In the realm of industrial manufacturing, the 40KW laser cutting machine stands out as a powerhouse of precision and efficiency. These ultra high-power machines are essential for cutting through thick materials with speed and accuracy, making them invaluable in industries such as automotive, aerospace, and heavy machinery. Understanding the 40KW laser cutting machine price is crucial for businesses looking to invest in top-tier cutting technology that can enhance their production capabilities and reduce operational costs.
As the demand for high-power laser cutting machines grows, it becomes imperative to delve into the factors that influence their price. From the power output and brand reputation to the advanced features and after-sales support, several elements play a role in determining the overall cost. This article aims to provide a comprehensive guide on the 40KW laser cutting machine price, helping potential buyers make informed decisions by exploring the latest market trends, key manufacturers, and essential buying considerations.
Introduction To Ultra High-power(UHP) Laser Cutter
Ultra high-power laser cutting machines represent a pinnacle in laser cutting technology, bringing exceptional precision, efficiency, and power to industrial cutting applications. These machines are designed to handle extremely high power outputs, often ranging from 10 kW to 40 kW or more, enabling them to cut through thick and tough materials with remarkable speed and accuracy.
What Is Ultra High-Power Laser Cutting Machine
An ultra high-power laser cutting machine uses a high-power laser beam to melt, burn, or vaporize material, producing precise and clean cuts. These machines utilize advanced laser technology, typically fiber or CO2 lasers, to deliver the high power necessary for demanding industrial applications. The laser beam is directed and focused onto the material through a series of mirrors or optical fibers, creating a highly concentrated energy source that can cut through metals, plastics, composites, and more.
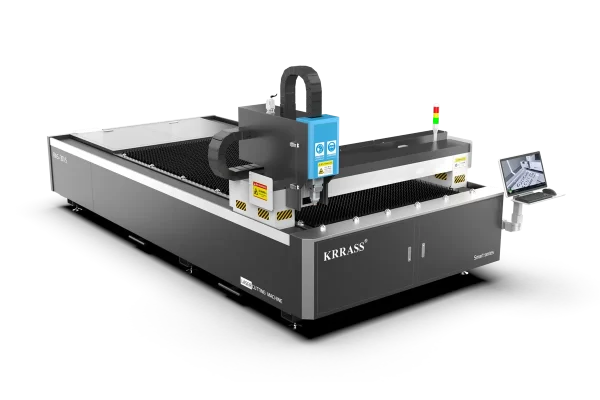
Evolution and Market Trends in Laser Cutting Technology
In the late 2010s and early 2020s, laser cutting market growth diverged in two distinct directions. One trend saw a surge in demand for low-power cutters (1–3 kW), driven by reduced equipment costs. The other trend was a significant increase in demand for ultra high-power (UHP) lasers. This demand was fueled by the high productivity and advanced technological capabilities of UHP lasers, offered at economical prices. The laser cutting industry experienced an unparalleled power transformation during this period. The maximum laser power available on cutting machine tools at fabrication trade shows skyrocketed from 6 kW in 2015 to an expected 40 kW in 2022, nearly a sevenfold increase. In the last three years alone, the available system power surged from 15 kW to 40 kW, marking a 2.5-fold increase.
Key Milestone Review
1970s - CO2 lasers were introduced, significantly improving cutting speed and thickness capabilities.
Early 2000s - Fiber lasers began to be used in industrial cutting, providing higher efficiency and lower maintenance costs.
Late 2000s - The emergence of kilowatt-class fiber laser cutting machines brought laser cutting technology into the high-power era.
Late 2010s to date - The rapid development of ultra-high power lasers, with maximum cutting power increasing from 6 kW to 40 kW, marks another leap in laser cutting technology.
Enabling Factors for UHP Laser Cutting
Three key developments in recent years have made the trend toward UHP cutting feasible: reduced cost per kW of fiber lasers, the availability of cutting heads capable of handling ultra-high laser power, and improved application engineering knowledge for high-power laser cutting.
Advantages of Using UHP Laser Cutting Machine
Prior to 2016, the high-power fiber laser cutter market was largely defined by machines ranging from 2KW to 6KW. Presently, the landscape has shifted dramatically, with 12KW, 15KW, 20KW, and 30KW systems emerging as the dominant players, with some even pushing the boundaries to 40KW. What accounts for the surge in popularity of high-power laser cutting machines? And how do they stack up against their medium and low-power counterparts? Let's delve into the advantages of high-power fiber laser cutter technology in comparison.
Advantage 1: Significantly Increased Cutting Thickness
High-power fiber laser cutters have revolutionized the cutting thickness capabilities. Today, these machines can effortlessly slice through aluminum alloy plates up to 40mm thick and stainless steel plates up to an astonishing 130mm. As technology advances, the cutting thickness is poised to increase further, driving down the processing costs for thick plates and expanding the application scope of fiber laser cutters in this domain.
For instance, a 15KW fiber laser can effortlessly tackle materials with a thickness exceeding 75mm, delivering impeccable cutting quality. This significant enhancement in cutting ability elevates the processing range of laser cutting machines to new heights.
Advantage 2: Doubled Efficiency for Medium and Thin Plates
When selecting laser cutting equipment, the cutting speed across different materials becomes paramount. Fiber laser cutting excels in processing medium and low-thickness sheets. By ramping up laser power, cutting speed can be doubled, resulting in exponential economic benefits.
Comparing common 20KW and 12KW models with a 6KW counterpart:
The difference is striking. The cutting efficiency for carbon steel and stainless steel of standard thicknesses is notably superior with 20KW and 12KW machines, boosting cutting speeds by 50-320%. While the advantage is less pronounced for thinner materials due to excess power, it becomes increasingly evident with thicker materials.
Advantage 3: Enhanced Cutting Process Diversity
Beyond the ability to cut thicker materials at higher speeds, increased laser power unlocks a plethora of cutting techniques, including the highly lauded high-speed bright surface cutting technology. This technique leverages small nozzles, low air pressure, and high-power lasers to swiftly slice through carbon steel plates of varying thicknesses, yielding smooth cutting sections with minimal processing taper.
To achieve rapid and bright surface cutting for carbon steel, three conditions must be met:
- Small nozzle: Utilizing double-layer nozzles, typically ranging between 1.0-2.0mm.
- High power: Higher power translates to greater limit thickness for bright surface cutting in carbon steel, significantly enhancing efficiency.
- Air pressure: Maintained within the range of 0.6-1.2Bar for optimal results.
Test of High Power Laser Cutting Machines
For the tests presented here, IPG YLS-40000 40 kW and IPG YLS-30000-ECO2 30-kW high-wall-plug efficiency fiber lasers were used, set up with 100 µm fiber core diameter and the IPGCut-HP cutting head to assess the cutting speed and quality in different metals. To the extent of the authors’ knowledge, 40 kW laser power in 100 µm fiber core diameter is the highest level of laser source intensity ever used to date for industrial laser cutting. We selected a 100 µm fiber core diameter because of the additional 10–25% increase gained in cutting speed compared to 150 µm diameter.
Higher cutting speeds
Our experiments show laser cutting speed increases with increasing average power up to 40 kW for all metals tested, including stainless steel, carbon steel, and aluminum. Figure 2 shows the increase of cutting speed vs. laser power within the range of 12 to 40 kW, for 6–40 mm carbon steel with air-assist gas. The percentage gain in speed increases with increasing metal thickness. For example, a 280% increase in cutting speed for 12-mm-thick carbon steel from 15 to 40 kW (a 270% increase in power) is observed, while a 420% increase is observed for 20-mm-thick carbon steel. For 30 mm carbon steel, going from 30 to 40 kW (a 33% power increase) leads to 66% faster cuts. This suggests that UHP lasers with even higher power may lead to further productivity gains in thick cutting.
Cost Analysis - Reducing Cost per Part for Rapid ROI
Ultra-high-power (UHP) laser cutting, compared to lower power alternatives, substantially lowers the cost per part, ensuring swift return on investment and heightened profitability.
1.Reduce gas consumption
A significant portion of the operating expenses in laser cutting arises from gas consumption, particularly as part thickness increases. UHP laser cutting maintains or even reduces gas pressure and nozzle size compared to lower-power counterparts. However, it dramatically boosts cutting speed, thereby slashing the time required per part and substantially curbing gas consumption. For instance, a 30 kW laser can halve the cycle time for cutting a standard 16-mm-thick stainless steel part compared to a 15 kW laser, effectively halving the gas consumption as well.
Apart from speed, UHP lasers offer additional gas savings. They enable swift, dross-free cutting of thick carbon steel using high-pressure air, eliminating the need for costly nitrogen or slow oxygen cutting. Moreover, UHP lasers allow for lower gas pressure requirements, significantly reducing gas usage and simplifying gas generation equipment specifications.
2.Save electricity
While electricity consumption for the laser and chiller tends to increase linearly with power, the overall electricity costs per part decrease with higher laser power due to reduced cycle time. Continuous advancements in high-power fiber lasers have pushed energy efficiency beyond 50%, further contributing to electricity savings.
3.Cost-effectiveness of UHP laser systems
Despite doubling productivity compared to lower power systems, UHP laser cutting is not proportionally more expensive. The cost per kilowatt decreases with higher laser power, and the higher laser cost is absorbed within the total machine tool cost. Thus, a UHP laser cutter with double the productivity may only incur a 30–40% higher capital cost.
4.Enhanced productivity
With significantly enhanced productivity, a single UHP system can replace multiple lower-power systems, necessitating a smaller footprint, fewer operators, and reduced facility preparations. However, maintaining productivity demands higher reliability standards for UHP fiber laser sources and cutting heads. These components must ensure stable power output, beam quality, and reliable operation under high optical power, gas pressure, dust, process heat, and acceleration.
Guide For 40KW Laser Cutting Machine
Laser cutting machines have revolutionized the manufacturing industry with their precision and efficiency. These machines use a high-powered laser beam to cut through various materials, including metal sheets, with incredible accuracy. One of the most powerful laser cutting machines available in the market is the 40000W laser cutting machine.
Incredible cutting capability
The 40,000W high-power thick plate laser cutting machine has been upgraded with stronger cutting capabilities. The entire machine is equipped with a 40,000W ultra-high power laser. While meeting the processing needs of ultra-thick plates, the cutting speed of medium-thick plates has been greatly improved.
Compared with 12000W air cutting, the cutting thickness is increased by 333% and the cutting speed is increased by 447%. It bids farewell to the past problems of excessive plate thickness and limited production, and is more suitable for production needs.
Maximum cutting thickness
40000W maximum cutting thickness up to 200mm, The comprehensive processing efficiency of Bond Laser 40000W is increased by 50%-80%. It can cut 20mm carbon steel to 6m/min and 30mm carbon steel to 2.4m/min.
The 40000W laser cutting machine is known for its exceptional cutting capabilities. With a maximum cutting thickness of, it can effortlessly slice through thick metal sheets with ease. This makes it an ideal choice for industries that require heavy-duty cutting operations.
Whether you need to cut steel, aluminum, or any other type of metal, this powerful machine can handle it all. Its high wattage ensures that even the thickest materials can be precisely cut without compromising on quality.
Features of 40KW laser cutter
The 40000W laser cutting machine comes with a range of features that make it stand out from other machines in its class. Some of its notable features include:
- Precision Cutting: The high-powered laser beam ensures precise and clean cuts, resulting in superior finished products.
- High Efficiency: With its immense power, this machine can complete complex cutting tasks in a fraction of the time compared to traditional methods.
- Versatility: It can cut through various materials, including metals like stainless steel, carbon steel, and aluminum.
- User-Friendly Interface: The machine is equipped with an intuitive interface that allows operators to easily control and monitor the cutting process.
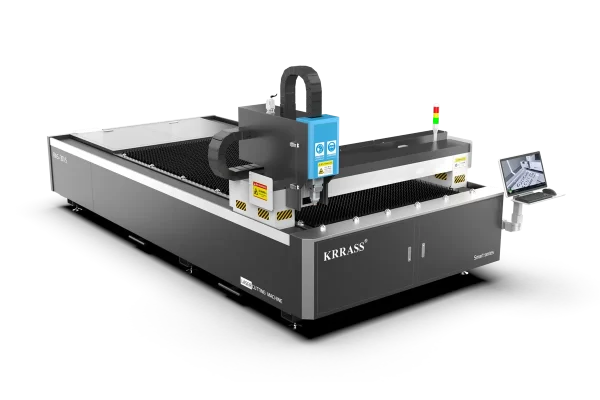
40KW laser cutting machine components
- It adopts high-rigidity and ultra-heavy plate welding bed, unique integrated welding process, high vibration resistance and strong rigidity. The high-precision gantry milling integrated forming bed mounting surface greatly improves high-speed operation accuracy, durability and higher production efficiency.
- Fully protective thickened sheet metal protective cover, safe and environmentally friendly. Intelligent high-definition monitoring allows you to observe the cutting status in real time. Glass observation window, national laser protection standards.
- The large ultra-high-definition display screen and the intelligent central control system provide real-time monitoring. The monitoring screen and operation interface are split into upper and lower screens to keep track of the production progress at any time.
- Equipped with a smart engine, a glimpse of front-end technology and a high-performance bus control system to achieve highly intelligent and flexible processing. Flexible production, agile and compatible, greatly improve the cutting performance and stability of the equipment.
- Precision transmission system composed of world-renowned brand components, intelligent automatic focusing laser head, brand servo motor, reducer and high-precision guide rail, rack, gear, ball screw, etc.
Applications
The 40000W laser cutting machine finds extensive use in various industries due to its exceptional cutting capabilities. Some of its common applications include:
- Automotive Industry: The machine is used for precise cutting of metal components required in the automotive manufacturing process.
- Aerospace Industry: It is utilized for cutting intricate parts used in aircraft construction.
- Shipbuilding Industry: The machine can effortlessly cut thick metal sheets required for shipbuilding.
- Furniture Manufacturing: It enables precise cutting of metal components used in furniture production.
The power and versatility of a 40000W laser cutting machine make it an indispensable tool in modern manufacturing processes. Its ability to cut through thick materials with precision and efficiency sets it apart from other machines. Whether you are in the automotive, aerospace, shipbuilding, or furniture industry, this machine can greatly enhance your production capabilities.
What Is 40KW Laser Cutting Machine Price
The cost of a 40KW fiber laser cutting machine varies, but based on recent listings, these machines are priced around $300,000 to $320,000.
40,000W is a relatively high power level, and these types of machines are typically used in industrial-grade applications. They can be very expensive and may need to be customized based on specific application needs. Therefore, if you need to know the exact price of 40000W fiber laser cutting machine, it is recommended to contact the manufacturer or supplier directly to get the latest quotation.
When considering such an investment, it is important to factor in additional costs such as shipping, taxes, and potential customization based on your specific needs. It’s also beneficial to request quotes from multiple suppliers to compare prices and features comprehensively.
The following are recommended world-class suppliers:
- IPG Photonics
- IPG Photonics is known for its high-power fiber lasers, including 40KW models, which are used in various industrial applications.
- Trumpf
- Trumpf offers a range of high-power laser cutting machines, including those in the 40KW range, known for their precision and efficiency.
- Bystronic
- Bystronic manufactures advanced laser cutting machines, including models with 40KW power, suitable for cutting thick and large metal sheets.
- Han's Laser
- Han's Laser provides a variety of high-power laser cutters, including 40KW machines, widely used in heavy industrial sectors.
- Krrass
- Krrass is a Chinese brand that offers high-power fiber laser cutting machines up to 40KW, designed for cutting thick materials with high precision.
Differences Between A 40000w And A 20000w Fiber Laser Cutting Machine
Cutting Thickness Capabilities:
A 40,000W machine can cut through much thicker materials compared to a 20,000W machine. For instance, in stainless steel, a 40,000W machine can cut up to 100mm (3.94″) thick, while a 20,000W machine is limited to around 60mm (2.36″) thick. For aluminum, a 40,000W machine can cut up to 80mm (3.15″) thick, whereas a 20,000W machine maxes out at around 50mm (1.97″) thick. Similarly, for carbon steel, the 40,000W machine can handle up to 100mm (3.94″) thickness, while the 20,000W machine is restricted to 60mm (2.36″) thick.
Cutting Speed:
The higher 40000W power allows for faster cutting speeds compared to a 20000W machine, especially on thicker materials.
Machine Size/Cutting Area:
40,000W machines typically feature a larger cutting area, often up to 12000x2500mm (39×8 ft), designed to handle larger and thicker workpieces. In contrast, 20,000W machines generally have a smaller cutting area, making them more suitable for cutting smaller or thinner workpieces.
Cost:
A 40,000W fiber laser is considerably more expensive than a 20,000W machine, reflecting its higher power and enhanced capabilities. On Alibaba, a 40,000W machine is listed at approximately $30,000 to $32,000, whereas 20,000W machines are generally less costly.
Maintenance Costs Associated with a 40,000W Fiber Laser Cutting Machine
Electricity Costs
A 40,000W fiber laser machine incurs substantial electricity consumption due to its powerful laser source. For example, a 1000W laser typically consumes about 6.6kW per hour of operation. Thus, a 40,000W machine would consume around 264kW per hour, making electricity one of the major ongoing operating costs for such a high-powered laser.
Consumable Gas Costs
Assist gases like oxygen, nitrogen, or compressed air are essential for laser cutting various metals. Gas consumption increases with both laser power and material thickness. Consequently, a 40,000W machine cutting thick materials will use large volumes of assist gas, significantly adding to operating costs.
Replacement of Wear Parts
Components such as protective lenses, focus lenses, nozzles, and ceramic rings require regular replacement, typically every 500 hours of operation. For a frequently used 40,000W machine, these costs can accumulate quickly. Approximate costs are:
- Protective lens: $15-$30
- Nozzle: $15-$30
- Focus lens: $150
- Ceramic ring: $100
Maintenance and Repair
Regular maintenance is essential to check alignments, lubricate components, and clean the machine. Repair costs for any failures or damaged components can be high, given the complexity and size of a 40,000W machine.
While the initial cost of a 40,000W fiber laser is very high (approximately $30,000-$32,000), the ongoing operating and maintenance expenses due to high electricity usage, gas consumption, wear part replacements, and regular maintenance/repairs can also be substantial over the machine’s lifetime, especially when operating at high utilization and cutting thick materials.
When is a High-Power Laser Cutter Needed?
Cutting Thick Materials
High-power laser cutters, such as 40KW machines, are essential for cutting extremely thick materials. For example, a 40KW laser cutter can handle up to 100mm thick stainless steel and carbon steel, as well as 80mm thick aluminum. These machines are indispensable when the material thickness exceeds the capabilities of traditional low-power laser cutters.
Large-Scale Production
In large-scale production environments, high-power laser cutters significantly enhance production efficiency. The cutting speed of high-power lasers is much faster than that of lower-power lasers, which considerably reduces the cutting time per part and increases overall production output and economic benefits.
High-Precision Cutting
High-power laser cutters achieve high-precision cuts, especially for intricate shapes and fine details. This precision is crucial in industries like aerospace, automotive manufacturing, and electronics, where high accuracy is a primary requirement.
Reducing Operating Costs
Despite the high initial purchase cost, high-power laser cutters can reduce per-part production costs over time. They decrease cutting time and assist gas consumption (such as oxygen or nitrogen), leading to lower operational expenses. Furthermore, with ongoing advancements in technology, the energy efficiency of high-power laser cutters has been improving, further reducing electricity consumption.
Larger Cutting Area
High-power laser cutters often feature larger cutting areas, such as worktables up to 12000x2500mm, enabling them to handle larger workpieces. This is particularly advantageous for cutting large-format materials.
In summary, high-power laser cutters are ideal for applications requiring the cutting of thick materials, large-scale production, high-precision cutting, cost-effective operation, and handling large workpieces.
Conclusion
The future of ultra high-power laser cutting technology is poised for remarkable advancements, driven by increasing demands for efficiency, precision, and capability in industrial applications. Companies like KRRASS are at the forefront of this evolution, offering state-of-the-art 40KW laser cutting machines that significantly enhance cutting performance and productivity.
These machines, priced around $300,000 to $320,000, represent a significant investment but bring unparalleled advantages. They can cut through extremely thick materials, such as 100mm stainless steel, 100mm carbon steel, and 80mm aluminum, at unprecedented speeds. This capability not only meets but exceeds current industrial requirements, positioning businesses to handle more complex and larger-scale projects with greater efficiency.
KRRASS’s 40KW laser cutters also feature expansive cutting areas, accommodating workpieces up to 12000x2500mm. This versatility is crucial for industries dealing with large-format materials, making these machines an indispensable asset for future industrial applications. As technology continues to advance, we can expect further improvements in energy efficiency and operational cost reductions, making high-power laser cutters even more advantageous.

Reviewed by 1 user
Fiber laser cutting machine
good machine