, and versatility, positioning fiber lasers as a cornerstone of modern metal fabrication.
Krrass Fiber Laser Cutting Machine For Sale
Krrass fiber laser cutting machines are advanced industrial tools used for cutting metal sheets and plates with high precision and speed. They are equipped with the latest fiber laser technology, which offers numerous advantages over traditional CO2 lasers, including higher efficiency, lower maintenance, and better cutting quality.
Advantages of Krrass Fiber Laser Cutting Machines:
Cost-Effective: Lower operating costs compared to other cutting technologies.
High Quality: Consistent, high-quality cuts with smooth edges and minimal burr.
User-Friendly: Easy to set up and operate, with comprehensive support and training available.
Innovation: Incorporates the latest advancements in laser cutting technology.
Our robust design, advanced features, and reliable performance make us an excellent choice for businesses looking to enhance their cutting capabilities and productivity. Whether you are in the automotive industry, aerospace, or metal fabrication, Krrass has a fiber laser cutting machine to meet your specific needs.
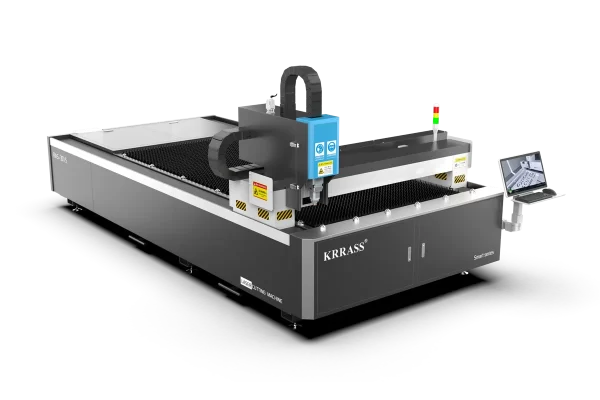