Are you searching for a V grooving machine for sale? Finding the best V grooving machine can significantly enhance your manufacturing processes, ensuring precision and efficiency. However, with numerous options available, making the right choice can be challenging. This guide will give you a comprehensive understanding of V grooving machine before make the formed decision, include principle, types comparison, and suppliers recommendation and so on.
Understanding V Grooving Machine For Sale
V grooving machine is a professional equipment used to process sheet metal workpieces. By cutting V-grooves on the sheet metal, it can be bent into the desired shape at a specific position. This technology is widely used in the sheet metal processing industry, providing an efficient and precise solution for the bending and processing of workpieces.
What Is V Grooving Machine
The V-groove machine is a special equipment for processing V-grooves on sheet metal. It is a sheet metal processing machine that is widely used in manufacturing and metal processing.
The V-shaped groove machine cuts V-shaped grooves on the surface of the metal sheet through a special cutting tool. These grooves can be straight or curved, depending on the design of the cutter and the setup of the cutting path. The workpiece produced by this technology has a small bending radius, no obvious color change, and requires little bending force. In addition, the straightness error of the round edge of the narrow and long workpiece is reduced, and ordinary bending machines and tooling can be used to bend workpieces with complex cross-sectional shapes.
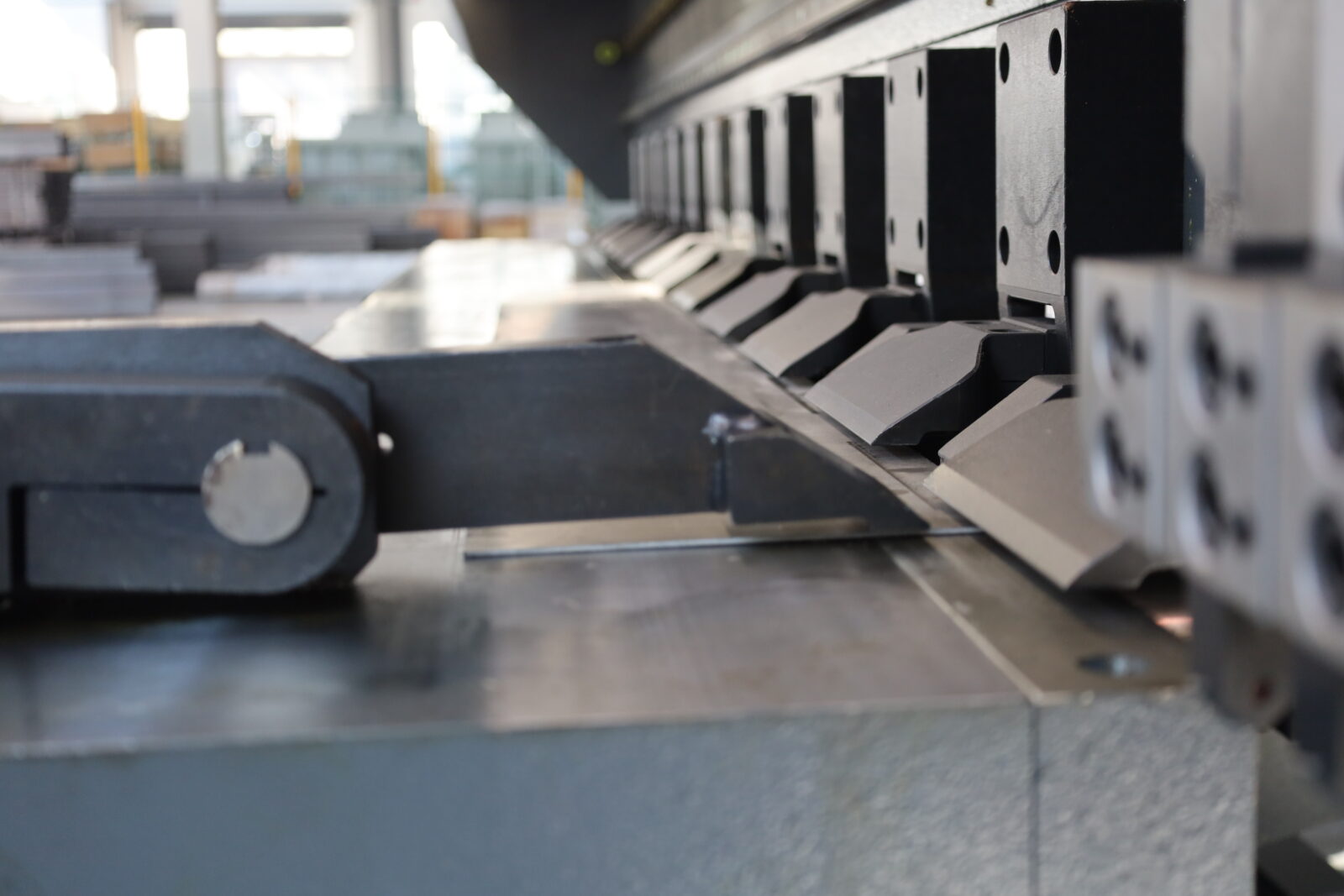
Good Applications For Metal Parts
V grooving machine is suitable for various metal materials, such as steel plate, stainless steel plate, aluminum plate, etc. Sheet metal of different thicknesses and sizes can be processed. V-groove machines usually have high cutting accuracy, which can ensure accurate V-groove cutting to meet the design requirements.
And they have important applications in the manufacture of metal parts, special sheet metal processing and the production of metal components with V-shaped bending structures. These slots can be used to bend and bend metal materials, giving components greater strength and stability. In addition, V-shaped grooves can also be used for splicing, connecting and assembling different metal parts, providing a stronger combination.
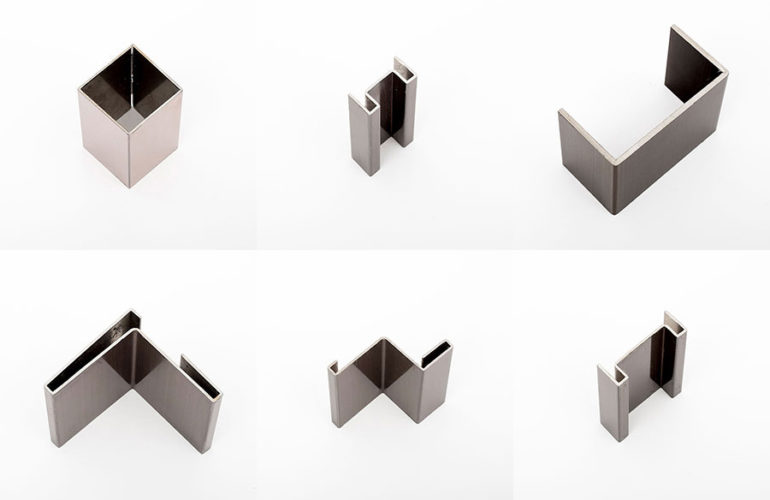
Some advanced V-groove machines are equipped with automated features, including CNC control and automatic tool adjustment, making operation easier and increasing productivity.
Processing Principle
First, fix the metal sheet to be processed on the workbench of the V-groove machine. Fixing the material is a key step to ensure that the metal plate does not move or shake during the cutting process to ensure the accuracy of the cut. According to the size and shape of the V-groove to be processed, select the appropriate cutting tool. The cutting tool may be a cutting blade or a cutting tool with a V-shaped edge, the shape of which matches the V-groove to be cut.
Then, adjust the cutting depth and angle of the V-groove machine to suit different processing requirements. The depth of cut determines the depth of the V-groove, and the angle determines the opening angle of the V-groove. Start the V-groove machine, the cutting tool moves along the predetermined path, and forms a V-shaped groove by cutting the surface of the metal plate. During the cutting process, a part of the metal plate is removed by the cutting action of the cutting tool, thereby forming a V-shaped groove.
Finally, when the cutting tool finishes cutting along the set path, stop the operation of the V-groove machine. Then, take out the cut metal plate to complete the V-groove process.
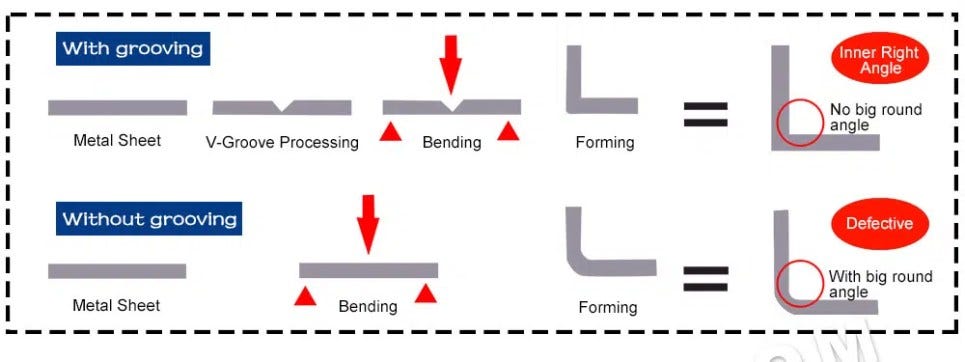
Structure Overview
Frame/Body:
- The main structure that supports all other components.
- Usually made of heavy-duty materials like cast iron or steel to ensure stability and durability.
- Houses the motor, control systems, and other critical parts.
Worktable/Bed:
- The surface on which the material to be grooved is placed.
- Equipped with clamping systems to hold the material securely in place during the grooving process.
- May have adjustable stops and guides to ensure precision and repeatability.
Grooving Head/Tooling:
- Contains the cutting tools or blades that create the V-shaped grooves.
- Can be a single-point tool or multiple tools arranged in a specific configuration.
- The depth and angle of the groove can usually be adjusted depending on the requirements.
Motor/Drive System:
- Powers the movement of the grooving head.
- May include variable speed controls to adjust the cutting speed based on the material and desired groove quality.
- Can be an electric motor or a hydraulic system, depending on the machine design.
Control System:
- Manages the operation of the machine, including the positioning of the workpiece and the grooving head.
- Modern machines often feature computerized numerical control (CNC) systems for precise and automated operation.
- Includes an interface (buttons, touchscreens, or computer interfaces) for the operator to input settings and commands.
Linear Guides/Rails:
- Ensure smooth and precise movement of the grooving head along the worktable.
- Typically involve ball screws, linear bearings, or similar mechanisms to minimize friction and maintain accuracy.
Depth Control Mechanism:
- Allows for the precise adjustment of the groove depth.
- Can be mechanical, hydraulic, or electronically controlled, depending on the sophistication of the machine.
Safety Features:
- Emergency stop buttons, protective covers, and sensors to prevent accidents.
- Safety interlocks to ensure the machine operates only when it is safe to do so.
Chip/Dust Collection System:
- Collects and removes debris produced during the grooving process.
- Essential for maintaining a clean work environment and prolonging machine life.
How To Operate A V Groover Machine
Using a V-grooving machine involves several steps to ensure precision and safety. Here's a general guide on how to use a V-grooving machine:
Preparation
- Read the Manual:
- Always start by reading the manufacturer’s manual specific to your V-grooving machine to understand its operation, safety guidelines, and maintenance requirements.
- Inspect the Machine:
- Check the machine for any signs of wear, damage, or loose components.
- Ensure all safety features, such as guards and emergency stops, are functional.
- Select and Prepare Material:
- Choose the appropriate material for grooving (e.g., metal, wood, composite panel).
- Ensure the material is clean and free from any contaminants that could affect the grooving process.
Setting Up the Machine
- Install the Cutting Tool:
- Choose the appropriate V-grooving tool or blade for the desired groove angle and depth.
- Securely install the tool in the grooving head, following the manufacturer’s instructions.
- Adjust Machine Settings:
- Set the depth and angle of the groove according to the requirements of your project.
- Adjust the worktable, stops, and guides to position the material accurately.
- Secure the Material:
- Place the material on the worktable.
- Use clamps or other securing mechanisms to hold the material firmly in place, preventing any movement during the grooving process.
Operating the Machine
- Power On the Machine:
- Ensure all safety guards are in place.
- Turn on the machine and let it reach the operating speed if it has a motor-driven head.
- Input Parameters (for CNC Machines):
- If using a CNC V-grooving machine, input the required parameters such as groove depth, angle, and positions into the control system.
- Load the program if it's a pre-designed CNC task.
- Start Grooving:
- Manually guide the material or let the CNC system control the movement if automated.
- Monitor the process closely to ensure the groove is being cut accurately.
- Adjust the feed rate if necessary to achieve a clean and precise groove.
Post-Grooving
- Power Off the Machine:
- Once the grooving is complete, turn off the machine.
- Wait for all moving parts to come to a complete stop before removing the material.
- Inspect the Groove:
- Check the groove for accuracy in depth, angle, and placement.
- Make any necessary adjustments for future grooves if needed.
- Clean the Machine:
- Remove any debris, chips, or dust from the machine.
- Ensure the cutting tool is clean and inspect it for wear.
- Store the Machine Properly:
- If the machine won’t be used for an extended period, follow the manufacturer’s recommendations for storage and maintenance.
Safety Tips
- Wear Personal Protective Equipment (PPE):
- Always wear safety glasses, gloves, and ear protection.
- Wear a dust mask if working with materials that produce fine dust.
- Maintain a Clean Work Area:
- Keep the area around the machine clean and free of obstructions.
- Stay Alert:
- Do not operate the machine if you are tired or under the influence of drugs or alcohol.
If you want to learn about the step-by-step operation of horizontal V groover, pls click here to read.
V Grooving Machine For Sale - Main Types
Nowadays V grooving machine for sale on the market has various types, each type of V-groove machine is designed to meet specific needs and applications, ranging from simple manual operations to complex, automated processes in industrial settings. Here are the primary types of V groove machines:
- Manual V-Groove Machines:
- Operated by hand, suitable for small-scale or low-volume production.
- Common in workshops where precision and control by the operator are essential.
- Semi-Automatic V-Groove Machines:
- Combine manual input with automated processes to enhance efficiency.
- Operators might load the material and initiate the process, while the machine controls the cutting.
- Fully Automatic V-Groove Machines:
- Highly automated, requiring minimal operator intervention.
- Ideal for high-volume production environments.
- Equipped with advanced features like programmable controls, automatic material feeding, and precise cutting mechanisms.
- CNC V-Groove Machines:
- Utilize computer numerical control (CNC) to automate the cutting process.
- Offer high precision and repeatability, suitable for complex and intricate groove patterns.
- Widely used in industries requiring high precision, such as aerospace, automotive, and electronics.
- Portable V-Groove Machines:
- Designed for mobility and ease of use on-site or in small workshops.
- Often used in construction, repair, and maintenance applications.
- Fixed V-Groove Machines:
- Stationary machines used in dedicated production lines.
- Provide stability and consistency for continuous operations.
- Hydraulic V-Groove Machines:
- Use hydraulic power to drive the cutting tools, providing greater force and capacity for thicker and harder materials.
- Suitable for heavy-duty applications.
- Pneumatic V-Groove Machines:
- Powered by compressed air, offering a balance between power and portability.
- Common in environments where electricity is not feasible or where air-powered tools are preferred.
- Laser V-Groove Machines:
- Utilize laser technology to create precise grooves without physical contact with the material.
- Suitable for delicate materials and applications requiring high precision and minimal material deformation.
Vertical and Horizontal V-grooving Machines: Comparison Analysis
V-grooving machine is a piece of equipment used for cardboard processing. It is mainly used to V-groove cardboard to facilitate folding and assembly. According to its different structural forms, V-shaped grooving machines can be divided into two types: vertical and horizontal, it's also most common classification method on the market.
What Is A Vertical V Slotting Machine
Vertical V-shaped grooving machine means that the overall structure of the equipment is in a vertical layout, the work surface is perpendicular to the ground, and the operator stands to operate. Vertical V-grooving machines are usually small in size and occupy a small area, making them suitable for use in workplaces with limited space. The vertical V-shaped grooving machine is simple to operate and easy to maintain, and is suitable for use by small carton manufacturers.
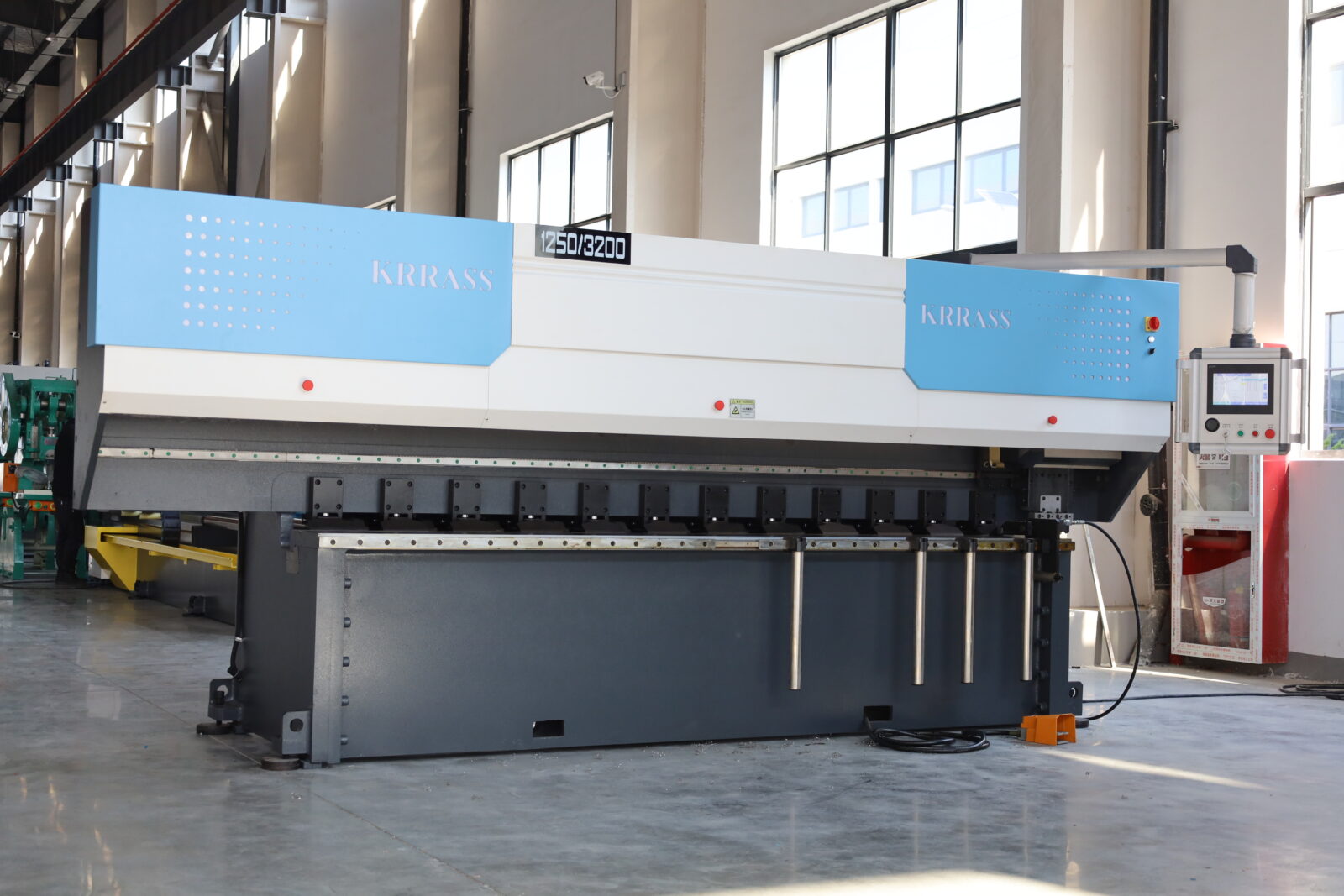
What Is A Horizontal V Slotting Machine
Horizontal V-shaped grooving machine means that the overall structure of the equipment is in a horizontal layout, the work surface is placed horizontally on the ground, and the operator sits next to the equipment to operate. Horizontal V-shaped grooving machines are usually suitable for large carton manufacturers. They have high production efficiency, easy operation, and are suitable for long-term continuous operations.
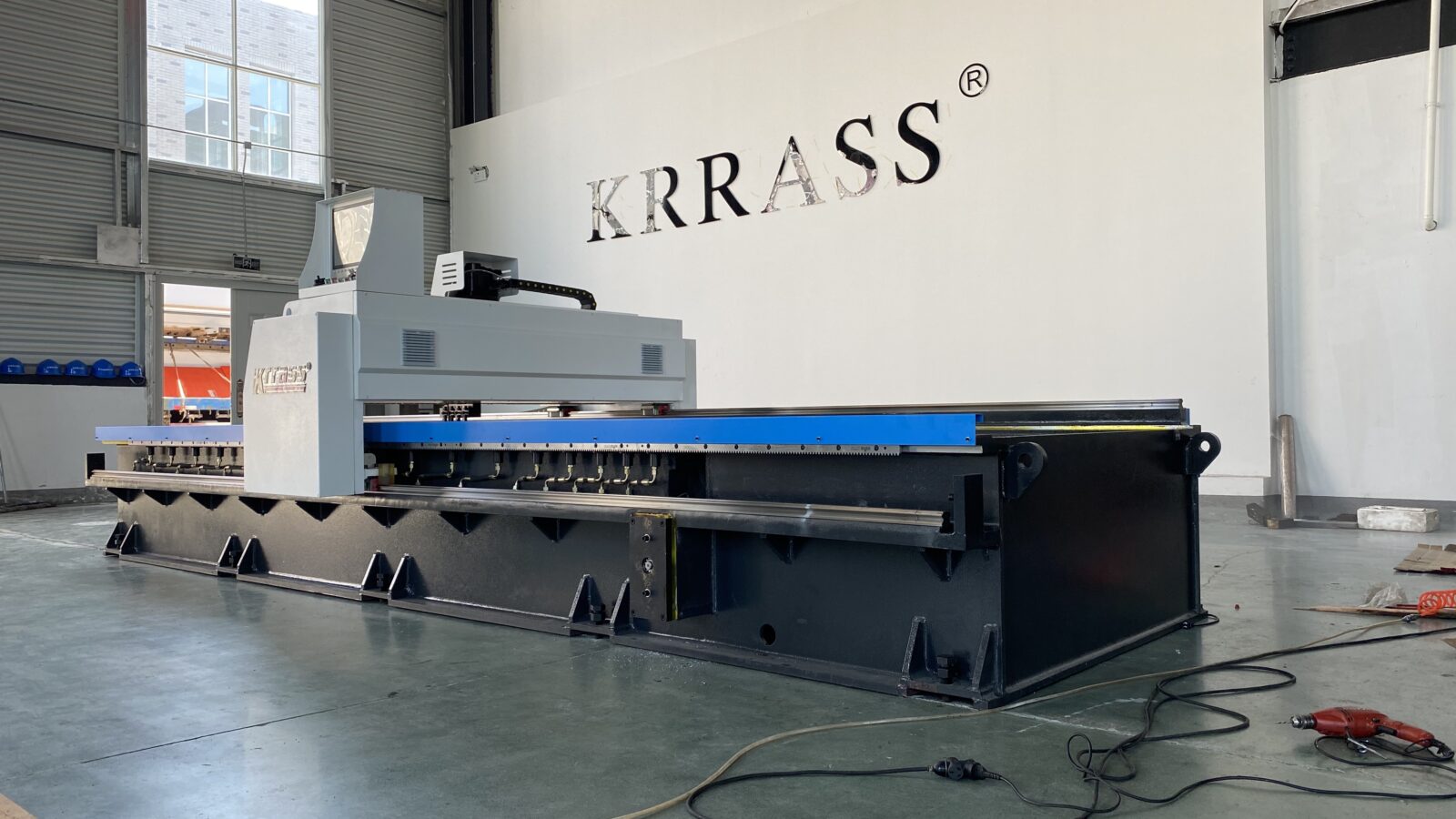
Diiference Explained
1. Accuracy
When Vertical V Grooving Machine working, the planer is fixed to the table and runs in a straight line, and the accuracy of the distance from the tool tip to the table is controlled within the range of 0.02mm; When horizontal machine working, the knife faces a platform with a width of 1.5 meters and a length of more than 4 meters. It is difficult to control the accuracy in the range of 0.1 mm.
2. Power consumption
The vertical tool rest moves back and forth, and its weight is about 60kg; The gantry and the tool rest move back and forth together, and its weight is 1000kg. Its energy consumption is more than 10 times that of the vertical router, so the vertical router is an energy-saving and environmentally friendly equipment.
3. Processing capacity
Vetical Groove has more than a dozen independent pressing plates and more than a dozen independent clamps to automatically clamp the sheet material. It is easy to process regardless of the size of the sheet, and it can be grooved in both horizontal and vertical directions. The smallest workpiece is 80* 80mm; Horizontal groove is only for large-sheet grooving. After grooving longitudinally, the grooving cannot be horizontally clamped due to deformation of the sheet material.
4. Crafts
The Vertical V Grooving Machine work surface of the vertical is made of high-quality mold steel after heat treatment and is finely ground by a grinder, and the surface fineness reaches the effect of a mirror surface; The work surface of the horizontal is welded from ordinary iron plates. The stainless steel plates are harder than it, and the shredders and damaged blades make the table pits and bumps. This is the reason why the processed product is spotted.
5. Installation
The vertical router is welded by steel plates, has high strength, and runs smoothly and quietly. It can work stably only by placing it on a flat and solid cement floor and leveling and installing it, and it is very convenient to move and hoist.; However, due to the high-speed operation of the horizontal groover, the impact force is large, and the platform needs to be adjusted. The concrete foundation must be made according to the installation drawing, and the civil engineering must be made.
6. Operation safety
The vertical groover is hydraulically automatically clamped the workpiece, automatically positioned, and works automatically, and the operator is away from the moving parts of the machine tool; The horizontal grooving machine clamps the workpiece within the range of motion of the machine tool. The gantry moves at a high speed, and the control part runs with the gantry, which is easy to cause personal injury to the operator and poses a great safety hazard.
In order to give you a more intuitive understanding of the difference between the two, here is a detailed table.
Item | Verticle V Grooving Machine | Horizontal V GroovingMachine |
Processing range | It is suitable for workpieces that need to be grooved around, but for longer workpieces, an additional workbench is required to carry them when processing the short side, and the operation is not very convenient. | It is suitable for workpieces of various large sizes and shapes, and has three-axis CNC machining capabilities. |
Workbench processing technology | The surface of the workbench is made of high-quality mold steel, which has undergone overall heat treatment and fine grinding with a grinder, and the surface finish has reached a mirror effect. | The surface of the worktable is welded by ordinary iron plates, but the hardness of the workpiece is higher than it. The work surface needs to be restored periodically because the grooved wires and blades can damage the work surface. |
Processing efficiency | The minimum distance between the V-shaped groove and the edge is 10mm, and the cutting speed is 40m/min. | The minimum distance between the V-shaped groove and the cutting edge is 8mm, and the cutting speed is 50m/min or higher. No reciprocating feeding is required, and the efficiency is higher. |
power loss | The front and rear movement loss of the tool holder is small, and the power of the main motor is 4.4kW. | The gantry and the knife rest move back and forth together, and the loss is large, and the power of the main motor is 5.5kW. |
Safety | Adopt hydraulic automatic clamping workpiece, automatic positioning, automatic work, the operator is far away from the moving parts of the machine, improving safety. | The workpiece is clamped within the range of motion of the machine tool, and the gantry moves at high speed, so the operator must pay attention to safe use. |
Overall effect | Since the workpiece needs to be automatically fed after clamping, the iron filings generated by the grooving often scratch the decorative surface. When processing large-sized workpieces, frequent alignment and movement are required, which is more likely to damage the surface. | The workpiece does not need to be moved during the processing, and the whole process can be operated by one person to ensure that the decorative surface of the workpiece will not be scratched and the surface processing quality is guaranteed (an important reason for use in the elevator industry). |
Horizontal vs Vertical: How To Select
Choosing the right vertical or horizontal V-grooving machine involves considering various factors based on your specific needs, the materials you work with, and the intended applications. Here's a detailed guide to help you make an informed decision:
1. Understand the Types of V-Grooving Machines
Vertical V-Grooving Machines
- Application: Typically used for creating V-grooves on vertical surfaces.
- Advantages:
- Suitable for large panels or surfaces.
- Ideal for architectural applications, furniture, and decorative panels.
- Allows for precise vertical cuts.
- Limitations:
- May require more floor space.
- Handling and setup of large panels can be cumbersome.
Horizontal V-Grooving Machines
- Application: Best for creating grooves on horizontal surfaces.
- Advantages:
- Generally more compact and easier to handle.
- Suitable for smaller pieces and more intricate designs.
- Easier to automate and integrate into existing production lines.
- Limitations:
- Limited to the size of the machine's table.
- May not be suitable for very large panels or surfaces.
2. Material Compatibility
- Types of Materials: Ensure the machine can handle the materials you work with, such as aluminum, stainless steel, composite panels, wood, MDF, or other types of sheet metal.
- Thickness: Check the maximum and minimum thickness of materials the machine can process.
3. Precision and Accuracy
- Tolerance Levels: Look for machines with high precision and low tolerance levels, especially if you're working on high-end projects or products.
- Repeatability: Ensure the machine can consistently produce the same quality and dimensions.
4. Production Volume and Speed
- Throughput: Consider the machine's speed and how many pieces it can process per hour or day.
- Cycle Time: Look at the time required to complete a single operation or cycle.
5. Ease of Use and Automation
- User Interface: Choose machines with intuitive controls and easy-to-use software.
- Automation Capabilities: Consider if the machine can be integrated into automated production lines and if it supports CNC controls for more complex operations.
6. Cost and Budget
- Initial Cost: Evaluate the purchase price and if it fits within your budget.
- Operating Costs: Consider ongoing costs such as maintenance, power consumption, and tooling.
7. Machine Footprint and Space Requirements
- Size: Ensure you have enough space in your workshop or production area for the machine.
- Accessibility: Consider the ease of access for maintenance and operation.
8. Manufacturer and Support
- Reputation: Research manufacturers' reputations for quality and reliability.
- Warranty and Service: Check the warranty period and availability of customer service and technical support. Aa a a well-known manufacturer of sheet metal processing equipment, Krrass provides professional installation and commissioning services to ensure that customers can smoothly start using the equipment after purchase and 2-years warranty is provided.
9. Safety Features
- Safety Standards: Ensure the machine complies with relevant safety standards and regulations.
- Safety Features: Look for features such as emergency stops, protective guards, and sensors.
10. Customer Reviews and Case Studies
- User Feedback: Read reviews and testimonials from other users to understand the machine's performance in real-world applications. You can click here to visit user comments.
- Case Studies: Look for case studies or examples of similar businesses using the machine successfully. Click here read more buyer cases.
V Grooving Machine For Sale Price
The price of a V grooving machine for sale can vary widely depending on its specifications, brand, and capabilities. Here is an overview of the price ranges for different types of V grooving machines:
- Manual V Grooving Machines:
- Uses: Suitable for small-scale projects and materials like plastic or light metals.
- Price Range: Approximately $500 to $2,000 USD.
- Semi-Automatic V Grooving Machines:
- Uses: Ideal for medium-scale production, offering more precision and efficiency than manual machines.
- Price Range: Approximately $3,000 to $10,000 USD.
- Fully Automatic V Grooving Machines:
- Uses: Designed for high-volume industrial use, capable of handling heavy-duty materials with high precision.
- Price Range: Approximately $10,000 to $50,000 USD or more, depending on the specific features and capabilities.
- CNC V Grooving Machines:
- Uses: High-precision machining for complex and large-scale production tasks, often used in industries like automotive and aerospace.
- Price Range: Approximately $20,000 to $100,000+ USD, based on the level of automation, size, and additional features.
V Grooving Machine For Sale - Top 5 Manufactures
1. Star “V” Machinery Ltd.
Star “V” Machinery Ltd. began producing groove machines in 1994. The founders took almost 30 years of combined experience to start engineering and manufacturing their products.
It only took seven years of development to create 11 unique V-groovers. The equipment is useful for many applications. It works with engineered stone, speakers, millwork, and more.
Eight different V-grooving machines are available for the solid-surface industry. The remaining designs are for fixtures, cabinets, and displays.
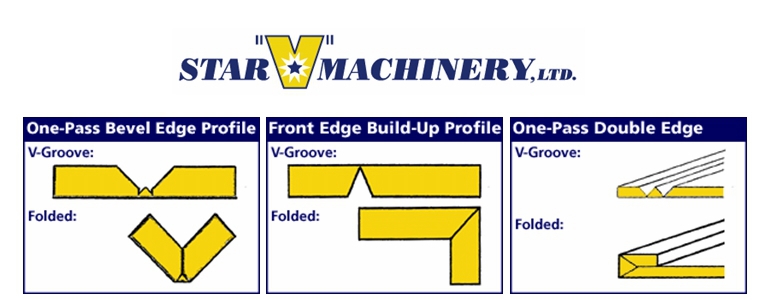
2. Krrass Machinery
Krrass is one of the world’s top CNC grooving machine producers. Their reputation involves manufacturing high-quality equipment for reasonable prices that meet global safety standards.
Their CNC V-grooving machine designs are some of the best in the global industry today. Anyone who needs auxiliary equipment cuts or sheet metal bending can find a solution here. This manufacturer offers two grooving machine solutions. You can choose from a horizontal or a vertical model.
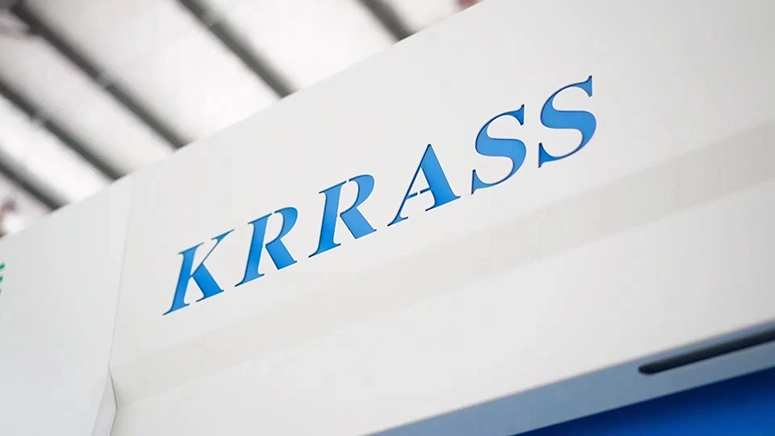
3. JMTC
JMTC manufactures, distributes, and supplies groove machines and similar equipment. Any work that involves cutting, pressing, or bending can benefit from their innovative approach.
Jeet Machinery Tools Corporation started offering services in 1967. Every unit produced by the company meets or exceeds international quality standards. The goal is to provide innovative technology with advanced automated features to simplify operator labor.
JMTC is headquartered in Delhi. Their extensive experience produces high-performance options at competitive prices.
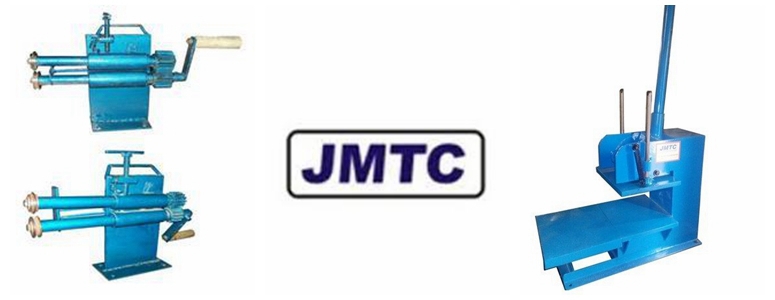
4. RIDGID Tool Company
RIDGID Tool Company has become a household name around the world. The manufacturer produces a broad range of tools to use in several applications. Everything from vacuum cleaners to power drills is in their portfolio.
For operators in India, RIDGID is a top supplier of roll grooving machines. The precision offered in their manufacturing process ensures that the highest quality materials are used. This emphasis combines with a commitment to craftsmanship to create a world-class product.
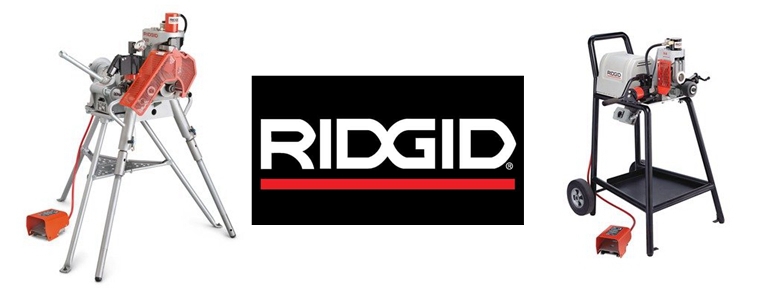
5. Copier Pipe Machinery USA
Copier Pipe Machinery USA offers several pipe roll grooving options for operators today. Their business started in 1997, providing automated choices for grooves at both pipe ends. You can find pile roll grooving machines offered at competitive prices. Operators can secure roller benches for their work using the knowledge and custom design solutions included with each unit. The machines groove from the outside to the inside. This design supports modern irrigation and sprinkler piping purposes.
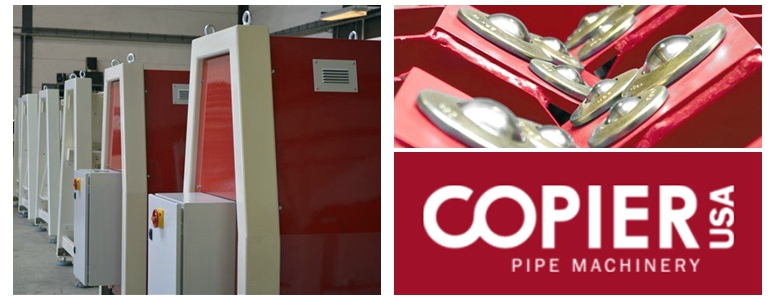
Krrass V Grooving Machine For Sale
Krrass is a prominent manufacturer in the sheet metal processing industry, known for its innovative and high-quality machinery. Among its extensive product lineup, Krrass's V grooving machines stand out for their precision, reliability, and efficiency. These machines are designed to create precise V-shaped grooves in sheet metal, which are essential for various applications, including architectural metalwork, automotive components, and custom metal fabrication.
The V grooving machines by Krrass are equipped with advanced features such as CNC control, adjustable grooving depth, and high-speed operation, ensuring optimal performance and superior finish. With a commitment to excellence and cutting-edge technology, Krrass continues to be a trusted name for professionals seeking top-tier metalworking solutions.