A tandem press brake is a sophisticated machine setup designed to enhance the capabilities of traditional press brakes by combining two or more machines to work in conjunction. This configuration allows for bending longer or larger sheets of metal that a single press brake might struggle to handle. Here’s a comprehensive guide to understanding tandem press brakes
Why You Need A Tandem Press Brake
In a fabricator shop, maintaining relationships with various contractors, each with unique needs, is crucial. As a result, the ideal setup for a hydraulic press brake might not always align with the diverse requirements of different projects.
At times, you may face challenges when asked to produce parts that don't fit any of your current press brake configurations. For instance, a standard press brake might meet the tonnage requirements but fall short in handling longer parts due to limitations in the center platform’s length.
This can be problematic if you're striving for accuracy and efficiency. You have two main options: invest in a larger press brake that can handle these larger parts or use two smaller press brakes in tandem.
Purchasing a larger press brake can be costly, impacting the profitability of your business. Therefore, using tandem press brakes is often a more cost-effective solution. In this article, we will explore what a tandem press brake is and highlight the top six benefits of using it to streamline your operations.
What is a Tandem Press Brake?
A tandem press brake is a highly efficient and versatile type of press brake machine designed for the fabrication and manufacturing of large and thick sheet metal components. With its unique design of two or more press brakes working together in tandem, it offers exceptional bending capacity and flexibility in the manufacturing process.
By working in unison, tandem press brakes can handle a wider range of materials and offer greater precision and accuracy in the bending process. With its increased productivity and efficiency, the tandem press brake is an essential tool for businesses seeking to take their manufacturing process to the next level.
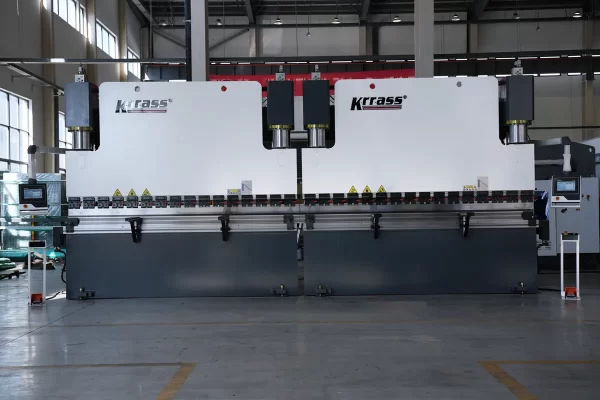
How Does a Tandem Press Brake Work?
A tandem press brake setup involves using two or more press brakes in alignment to handle larger or longer workpieces than a single press brake might be able to accommodate. Here’s a step-by-step explanation of how tandem press brakes work:
1. Configuration and Alignment
- Setup: In a tandem press brake setup, two or more individual press brakes are arranged side by side or in a specific configuration to work together on a single workpiece. The alignment is crucial to ensure seamless bending across the entire length of the metal sheet.
- Synchronization: The press brakes are synchronized via a central control system or software that coordinates their operations. This ensures that both machines perform bending actions in perfect harmony.
2. Loading the Material
- Sheet Placement: The metal sheet or plate is loaded onto the worktables of the press brakes. It is positioned carefully to ensure it spans across both machines if required.
- Securing the Workpiece: The material is secured in place, typically using clamps or other holding mechanisms, to prevent movement during the bending process.
3. Bending Operation
- Control Input: The operator inputs the bending parameters into the central control system. These parameters include the bending angles, lengths, and other specifications.
- Simultaneous Bending: Both press brakes perform their bending actions simultaneously or sequentially, depending on the required bend and the part's length. The synchronized operation ensures that the bending is consistent and accurate across the entire length of the workpiece.
4. Precision and Coordination
- CNC Controls: The central CNC control system manages the operation of both press brakes. It ensures that the bending actions are coordinated and that the machines work together without misalignment or errors.
- Accuracy: Advanced control systems, including backgauges and linear encoders, ensure precise bending by monitoring and adjusting the position of the metal sheet and the bending dies.
5. Unloading the Finished Part
- Completion: Once the bending process is complete, the finished part is carefully removed from the worktables.
- Inspection: The part is inspected for accuracy and quality to ensure it meets the required specifications.
Advantages of Tandem Press Brakes
- Extended Capacity: Tandem press brakes allow for the processing of larger or longer workpieces that a single press brake might not be able to handle.
- Increased Productivity: By using multiple machines, production speed can be increased, and different parts can be produced simultaneously.
- Flexibility: The configuration can be adjusted to handle various sizes and types of workpieces, providing greater flexibility in production.
In summary, tandem press brakes work by using multiple press brakes in alignment to handle larger or longer materials. The key to their operation is the synchronization of the machines through a central control system, allowing for precise and coordinated bending of workpieces.
Advantages of Tandem Press Brake
Two—or more—press brakes can be coupled to work in tandem with each other, giving the user greater bending length without requiring either the extreme cost or the expanded space needed for a giant press brake.
With the advent of hydraulic press brake technology, along with the development of computer numeric controls (CNC for short), precise control of immense bending power went from a pipe dream to being established as the norm in the majority of serious metal fabrication shops. Tandem, trio and even quad brake configurations make use of CNC precision to synchronize the machines into an orchestra of metal-bending perfection.
Components like linear encoders and press brake scales constantly gauge the exact positions of each ram and relay that data to the control so it can appropriately coordinate the Y1 and Y2 positions of all rams. Just as a single CNC press brake harmonizes both sides of a ram by reading two scales, tandem, trio and quad brake controllers read four, six or eight scales and accurately control the depth of all points along the combined ram.
The added requirements of proper calibration at set-up and very strict maintenance to keep all machines running at the same level of efficiency are offset by the incredible versatility brought by using press brakes in compound arrangements.
Benefits of Multiple Brake Configurations
While there are some limitations to using multiple press brakes, such as the depth of each machine potentially interfering with bending wider parts, there are several significant advantages to this setup:
1. Installation: Tandem press brakes are often more cost-effective and have a smaller footprint compared to a single large press brake. Installing a massive press brake typically requires major facility modifications, including potentially pouring a reinforced foundation and constructing a new building around the machine. In contrast, multiple smaller press brakes are easier to install, requiring no specialized rigging and minimal facility alterations.
2. Speed: Smaller press brakes in tandem can complete bending operations more quickly than a single large press brake. For a shop focused on maintaining high productivity, the increased speed of multiple machines can significantly enhance overall efficiency.
3. Flexibility: Many multiple brake configurations come with individual controls, allowing them to be operated separately when needed. A single CNC station manages tandem operations, but each press brake can also be controlled independently. This setup enables the production of different smaller parts simultaneously, effectively doubling output.
4. Accuracy: While all CNC hydraulic press brakes are precision tools, larger machines may have slightly less precise control. Using multiple smaller press brakes allows for finer control with each machine equipped with its own hydraulic valves, scales, and linear encoders. This configuration enhances the overall accuracy of the bending process.
5. Sharing: In multiple brake setups, programming for part bending can be shared among the machines. Only one CNC needs to be programmed for a part, and all the brakes can then produce that part. This streamlines the programming process and ensures consistency across the machines.
6. Downtime Management: If one press brake in a tandem setup goes down for maintenance or repairs, the other machines can continue to operate. This minimizes downtime and allows production to continue on other projects, maintaining shop productivity even when one machine is out of commission.
Overall, using multiple press brakes offers significant advantages in terms of installation, speed, flexibility, accuracy, programming efficiency, and downtime management. These benefits can enhance productivity and operational efficiency in a fabrication shop.
Disadvantages of Tandem Press Brakes
Complex Setup and Calibration: Ensuring perfect synchronization between the two machines can be challenging. It requires precise calibration and regular maintenance to maintain accuracy.
Higher Initial Investment: The cost of purchasing and setting up two synchronized machines can be higher than a single long press brake. However, this can be offset by the increased flexibility and productivity.
Space Requirements: Tandem press brake setups can require more floor space, which might be a constraint in smaller workshops.
Tandem Press Brake Purchase Guide
To purchase tandem type, you must know clearly the needs of the machine purchase, the scope of application, and the improvement of production efficiency and material handling.
The aspects can be used to judge whether single bending machine is good or tandem bending machines are more suitable:
– Flexibility
If there are two 500-ton, 6-meter tandem CNC press brakes in a workshop, we can produce not only 12 meters length sheet metal, but also two machines can be used independently.
For example, the length of the work piece is not more than 6 meters, the production can be double increased.
As the market continues to change, the processing business also continue to change. The tandem light pole press brake provides flexibility and has more business options.
– Risk Aversion
Choosing CNC tandem press brake machine can effectively avoid risks. When one machine breaks down and it is too late to repair, the other machine can continue to be used.
– Speed
Two single machines are faster than one large press brake. When we bend shorter parts, which shorter than one single press brake machine, Production speed must increase a lot.
– Machine costs
The price of two combined single CNC press brake machine usually is cheaper than a large, custom machine.
Technical Processes
Preparation and Setup
To ensure optimal performance of tandem press brakes, precise alignment and configuration are crucial. Begin by carefully positioning the press brakes so that their worktables are perfectly level and aligned. This alignment is essential to ensure that the bending dies across both machines work on the same plane, facilitating accurate and consistent bends across the entire length of the workpiece. Next, configure the central control system to manage both press brakes. This setup involves programming the machines to operate either in perfect synchrony or in a specific sequence based on the bending requirements. Proper configuration allows for coordinated bending actions, ensuring that both press brakes work seamlessly together to produce high-quality parts. This meticulous alignment and configuration process is key to achieving efficient and precise results in tandem press brake operations.
Material Handling
Proper material handling is essential for effective tandem press brake operation. Start by accurately positioning the metal sheet or plate onto the worktables of both press brakes, ensuring it extends across the full length of the machines if necessary. Secure the material using clamps, pneumatic hold-downs, or other fixtures to prevent any movement during the bending process. This secure positioning is critical to maintaining alignment and consistency throughout the bending operation. By ensuring that the material is properly loaded and fixed, you set the stage for precise and reliable bending results.
Bending Process
During the bending process, enter the specific bending parameters into the central control system, including bend angles, lengths, and material thickness. The system coordinates the bending actions of both press brakes, synchronizing their movements to achieve the desired bends without misalignment. Depending on the part’s design and length, the press brakes may perform bending operations simultaneously or sequentially. For longer parts, the machines may handle the bending in sections, with careful coordination to ensure seamless transitions. This synchronized operation ensures that bends are accurate and consistent across the entire workpiece.
Precision Techniques
Precision techniques are vital for ensuring high-quality results in tandem press brake operations. Utilize the CNC (Computer Numerical Control) system to achieve precise control over the bending process. The CNC system manages the positioning of backgauges, ram movements, and die alignments to ensure accurate bends. Advanced backgauge systems, often with multiple axes, provide precise positioning and adjustments, while linear encoders monitor the exact position of the ram and dies. These technologies collectively ensure that the bending process is executed with high precision, resulting in accurate and consistent workpieces.
Quality Control
After completing the bending process, perform a thorough inspection of the workpiece to verify accuracy and quality. Check dimensions, bend angles, and overall alignment to ensure that they meet the specified requirements. Based on the inspection results, make any necessary adjustments to the CNC programming or machine alignment to address discrepancies and fine-tune the process. This diligent quality control step helps maintain high standards and ensures that the finished parts meet the desired specifications.
Maintenance and Troubleshooting
Regular maintenance and effective troubleshooting are essential for maintaining optimal performance of tandem press brakes. Perform routine maintenance tasks, such as checking hydraulic systems, calibrating machines, and cleaning components, to keep the press brakes in good working condition. Address any operational issues or inconsistencies promptly to minimize downtime and ensure continuous production. By staying on top of maintenance and troubleshooting, you can prevent potential problems and maintain the efficiency and reliability of your tandem press brake setup.
Conclusion
Large press brakes are often less ideal due to their challenging installation and maintenance requirements. Additionally, the larger ram size can make it difficult to achieve precise bending results. Tandem press brakes address these issues by providing an advanced solution that overcomes the limitations of large press brakes.
If you're seeking a reliable provider, KRRASS stands out as a leading manufacturer of Tandem Press Brakes. Their machines are designed to deliver exceptional performance in the fabrication and manufacturing industry. The KRRASS Tandem CNC Press Brake features advanced components such as the CE LazerSafe LZS-XL tandem adapter and linear encoders, enhancing the speed and efficiency of bending long or wide parts. Contact us today for more information.
Reviewed by 1 user
It is an amazing press break!! we need the tandem press brake to effectively avoid risks